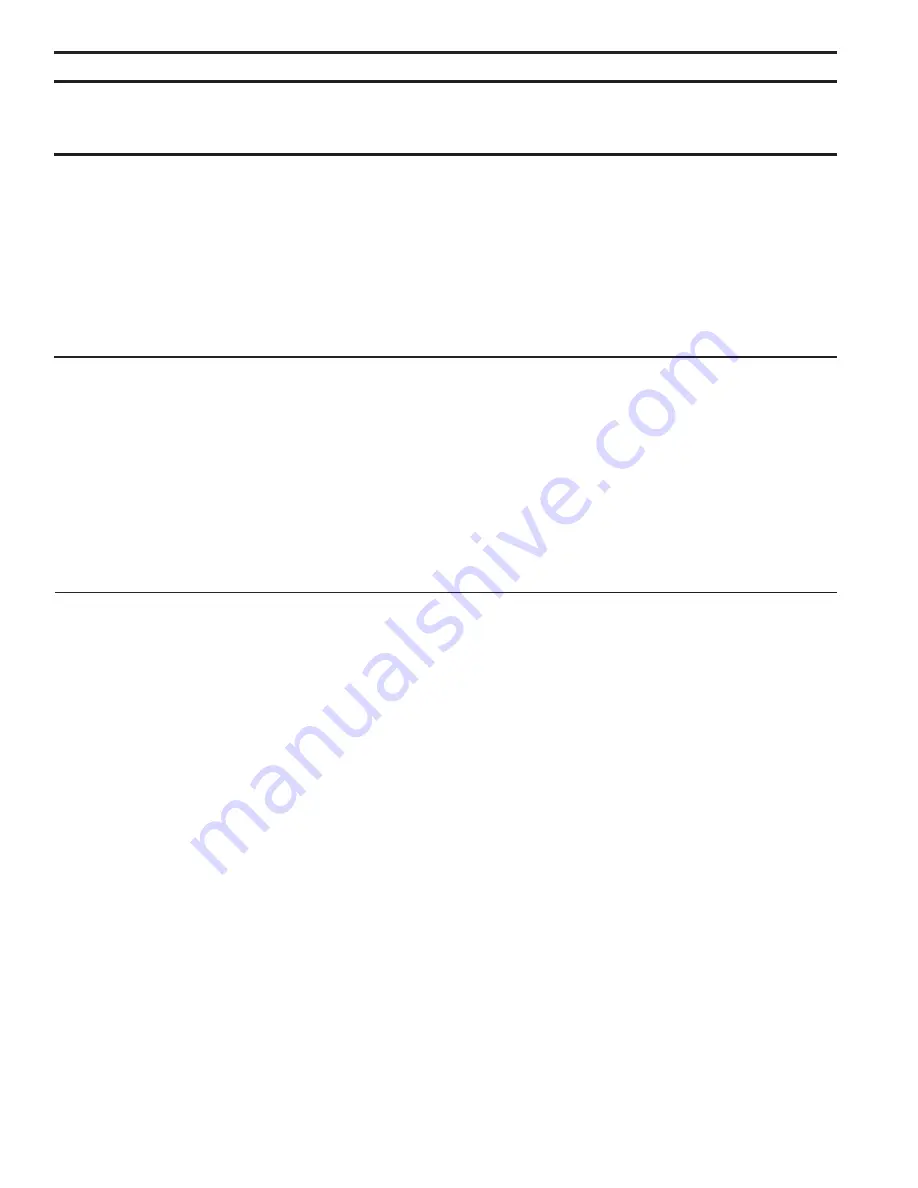
4
53D0419
DV6000 Gas Fireplace
trouBleshootInG
standInG pIlot IGnItIon
syMptoM
possIBle cause
actIon
1. Spark ignitor will
not light pilot after
repeated triggering of
piezo.
. Pilot will not stay lit
after carefully follow-
ing lighting instruc-
tions.
3. Pilot burning, valve
knob turned to “ON”,
switch is turned to
“ON” or “RS”, but
burner will not ignite.
A. Wire disconnected.
B. Defective ignitor.
C. No gas or low gas pres-
sure.
D. No Propane/LPG in tank
A. Defective thermocouple
B. Defective valve
A. Defective switch, wall
switch, remote control or
wire
B. Pilot flame too small
C. Defective or malfunction-
ing thermopile
D. Defective valve
A. Open door and check to make sure wire is connected
to ignitor.
B. Check for spark at electrode and pilot. If no spark and
electrode wire is properly connected, replace pilot
assembly.
C. Check remote/manual shut off valve from fireplace.
Low pressure can be caused by bent lines, restricted
lines, low pressure line pressure. Consult with plumber
or gas supplier.
D. Check Propane/LPG tank. Refill tank.
A. Check that thermocouple flame impinges on thermo-
couple. Clean and/or adjust pilot for maximum flame
impingement. Ensure that the thermocouple connec-
tion at the gas valve is fully inserted and tight.
Disconnect the thermocouple from the valve, place
one millivolt lead wire on the tip of the thermocouple
and the other meter lead wire on the thermocouple
copper lead. Start the pilot and hold the valve knob in.
If the millivolt reading is less than 15 mV, replace pilot
assembly.
B. If thermocouple is producing more than 15 mV,
replace faulty valve.
A. Check switch and wire for proper connection. Place
jumper wires across terminals of switch. If burner
comes on, replace defective switch.If the switch is OK,
repeat the same procedure on remote control If burner
comes on, replace remote control.
Place jumper wire across wire at gas valves (terminals
marked TH and TP/TH). If burner comes on, wires are
faulty or connections are bad. Replace wire.
B. If pilot flame is not close enough to the thermopile,
adjust pilot flame.
C. Check thermopile wire connections to make sure
all are tight and that the thermopile is fully inserted
into pilot assembly. Check thermopile with a millivolt
meter. Connect leads to TP and TP/TH terminals on
the control valve. If meter reading is below 35 mV,
replace pilot assembly.
D. Turn valve knob to “On” and switch to “ON.” Take a
reading at the thermopile leads (TP & TP/TH) on the
valve. If the meter reads greater than 175 mV and the
burner does not light, replace defective valve.
Summary of Contents for DV6000
Page 52: ...52 53D0419 DV6000 Gas Fireplace...
Page 53: ...53D0419 DV6000 Gas Fireplace 53...