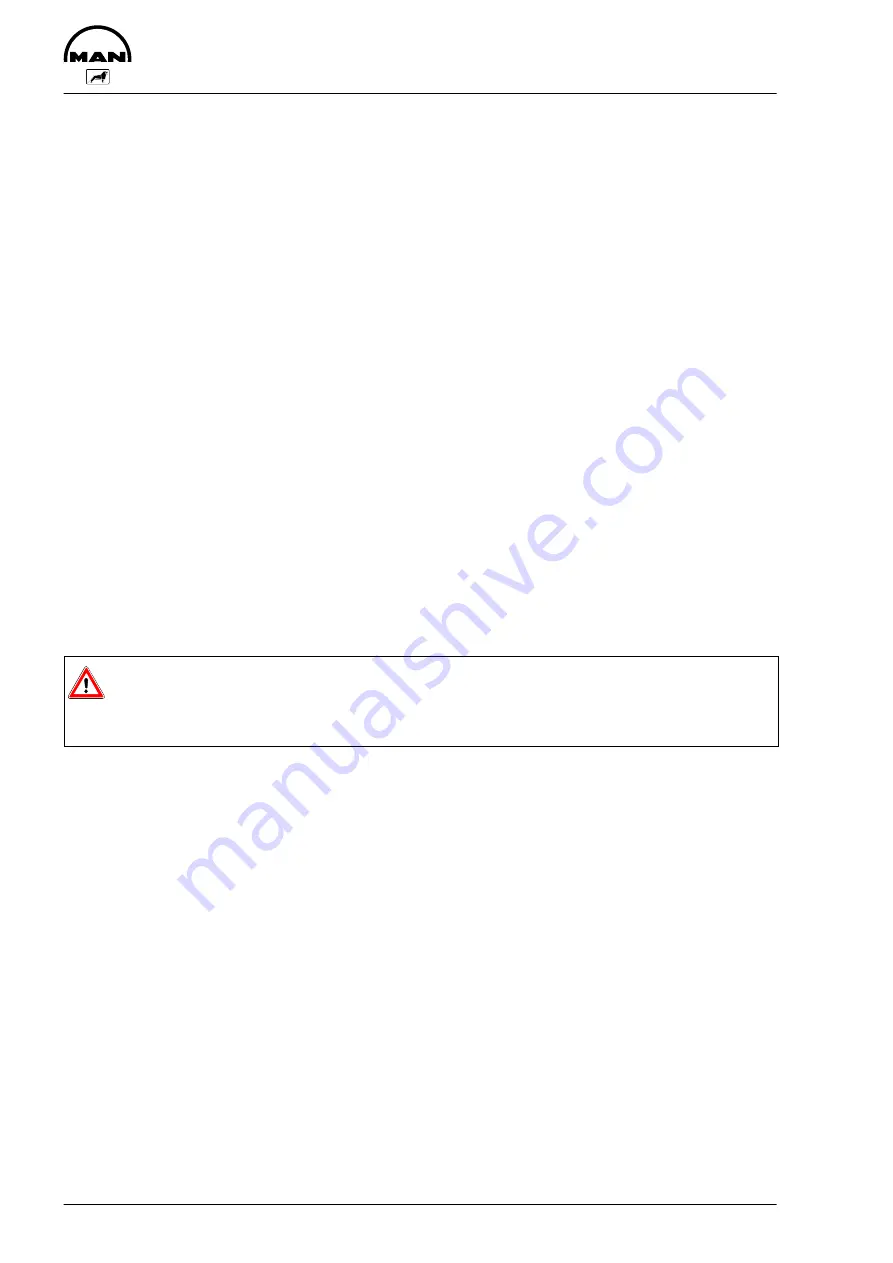
Turbocharger, troubleshooting
80
In the case of oil accumulation in charge-air lines and charge-air cooler
Slight oil accumulation due to oil spray in the charge-air system is a result of the design and is desirable.
The oil spray is required as lubrication of the inlet valve seats.
If more oil accumulates than is normal, i.e. to the extent that oil pockets develop e.g. in the lower air box of
the intercooler, this can lead to oil disintegration or uncontrolled engine racing when the oil is separated. In
such cases, remove the cause.
Possible causes:
- Oil overfilling of the engine
D
Check whether the correct dipstick and guide tube combination is fitted.
- Use of unsuitable engine oil (see brochure “Fluids and lubricants”)
- Operation of the engine on non-permitted inclines
- Excessive crankcase pressure, e.g. due to defective oil separator valve (crankcase breather) or piston
ring wear
Compressor coking
At permanently high charge-air temperatures, e.g. constant full-load operation.
Coking leads to a reduction in the charging pressure, but not to drops in power or poorer acceleration cha-
racteristics.
Coking can lead to increased exhaust haze.
In the case of compressor coking:
- Remove the compressor housing without tilting it
D
If it jams, the compressor wheel blades may get damaged or bent and the resulting imbalance may
destroy the turbocharger.
- Remove coking from the compressor housing using coke-dissolving cleaner
Danger:
Under no circumstances should cleaner be sprayed in while the engine is running
- ineffective
- danger of accident!
- In problem cases, use oil types that are less likely to lead to compressor carbonisation (see publication
“Fuels, Lubricants and Coolants for MAN Diesel Engines”).
Summary of Contents for D 2866 LUE 605
Page 1: ......
Page 2: ......
Page 14: ...Notes 12...
Page 19: ...Memoranda 17...
Page 20: ...Engine views 18 Engine views 3 4 2 1 7 6 5 8 11 10 9...
Page 68: ...Memoranda 66...
Page 133: ...131 Service Data...
Page 157: ...155 Special tools...
Page 158: ...Special tools 156 2 3 4 5 6 7 8 1 6 1 6 2 6 3 9 1 9 2 9 3 9...
Page 162: ...Special tools 160 21 22 25 25 2 24 25 1 26 27 1 27 2 27 20 1 19 2 19 1 20 2 19 20 23 28...
Page 164: ...Special tools 162 30 31 32 1 32 32 2...
Page 167: ...Special tools 165 Pressing mandel for cap dia 62 1 mm Pressing mandel for cap dia 50 1 mm...
Page 170: ...Notes 168...
Page 173: ......
Page 174: ......