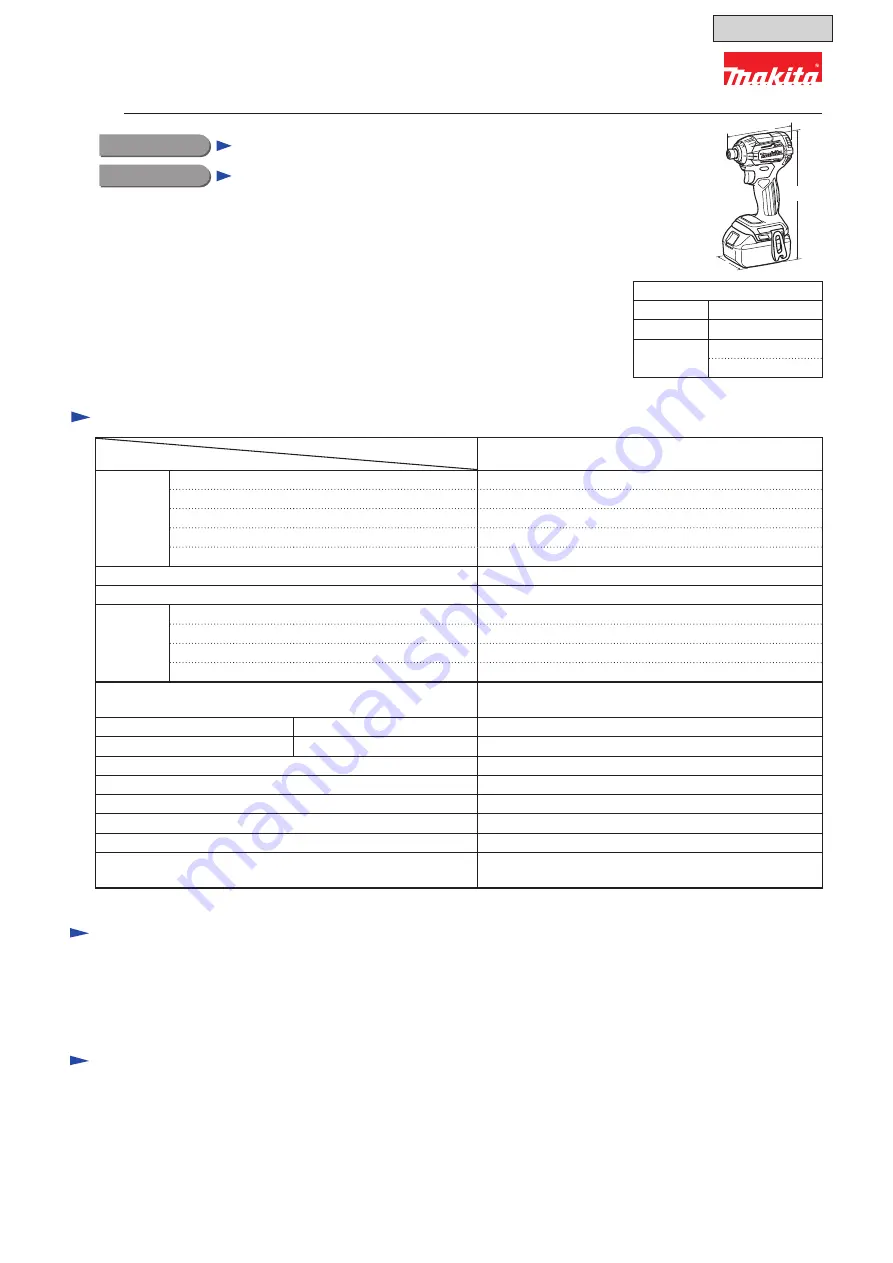
1 / 19
Model No.
Description
Cordless Impact Driver
DTD170
C
ONCEPT AND MAIN APPLICATIONS
Model DTD170 is our high-end Cordless impact driver powered
by 18V Li-ion battery and developed based on
the current model DTD148.
The main features and benefits are:
• More compact body (overall length: 117mm) than DTD148
• Electronic 4 stage impact power selection
• A mode [assist mode]
• Ergonomically designed handle with better control
S
pecifications
Model
Specifications
DTD170
Battery
Voltage: V
18
Capacity: Ah
1.5, 2.0, 3.0, 4.0, 5.0, 6.0
Energy capacity: Wh
27, 36, 54, 72, 90, 108
Cell
Li-ion
Charging time (approx): min
15, 24, 22, 36, 45, 55 with DC18RC
Max output (W)
290
Driving shank: mm (")
6.35 (1/4) Hex
Capacities
Machine screw
M4 - M8 (5/32 - 5/16")
Standard bolt
M5 - M16 (3/16 - 5/8")
High strength bolt
M5 - M14 (3/16 - 9/16")
Coarse-thread
22 - 125mm (7/8 - 4-7/8")
Impact power selection
Electronic 4 stage (Max/ Hard/ Medium/ Soft)
+ Teks screw mode + A mode [assist mode]
Impacts per min: min
-1
=ipm
Max/ Hard/ Medium/ Soft
0 - 3,800/ 3,600/
2,600/ 1,100
No load speed: min
-1
=rpm
Max/ Hard/ Medium/ Soft
0 - 3,600/ 3,200/ 2,100/ 1,100
Max tightening torque
*
3
: N·m [kgf·cm] (in·lbs)
175 [1,780] (1,550)
Electric brake
Yes
Variable speed control by trigger
Yes
Reverse switch
Yes
LED job light
Yes
Weight according to
EPTA-Procedure 01/
ver.2.1
: kg(lbs)
1.2 (2.7)
*
1
or 1.5 (3.3)
*
2
*3
Tightening torque at 3 seconds after seating, when tightening M16 (grade 10.9) high strength bolt
Dimensions: mm ( " )
Length (L)
117 (4-5/8)
Width (W)
79 (3-1/8)
Height (H) 218 (8-5/8)
*
1
236 (9-1/4)
*
2
*1
With Battery BL1815N, BL1820(B)
*2
With Battery BL1830(B), BL1840(B), BL1850(B),
BL1860B
Belt clip
Battery
*
5
Battery cover
*
6
Charger
*
5
Plastic carrying case
*
5
*5
Battery, charger and plastic carrying case are not supplied with “Z” model.
*6
Supplied with the same quantity of extra Battery.
Note:
The standard equipment may vary by country or model variation.
Phillips bits
Socket bits
Drill chucks
Drill bits with 6.35mm Hex shank
Bit piece
Stopper for impact driver
Hook set (Belt clip)
Tool catcher set
Battery protectors
Li-ion batteries:
BL1815N, BL1820(B),
BL1830(B), BL1840(B),
BL1850(B), BL1860B
Fast charger DC18RC
Two port multi fast charger DC18RD
Charger DC18SD/DC24SC
Four port multi charger DC18SF
Automotive charger DC18SE
S
tandard equipment
O
ptional accessories
H
W
L
July 2016
T
ECHNICAL INFORMATION
OFFICIAL USE
for ASC & Sales Shop