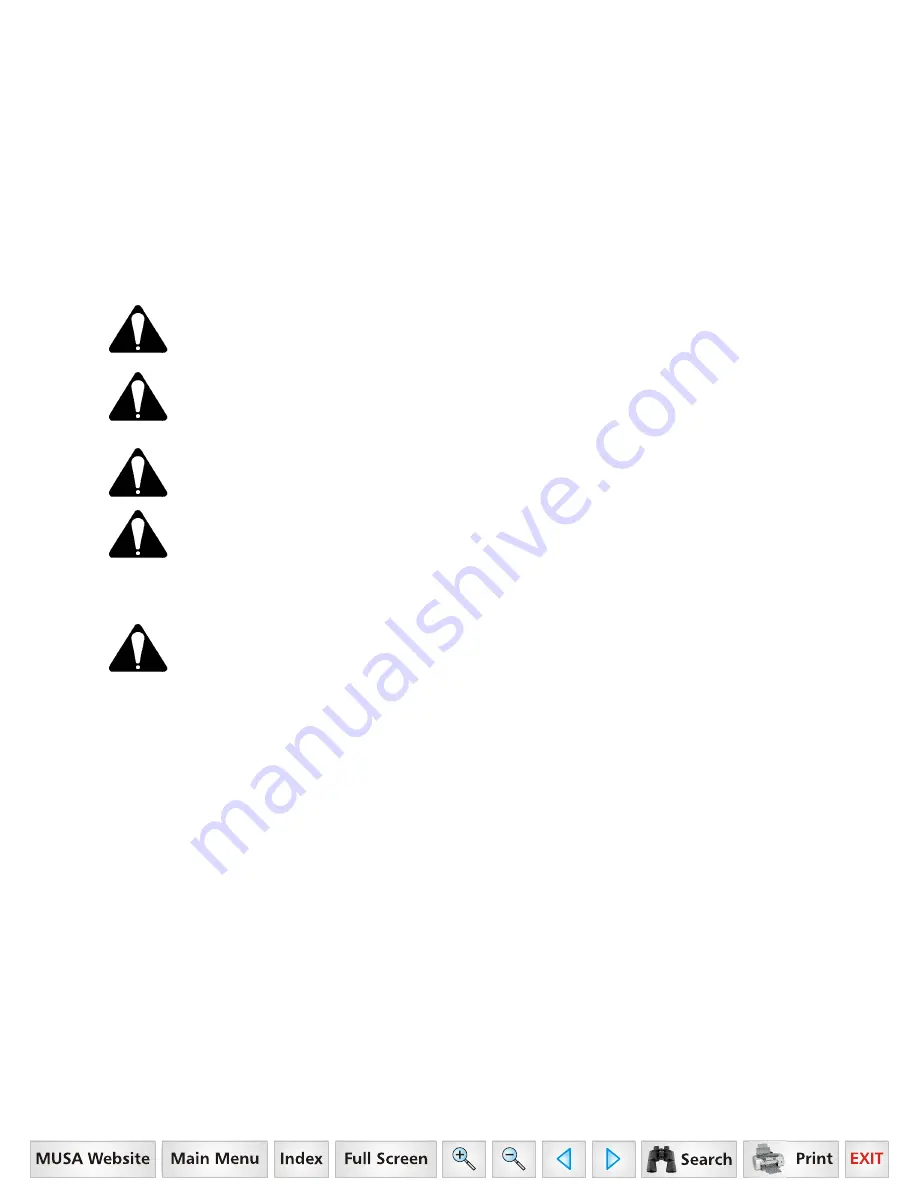
14
LOADER OPERATION
Transporting a Loaded Bucket
Transport material with the bucket as low as possible to prevent spilling and keep maximum
stability. The loader must be in a position that will not block the operators’ vision. A loaded
bucket must not be transported in the upright position or at excessive speed.
Observe the following safety warnings when transporting a loaded bucket.
CAUTION: When using a loader, be aware of bucket location at all times.
When raising a loader with bucket rolled back, material can dump onto
tractor causing damage to tractor or injury to operator.
WARNING: Contact with overhead power lines can cause severe
electrical burns or death from electrocution. Make sure there is
clearance between raised equipment and overhead power lines.
CAUTION: Stop the loader arms gradually when lowering or lifting.
WARNING: A loaded Bucket should be transported in a low position at
low ground speeds. Make turns slowly and use the tractor brakes
cautiously. A full bucket in the raised position alters the center of
gravity location of the machine and increases the possibility of
accidents.
CAUTION: Do not stand, walk or work under a raised loader unless it is
securely blocked or held in position. Accidental movement of a control
lever or leak in the hydraulic system could cause the loader to drop, or
attachment to dump, resulting in serious injury or death.
Important:
Contaminates in hydraulic oil can cause valve spools to stick. Be alert when operating loader
and follow your Tractor Operator’s Manual maintenance schedule.
Scraping
When scraping, the float position must be used to keep the bucket on the ground and at the
same time let the bucket follow ground contours. The bucket must be kept level to the ground
during scraping operations.
Backfilling/Backgrading
When “Backfilling” or “Backgrading”, position the bucket so it is level on the ground. Do not
dump material from bucket following each pass, as additional weight of material in bucket will
assist in “Backgrading” and increases loader efficiency during “Backfilling”.
Controlled Rate of Loader Functions
By “feathering” the control lever, reduced operational speeds can be controlled. This action
controls the position of the valve spool in the valve body and regulates flow of oil to/from
cylinders. It is important to utilize this operational practice when lowering loader boom when the
bucket is loaded with material.
1
6
Series, Model - 2
816