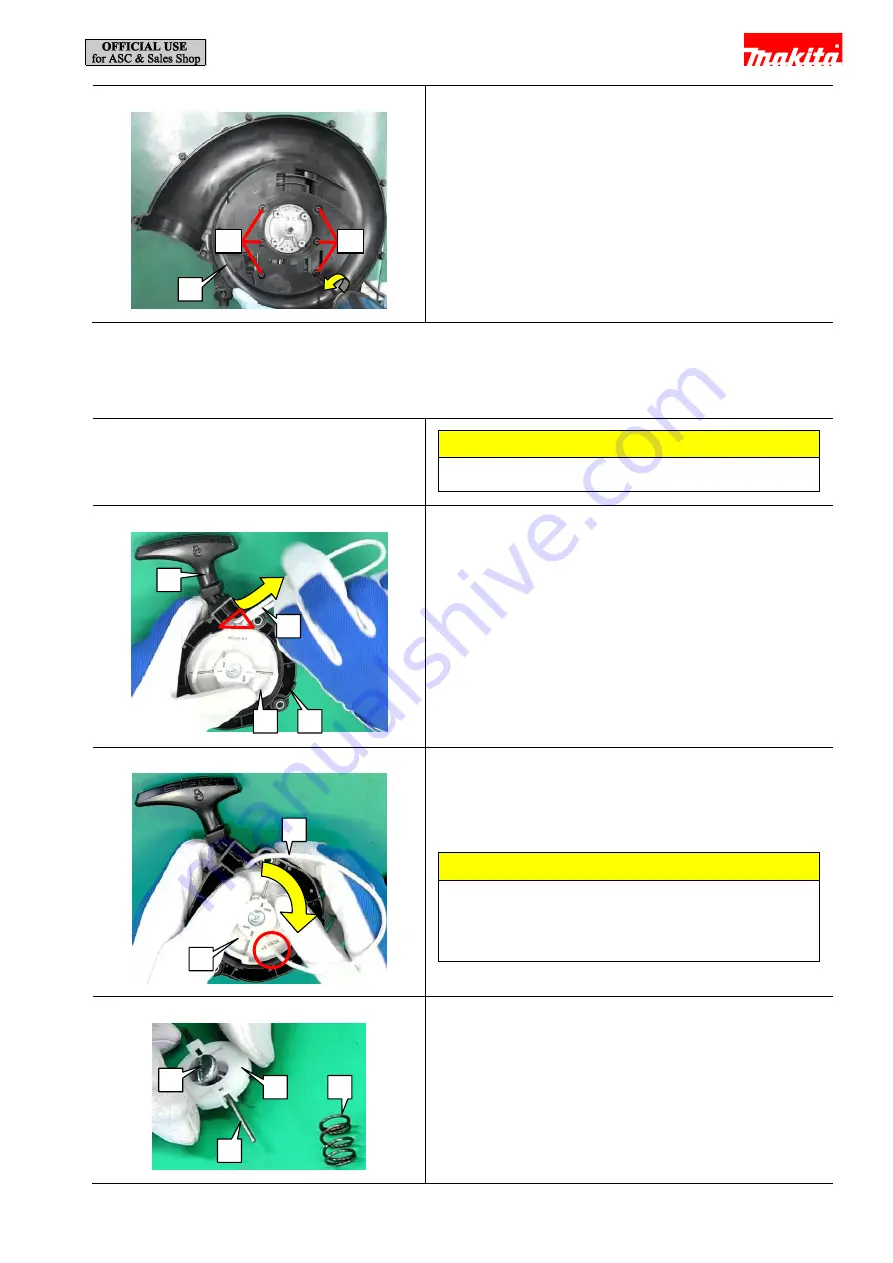
11 / 71
Fig. 21
14
Remove six M6x25 Hex socket head bolts [1] to
remove Front volute case [2].
4-3
Recoil starter
4-3-1
Disassembling Recoil starter
1
Follow Fig. 13 to remove Recoil starter.
Note
Be sure to wear leather gloves to protect your hands.
Fig. 22
2
Pull Starter knob [3] approximately 200mm, then hold
Reel [1] so that it does not rotate back and then pull out
Starter rope [4] from the triangular gap between Recoil
starter [2] and Reel [1].
Fig. 23
3
Hook Starter rope [1] on the U-shaped notch of Reel
[2], and then turn Reel [2] clockwise to release the
tension from Spiral spring.
Note
Once the tension is released from Spiral spring, do not
turn Reel [2] clockwise any further or Spiral spring will
be deformed.
Fig. 24
4
Remove Set screw [1] to remove Collar [2], Swing arm
[3] assembly and Friction spring [4].
[1]
[2]
[3]
[4]
[1]
[2]
[4]
[3]
[1]
[2]
[1]
[2]
[1]