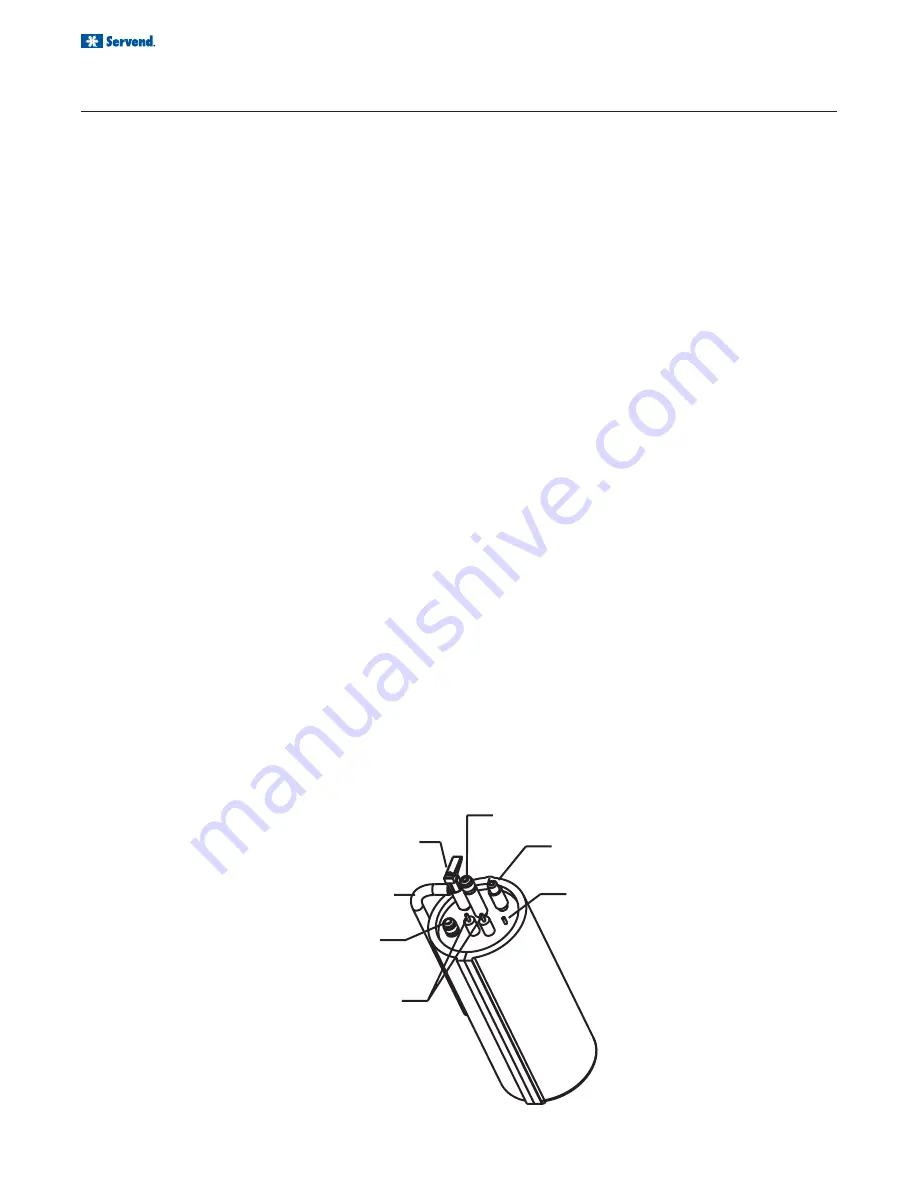
20
Installation and Service Manual
Carbonated
water Outlet
CO
2
Inlet
Water Inlet
Electronic
Probes
Ground
Pressure
Relief
Purge
Tube
OPERATION
CARBONATION
The purpose of the carbonator is to take regular tap water at street water pressure (minimum 40 PSI dynamic or
flowing pressure) 3/8” water line, and increase the water to beverage system pressure (usually 75 PSI). This water
is then combined with the CO
2
gas. Chilling the mixture before dispensing will assist in locking the carbon dioxide
into the water. After dispensing, the CO
2
may be unlocked from the liquid. The CO
2
will gradually leave the liquid
due to pressure and temperature changes.
Components
The components of the carbonator are: water pump, an
electric motor to operate the pump, carbonator tank
where the water & CO
2
mix, and a water level control.
Operation
Carbon Dioxide (CO
2
) leaves the storage tank and ar-
rives at the carbonator tank through the gas inlet. Water
supply enters the carbonator pump inlet at regular street
water line pressure (minimum 40 PSI dynamic or flow-
ing pressure). The water pump increases the pressure
of the water, which allows the water to flow into the car-
bonator tank. The CO
2
and the water mix together in the
carbonator to produce the carbonated water that is then
sent to the tank soda dispenser.
The agitation of the water & CO
2
together in the tank
under high pressure creates the carbonated water. The
quality of carbonation (percent of CO
2
mixed in the wa-
ter) increases as the water temperature decreases and
exposure time increases.
The water level in the carbonator tank is controlled by a
water level control in the tank. This control turns the pump
motor off and on to maintain a preset level of liquid in the
tank. The water level control is two conductivity probes
wired to a liquid level control board.
INTERNAL CARBONATION
The carbonator tank has two inlets and one outlet con-
nection, as well as a relief valve and two conductivity
probes. The water inlet is topped by a 3/8" male flared
fitting. The carbonator will be pre-plumbed as it leaves
the factory. If the carbonator needs to be serviced or if
the fittings need to be replaced, make sure a nylon
washer is used inside each inlet fitting to prevent leaks.
The conductivity probes are used to control the level of
water inside the carbonator tank. The red probe, or the
“high” probe, is the shorter of the two. When the level
of the water reaches the bottom of the red probe, the
pump shuts off. The pump starts when the water level
inside the tank goes below the bottom tip of the of the
black or "low" probe. Both probes are wired to the elec-
tronic liquid level control, which is a circuit board
mounted inside the electrical box that activates the
pump and motor. Removing the cover of the electrical
box will grant access to the circuit board. As the control
receives a signal from the conductivity probes, it acti-
vates the pump motor, which will pump water into the
carbonator until the water reaches the high probe.
The pump is a standard 125 GPH brass rotary vane
pump. The flared fittings accept the same swivel/barb
connectors used on the carbonator water connections.
Also, water enters the pump from the water source on
the side that has the strainer.
Summary of Contents for LP-3
Page 2: ......
Page 26: ...26 Installation and Service Manual EXPLODED VIEWS PARTS DIAGRAMS 115V WIRING DIAGRAM ...
Page 30: ...30 Installation and Service Manual EXPLODED VIEWS PARTS DIAGRAMS AUGER AGITATION DRAIN ...
Page 33: ...Installation and Service Manual 33 EXPLODED VIEWS PARTS DIAGRAMS 120V AUGER DRIVE ...
Page 36: ...36 Installation and Service Manual EXPLODED VIEWS PARTS DIAGRAMS AUGER ROCKING CHUTE ...
Page 39: ...Installation and Service Manual 39 EXPLODED VIEWS PARTS DIAGRAMS BIN ...
Page 47: ...Installation and Service Manual 47 ...
Page 48: ...48 Installation and Service Manual ...
Page 49: ...49 Installation and Service Manual ...