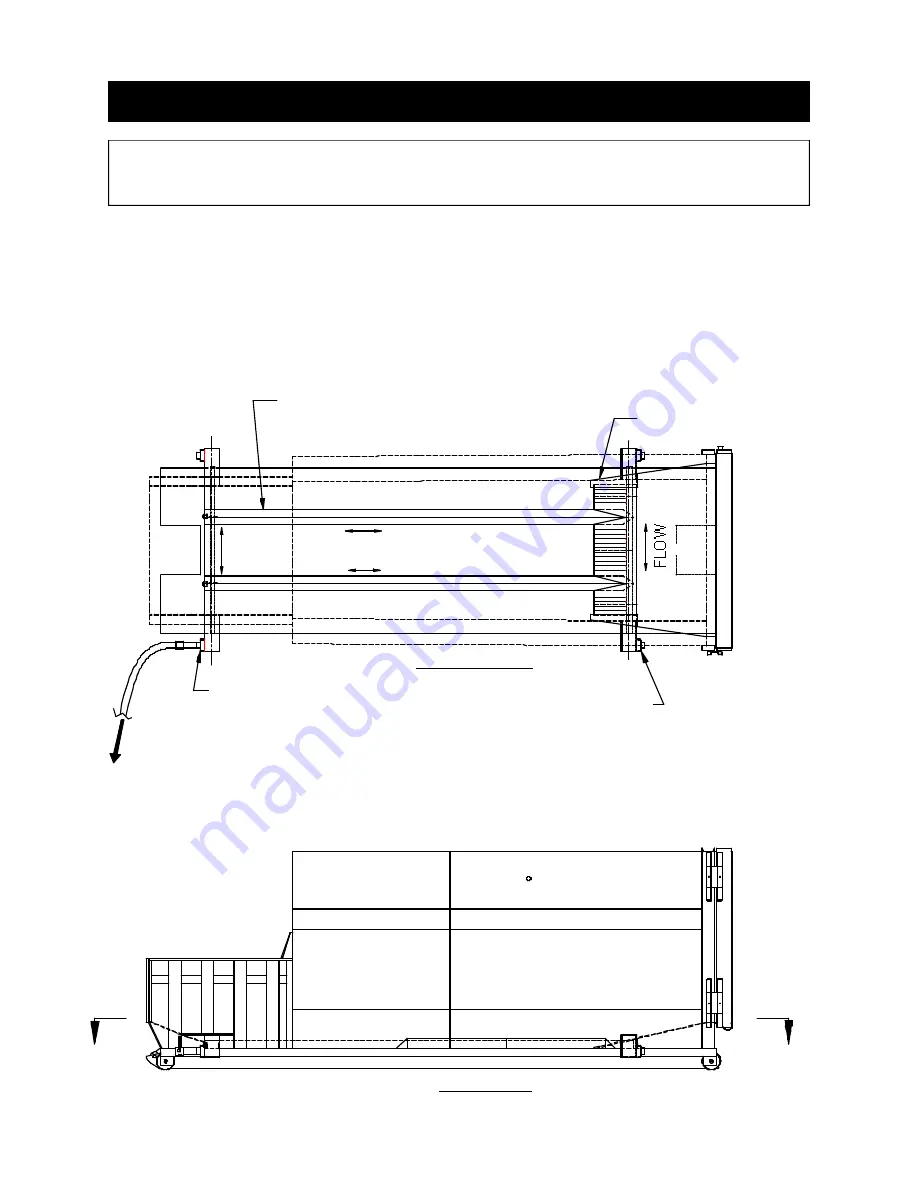
4 HAULER INFORMATION
HAULER INSTRUCTIONS - LIQUID REMOVAL
(FOR OPTIONAL SL UNITS) 4-5
The Ram Jet Self-Contained Streamline compactor/containers are designed with an
internal drain system for liquid removal, ported to each corner of the machine. The unit
comes standard with one ball valve. This valve can be moved to any of the four drain
outlets on the machine. The valve should be located at the lowest outlet on the machine
for proper drainage. The customer can attach a drain hose with a 3” NPT male fitting to
the drain valve.
5” ANGLES PROVIDE PATH FOR LIQUID
REMOVAL
REAR DRAIN GRATING
DIRECTS LIQUID OUT
TO DRAINS
FLOW
FLOW
FLOW
A
A
SECTION A-A
DRAIN HOSE TO PUMP
OR DRAIN SUMP.
(CUSTOMER SUPPLIED)
TYPICAL DRAIN VALVE LOCATION
AT LOW CORNER OF MACHINE.
(3” NPT FEMALE THREAD)
4” DRAIN OUTLET
AT EACH CORNER.
SIDE VIEW