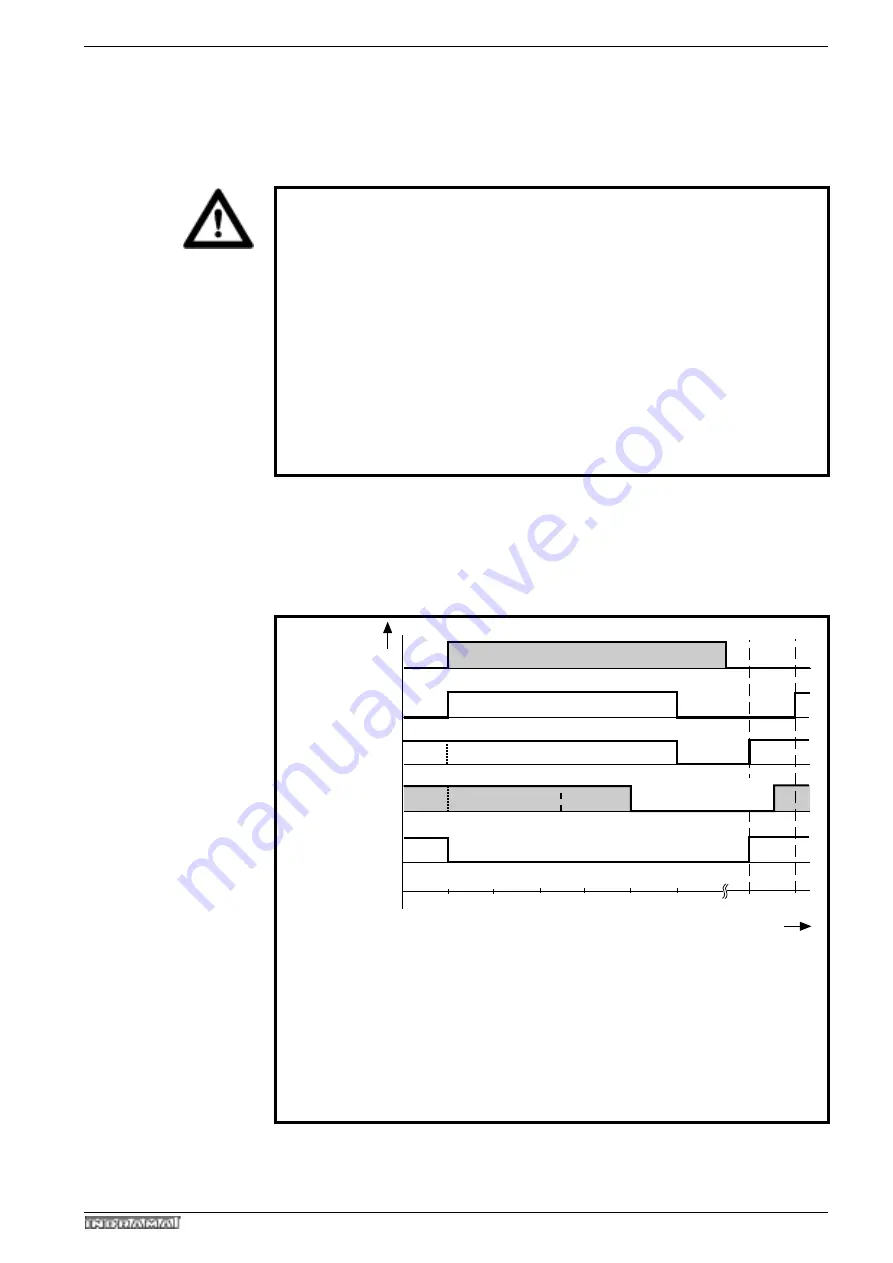
7. Commissioning
• DOK-CONTRL-DDC+MDD+DLC-ANW1-EN-E1,44 • 01.97
67
7.6.
Check Motor Holding Brake
To keep suspended axes from slumping, it is necessary to use motors with
integrated holding brakes.
Warning
Holding brake function
To release the holding brake, apply + 24V DC. The holding brake is clamped
with a power disconnect.
An INDRAMAT drive controller controls the holding brake. The set error
reaction affects the control of the holding brake.
Control of holding
brake as depends on
error reaction
Fig 7.5: Control of the holding brake depending on the error reaction
Source of danger:
The motor holding brake is not a working brake. It
wears down after 20,000 revolutions against the
closed brake.
Possible consequences:
Damage can be caused by slumping feed axes.
How to avoid:
• Use INDRAMAT drive controllers only to control
the motor holding brake.
• When projecting the machine, make sure that the
braking time of the drive does not exceed 0.4
seconds. Use a service brake for longer braking
periods.
• Do not set error reaction 2 in motors with holding
brakes.
FPDDChb
Error
Internal speed
command value
to zero
Motor torque
Holding brake
Time axis
1
0
1
0
1
0
0 100 200 300 400 500
3)
t in ms
n<10 min
-1
n>10 min
-1
1)
2)
1)
1)
The blocking brake is immediately applied is error reaction 2 is set.
The motor is immediately switched torque free.
2)
Error reaction 0 :
The blocking brake is applied when rpm falls below 10 min-1, but no later
than 400 ms
3)
The automatic program can be started 300 ms after the UC contact has closed.
4)
The UD contact opens with error reaction 1 and 2 only, if the Bb contact is
switched into the E-stop loop.
0
300
UD contact
1
0
1
0
3)
4)
released
clamped