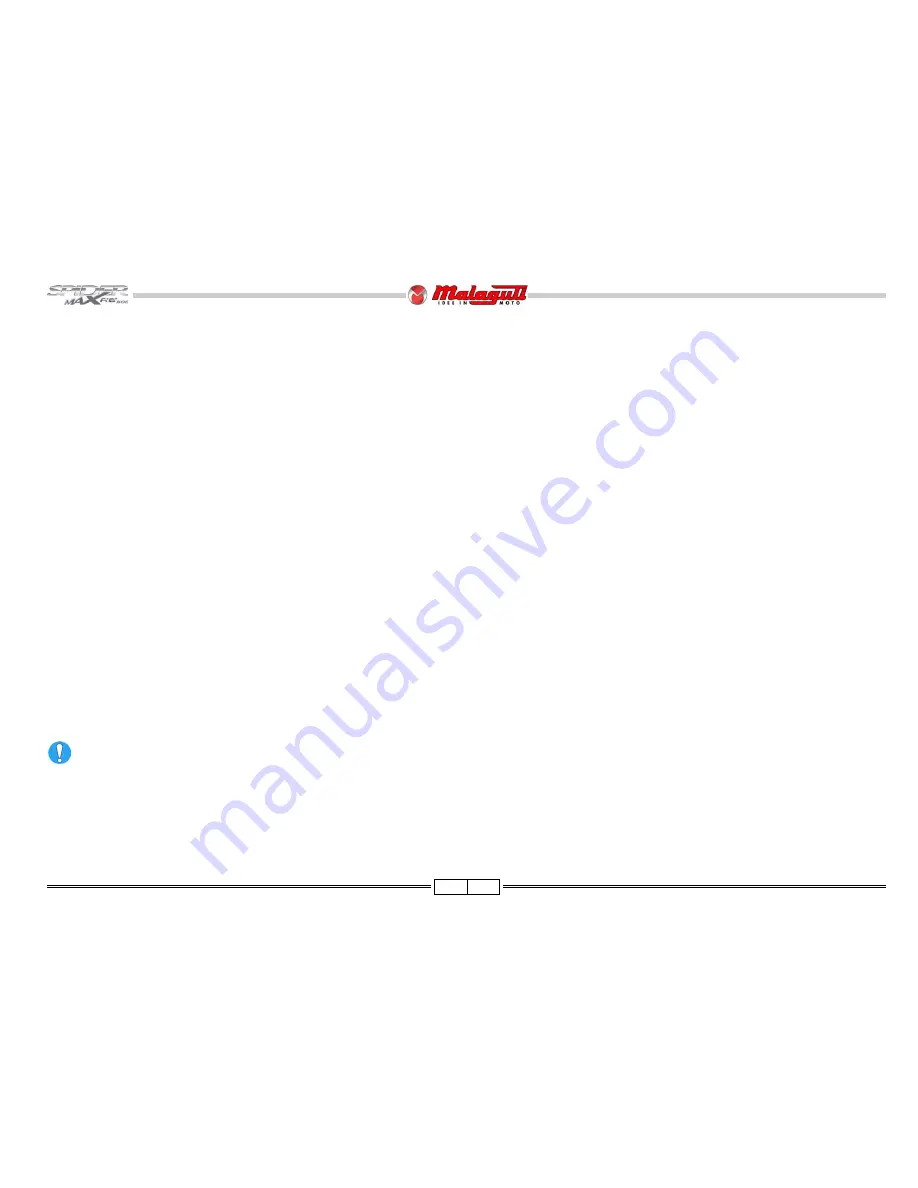
4
02/08
Before any servicing, make sure that the vehicle is perfectly stable.
The front wheel should preferably be anchored to fixture, which is integral with the lift platform.
GENERAL WORK PROCEDURES
• The recommendations given hereafter are aimed at ensuring maximum work safety as well as at considerably reducing the risk of accidents, personal injury, equipment
damage and idle times, and should therefore be strictly adhered to.
• Always listen with attention to the customer’s opinion and complaints about the motor-bike operation, asking specific questions in order to have a complete understanding of
all the symptoms and identify with good approximation the real causes of the trouble. The present manual provides the technical information and the basic indications on the
intervention procedures but these have to be integrated with the personal expertise.
• We suggest planning the service interventions in order to avoid any waste of time or downtime. Try to reduce as much as possible the operations necessary to reach the
components that needs repairing.
• Prepare the components that are likely to be replaced and all the original spare parts you may need.
• Use only the original spare parts.
• Mark the components that may be mis-placed during re-assembly operations.
• Only use quality tools and equipment.
• Only use equipment conforming to EU Directives for lifting the vehicle.
• During operations, always keep tools and equipment at hand, possibly laying them out according to the sequence in which they are to be used. Absolutely avoid putting them on the
vehicle itself, out-of-sight or in poorly accessible places.
• Always keep the work area neat and clean.
• When tightening screws or nuts, start with the larger diameter or inner fasteners, and tighten them in progressive “pulls” using a “criss-cross” pattern.
• The torque settings specified in the manual refer to the “final torque”, which must be attained progressively by steps.
• Preferably use open-end box wrenches by “pulling” and not “pushing”.
Summary of Contents for SPIDER MAX RS 500
Page 1: ......
Page 78: ...77 02 08 CABLE POSITIONING PIPE SYSTEM AND ANCHORING TIES F 198 F 199 ...
Page 79: ...78 02 08 F 200 ...
Page 80: ...79 02 08 F 201 ...
Page 81: ...80 02 08 F 202 ...