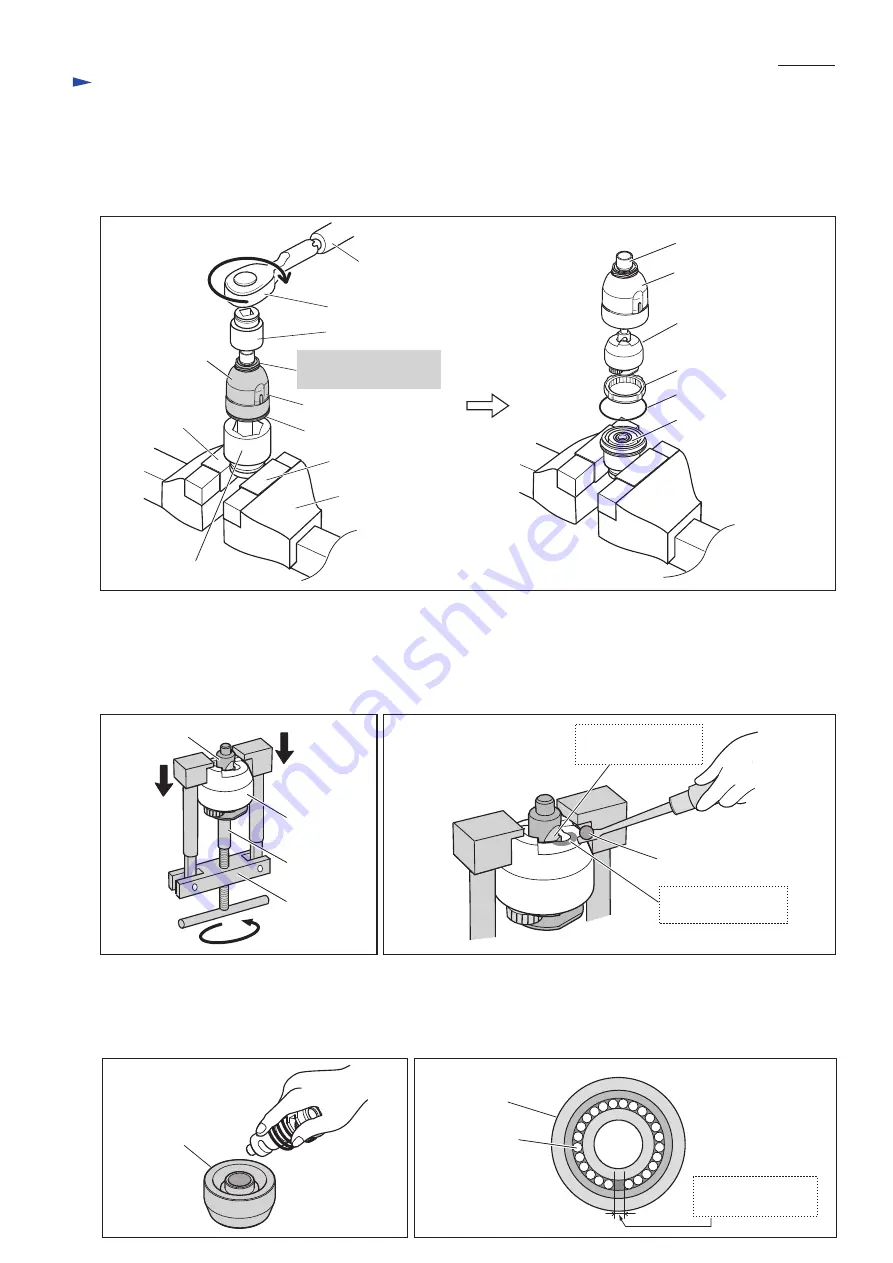
P
4
/
9
R
epair
[3] -1. Disassembling/Assembling Hammer Section (cont.)
top of cam groove
on Spindle
Steel ball 5.6
6) Install 1R346 on R045, and set them on Hammer mechanism as illustrated in Fig. 6.
Then turn the handle of 1R045 clockwise to lower Hammer to the full.
7) Align the notch in Hammer with the top of the cam groove on Spindle.
Then take Steel ball 5.6 (2 pcs) out of Spindle using tweezers or a slotted screwdriver magnetized with 1R288. (Fig. 7)
8) Remove 1R045 by turning the handle counterclockwise.
Fig. 7
Hammer
Spindle
1R346
1R045
Fig. 6
5) Attach a pair of 1R041 to vise. Fix Socket 32-50 in vise securely. Then put Hammer section on Socket 32-50
while fitting the hexagonal portion of Bearing box in Socket 32-50. Fit Socket 30-78 over the hexagonal portion of
Hammer case complete. Then, by turning Socket 30-78 clockwise with 1R223 and 1R224, Hammer section can be
disassembled as illustrated to right in Fig. 5.
Fig. 5
Hammer section
1R223
1R224
Socket 30-78
1R041
Vise
Socket 32-50
1R041
Bearing box
Internal gear 51
O ring 40
Bearing box
Hammer mechanism
Hammer case complete
Hammer case complete
Bit holder section
9) Remove Spindle, Compression spring 45 and Cup washer 14 from Hammer as illustrated in Fig. 8.
Important: Be sure to lower the Hammer side so that Steel balls in Hammer cannot fall down and scatter.
10) Steel ball 3.5 can now be removed from Hammer. There are twenty-four 3.5 Steel balls in the groove on the inside
of Hammer. (As illustrated in Fig. 9, the groove is designed to have a space equivalent to one 3.5 Steel ball.)
Fig. 9
Hammer
Steel ball 3.5
(24 pcs)
space equivalent to
one 3.5 Steel ball
Fig. 8
Hammer
notch for
Steel ball insertion
Fit Socket 30-78 over
this hexagonal portion.