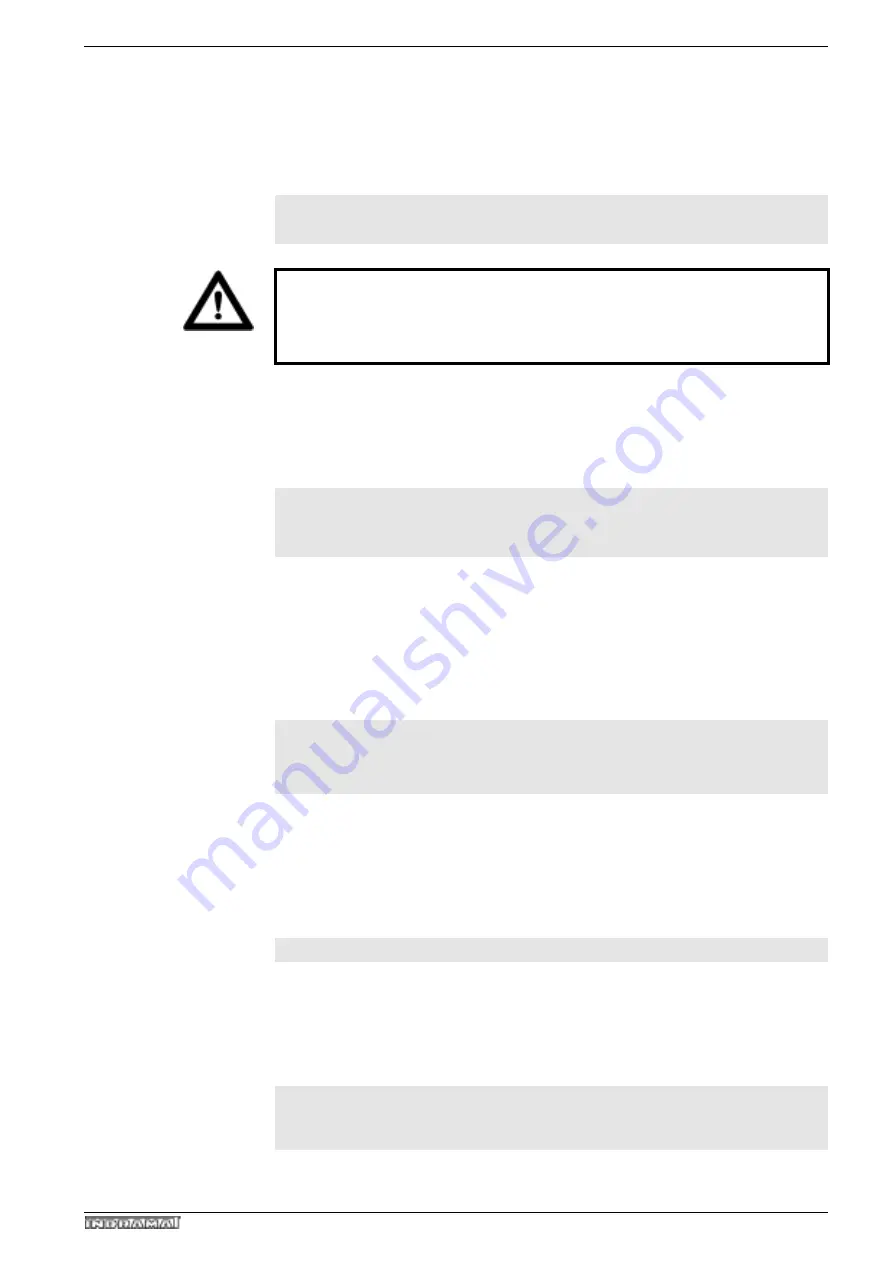
9. Diagnostics and Fault Clearance
• DOK-CONTRL-DDC+MDD+DLC-ANW1-EN-E1,44 • 01.97
93
22
Motor encoder error
There are no motor encoder signals or they are outside of the tolerance.
Remedy
1. Motor encoder cable break or incorrectly poled.
2. Motor feedback is defective.
Warning
24
Overcurrent
One of the three phase currents has reached a level that is greater than 1.5
times the rated current of the unit.
Remedy
25
Overvoltage
The DC bus voltage has reached an unacceptably high level (UD > 475V).
So as not to endanger the power stage of the drive controller, the drive was
switched torque-free.
Remedy
1. Peak regenerative power too high
2. Bleeder switch defective
26
Undervoltage error
The DC bus voltage is monitored in the drive controller. If it should exceed a
threshold of + 200 V then the drive will be brought to a standstill as per the
error reaction set.
Remedy
Fault in the power source (Phase failure)
33
External voltage supply fault
Auxiliary plug-in module (e.g., DEA 4) with galvanically isolated inputs and
outputs must be supplied with 24 V DC.
Remedy
The external 24 V DC are lacking or outside of the tolerance.
1. Check motor encoder cable.
2. Replace motor (feedback defective)
Source of danger:
Displacement of dimensions if motor replaced!
Possible consequences:
Risk of damage to machine and workpiece.
How to avoid:
Check reference dimension after motor is replaced.
1. Check motor cable.
2. Check current regulator parametrization. Contact INDRAMAT Customer
Service in this case.
1. Use a drive controller with higher peak bleeder output.
2. Check application.
3. Replace drive controller.
1. Clear the fault in the power supply.
1. Check external voltage source. Voltage width and tolerances are listed
in the Project Planning Manual. See plug-in module for digital intelligent
drive controllers, Project Planning Manual, doc. no. 209-0069-4356-XX.