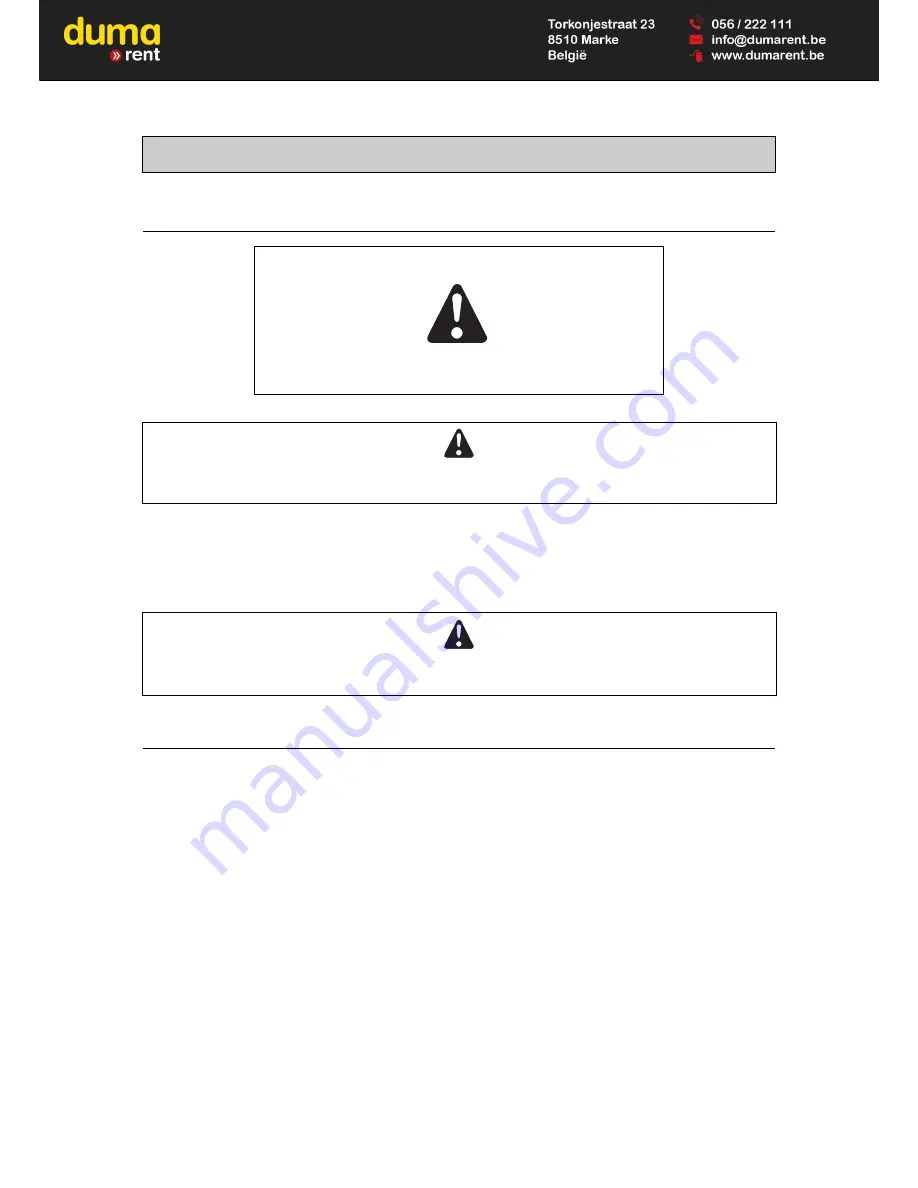
1 - 6
INSTRUCTIONS FOR THE OPERATOR
P
REAMBLE
The risk of accident while using, servicing or repairing your platform can be restricted if you follow the safety instructions and safety
measures detailed in these instruction.
- Only the operations and manœuvres described in these operator's manual must be performed. The manufacturer can-
not predict all possible risky situations. Consequently, the safety instructions given in the operator's manual and on the
platform itself are not exhaustive.
- At any time, as an operator, you must envisage, within reason, the possible risk to yourself, to others or to the platform
itself when you use it.
Failure to respect the safety and operating instructions, or the instructions for repairing or servicing your platform may lead to serious,
even fatal accident.
G
ENERAL INSTRUCTIONS
A - OPERATOR’S MANUAL
- Carefully read and understand the operator's manual.
- The operator’s manual must always be kept in the place provided for it on the platform and be written in the language
used by the operator.
- Any operations or manoeuvres not described in the operator’s manual must necessarily be forbidden right from the
start.
- Follow the safety advice and the instructions on the platform.
- Ypu must necessarily replace the operator’s manual, as well as any plates or stickers, if they are no longer legible or
are damaged.
- A second operator must necessaily be present on the ground as a safety measure when using the platform.
- Familiarise yourself with the platform on the terrain it has to travel over.
- The machine must also be used in accordance with good engineering practice.
- Do not use the platform if the wind speed is over 45 km/h. The platform’s arms must not be subjected to a lateral force
of more than 40 kg (platforms for indoor use must not be used outside the building).
B - AUTHORIZATION FOR USE IN FRANCE
(
or see current legislation in other countries
)
- Only qualified, authorized personnel may use the platform. This authorization is given in writing by the appropriate
person in the company, in charge of using the platform, and must be permanently carried by the operator.
- The operator is not competent to authorise the driving of the platform by another person.
WHENEVER YOU SEE THIS SYMBOL IT MEANS :
WARNING ! BE CAREFUL ! YOUR SAFETY OR THE SAFETY OF THE
PLATFORM IS AT RISK.
Summary of Contents for 160 ATJ
Page 2: ......
Page 4: ......
Page 6: ......
Page 7: ...1 1 1 OPERATING AND SAFETY INSTRUCTIONS 1 OPERATING AND SAFETY INSTRUCTIONS...
Page 8: ......
Page 25: ...1 19 REAR AXLE ASSEMBLY FIG E Axle type Serial Nr Maker s N E...
Page 28: ...1 22...
Page 29: ...2 1 2 DESCRIPTION 2 DESCRIPTION...
Page 30: ......
Page 31: ...2 3...
Page 37: ...2 9...
Page 39: ...2 11...
Page 41: ......
Page 74: ...2 46 MAIN DISTRIBUTOR Basket rotation Turret rotation Steering Pendular arm Tilt compensation...
Page 75: ...3 MAINTENANCE 3 MAINTENANCE...
Page 76: ......
Page 78: ......
Page 105: ...3 31...
Page 107: ...3 33 G3 2 Centre of gravity Platform s total weight 8090 Kg...
Page 111: ...4 ELECTRICITY 4 ELECTRICITY 4 1...
Page 112: ...4 2...
Page 114: ...4 4...
Page 115: ...5 1 5 OPTIONAL ACCESSORIES FOR THE RANGE 5 OPTIONAL ACCESSORIES FOR THE RANGE...
Page 116: ...5 2...
Page 120: ...5 6...
Page 121: ...6 1 6 MAINTENANCE HANDBOOK 6 MAINTENANCE HANDBOOK...
Page 122: ......
Page 130: ......
Page 131: ...Powered by TCPDF www tcpdf org...