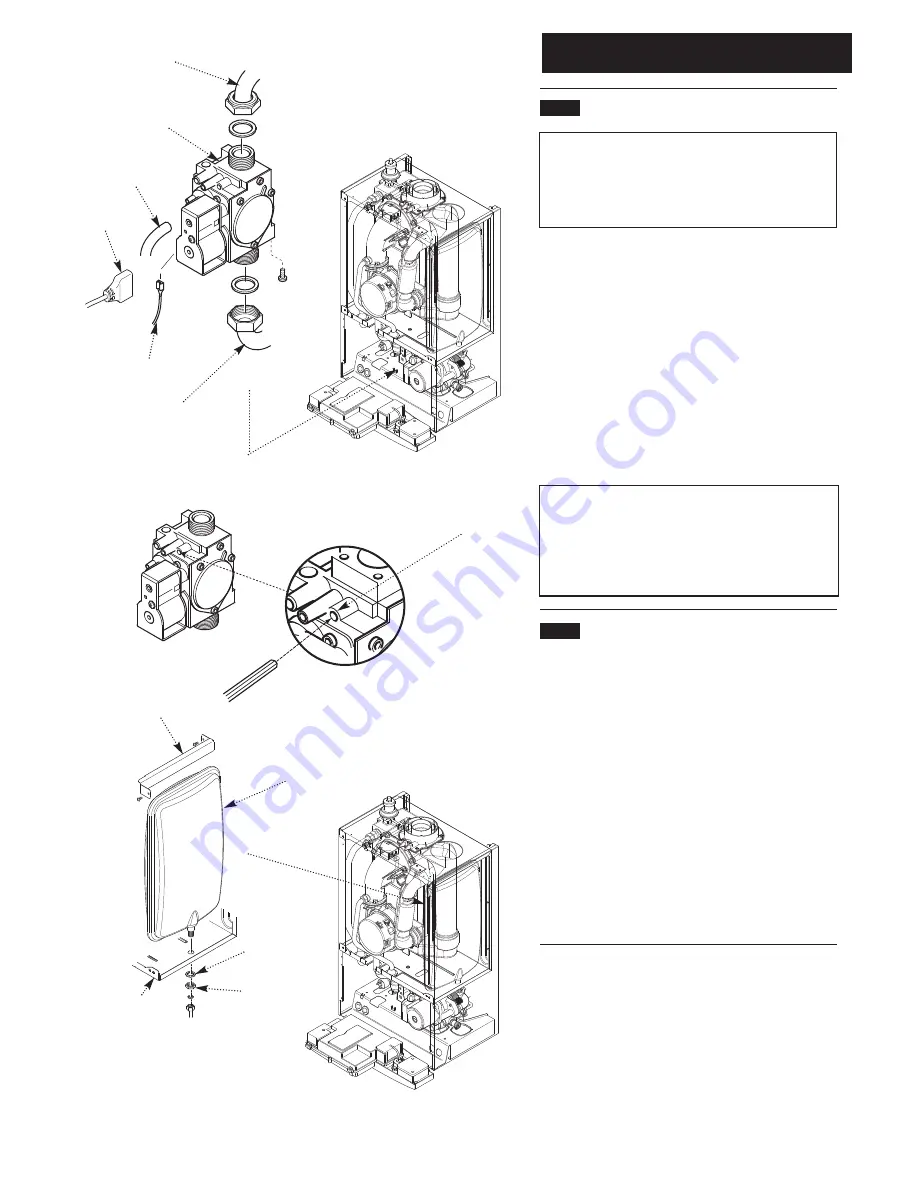
48
14.0 Changing Components
© Baxi Heating UK Ltd 2014
14.22
Gas Valve (Fig. 99)
IMPORTANT: After replacing the valve the CO
2
must be
checked and adjusted as detailed in Section 15.0 Setting
the Gas Valve. Only change the valve if a suitable
calibrated combustion analyser is available, operated by a
competent - see section 13.1.
1. Turn the gas cock off and undo the nut on the gas feed
elbow under the boiler.
2. Remove the screws securing the gas valve to the boiler
bottom panel.
3. Pull off the power lead, earth lead and sensing pipe.
4. Undo the nut on the gas pipe at the gas/air inlet and the gas
valve. Remove the pipe, taking care not to lose the sealing
washers. Remove the valve.
5. Reassemble in reverse order., ensuring that all seals are in
place and the injector is fitted.
NOTE:
To assist the boiler to light prior to final setting,
use a suitable hexagon key to wind out the Throttle
Adjustment Screw until it is flush with the valve body, then
turn the screw 4 full turns clockwise (Fig. 99a). If the boiler
will not light, or the correct CO
2
cannot be achieved
contact the ‘heateam’ technical helpline.
14.23
Expansion Vessel (Fig. 100)
1. Drain the boiler primary circuit and undo the nut on the
vessel connection pipe.
2. Remove the screw retaining the air inlet pipe, and swing the
pipe to one side.
3. Undo and remove the locknut and spring washer securing
the vessel spigot to the boiler lower panel.
4. Remove the bracket and vessel from the boiler.
5. Locate the retaining bracket on the upper flange of the new
vessel and fit to the boiler.
6. Examine the sealing washer, replacing if necessary, and
reassemble in reverse order.
Gas Valve
Gas Feed
Elbow
Fig. 99
Earth Lead
Expansion Vessel
Boiler Chassis
Lock Nut
Spring
Washer
Fig. 100
Retaining Bracket
Sensing Pipe
Venturi Inlet
Pipe
Power Lead
Fig. 99a
Throttle
Adjustment Screw