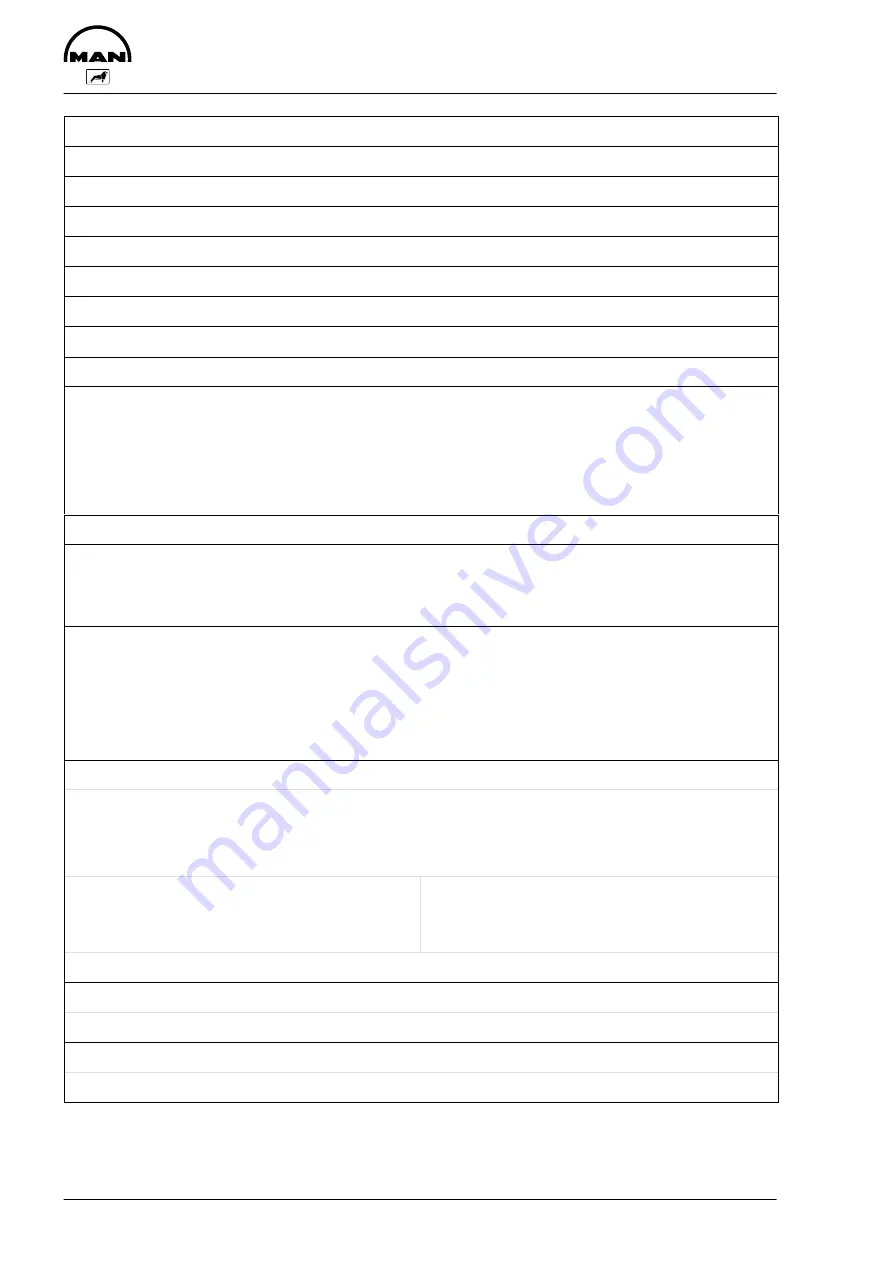
Technical Data
36
Model
E 0826 E 301 / 302
Design
in-line, vertical
Cycle
4-stroke Otto-cycle
Number of cylinders
6
Bore
108 mm
Stroke
125 mm
Swept volume
6,870 cm
3
Compression ratio
12,5 : 1
Speed
1,500 rpm
Rating
70 kW
Blocked ISO standard output as per ISO 3046 / part 7
Standard reference conditions: air temperature 298 K, air pressure 1,000 mbar,
humidity 30% for operation with natural gas (group H) with calorific value H
u
of
10 kWh/m
3
N
methane number
80
Firing order
1 - 5 - 3 - 6 - 2 - 4
Valve clearance (cold engine)
Intake
0,50 mm
Exhaust
0,50 mm
Valve timing
Intake opens
6
°
before TDC
Intake closes
38
°
after BDC
Exhaust opens
56
°
before BDC
Exhaust closes
12
°
after TDC
Engine lubrication
Force feed
Oil capacity in oil sump (litres)
min.
max.
16 l
20 l
Oil change quantity (with filter)
21 l
Oil pressure during operation (depen-
ding on oil temperature, oil visvosity
class and engine rpm)
must be monitored by oil pressure moni-
tors / gauges
Oil filter
Full-flow filter with paper filter elements
Engine cooling system
Liquid cooling
Operating temperature
80 / 88
°
C engine inlet / -outlet
Electrical equipment
Starter
24 V; 4 kW
Summary of Contents for E 0824 E 301
Page 1: ......
Page 2: ......
Page 14: ...Commissioning and operation 12 Engine views E 0824 E 301 302 1 2 3 4 5 6 7 8 9 10 11 12...
Page 16: ...Commissioning and operation 14 Engine views E 0826 E 301 302 1 2 3 4 5 6 7 8 9 10 11 12...
Page 35: ...Notes 33...
Page 41: ...39 Circuit diagrams...
Page 45: ...Notes 43...
Page 47: ......
Page 48: ......