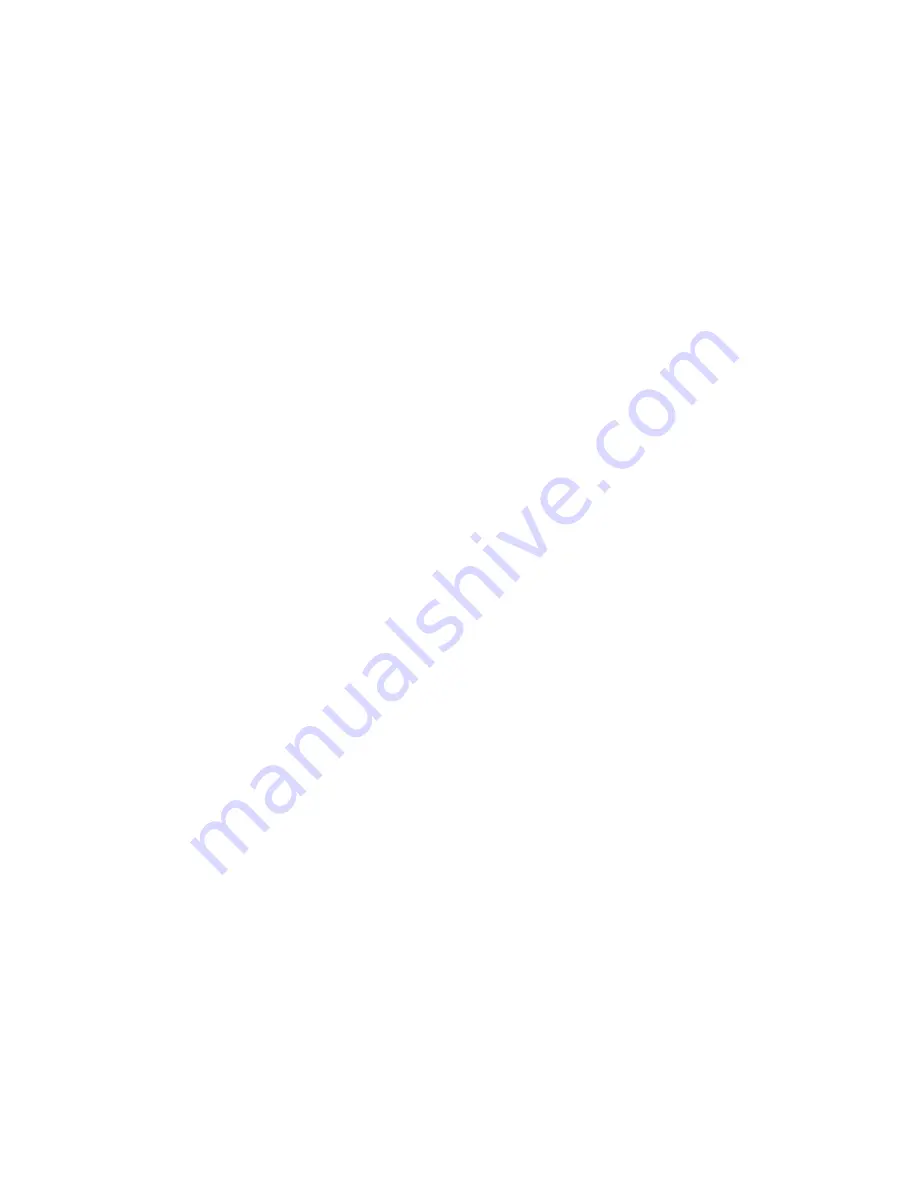
THERMOSTATS
ACC Models. Two accessory options are available:
• The hand-held IRRC Model 300 non-programmable remote thermostat.
• The wall-mounted programmable thermostat.
Instructions for installing both options are supplied with them.
RMT Models. These have an IRRC Model 400 programmable hand-held remote control (not interchangeable with
the Model 300 control available for the ACC models). The RMT system uses a mains powered 24 volt supply to
operate the control box which is factory mounted on the rear of the pedestal. The receiver for the signal from the
remote control is mounted on the front corner of the pedestal foot. Connect the cable from the receiver unit to
the matching plug on the short cable on the control box. Fit the plug on the transformer outlet cable into the
socket on the control box and plug the transformer into a suitable 230v mains outlet. The three-position switch
on the control box must be set to ‘REMOTE’ before the heater will operate automatically. See page 5
(RECEIVER SWITCH POSITIONS) for details of the various functions provided by the three-position switch.
ECS Models. An optional battery powered wall-mounted programmable thermostat is available.
GAS PRESSURE ADJUSTMENT.
All pressure adjustments (except the low pressure on the RMT
model) must be made while the heater is operating on the ‘HIGH’ setting.
STD NG. This has a pressure regulator separate from its control valve. The regulator must be set to 1.0 kPa. The
pressure test point is on the side of the regulator and the adjusting screw is on the top. Slacken the lock-nut and
rotate the screw by hand, screwing down to increase the pressure. Tighten the lock nut after adjusting. This
should result in a valve outlet pressure of 0.72 kPa.
STD LP. This model has no internal pressure regulator as it runs directly on the 2.71 kPa pressure delivered by the
gas bottle regulator.
ACC NG and ACC LP. These also have a pressure regulator inside the control valve. There are two test points
side by side on top of the control valve – the outlet pressure test point is the one closer to the flame size control
knob. If adjustment is necessary, uncouple the control rod from the top of the flame size control knob, extract
the screw from down the centre of this knob and pull the knob off vertically. The pressure is then set by rotating
the knurled plastic wheel exposed by removing the knob. Once the pressure is correct (0.95 kPa for NG or 2.5
kPa for LP), care must be taken not to turn the plastic wheel as the knob is re-fitted in its maximum anti-
clockwise position. This position is set when the skirt of the knob contacting the adjacent metal up-stand. Rotate
the knob clockwise and then fully anti-clockwise while observing the pressure to verify that it is correct before
replacing the retaining screw and re-coupling the control rod.
RMT NG and RMT LP. Again, these have a pressure regulator inside the control valve. The outlet pressure test
point is on the top of the control valve and is furthest from the gas inlet connection. There are two pressure
settings to adjust, high and low. Access to the adjusters is gained by removing the protective transparent cap at
the very top of the control valve. This will expose the red central screw (low pressure adjuster) and a 10mm
hexagonal nut surrounding it (high pressure adjuster).
Set the high pressure first. With the heater running on ‘HIGH’, make the adjustment by rotating the 10mm nut,
screwing down to increase the pressure. Correct pressures are 1.0 kPa for NG and 2.71 kPa for LP. To set the
low pressure, move the switch on the receiver control box to ‘ON’ so that the flame is burning on ‘LOW’. Set
the low pressure by rotating the red Phillips head screw downwards to increase the pressure, taking great care
not to disturb the setting of the outer 10mm nut. The correct low pressures are 0.3 kPa for NG and 1.0 kPa for
LP.
Replace the protective cap on top of the adjusters and set the three-position switch to ‘REMOTE’.
ECS NG and ECS LP. These also have a pressure regulator in the control valve. The outlet pressure test point is
on the top of the control valve and is the one remote from the gas inlet connection. There are two pressure
settings to adjust, high and low. Access to the adjusters is gained by first removing the heat shield above the
valve and then removing the protective transparent cap at the very top of the control valve modulating coil. This
will expose the central screw (low pressure adjuster) and a 10mm hexagonal nut surrounding it (high pressure
adjuster). Note that the modulating coil may be rotated through 90° if necessary to provide easier access for
pressure adjustments. Before adjusting the high pressure, the fire must be alight and burning at the ‘HIGH’
setting. (Hold down the + end of the top rocker switch on the handpiece for 30 seconds to ensure this).
Set the high pressure first. NG high pressure should be 0.95 kPa and LP high pressure should be 2.3 kPa.
Adjust, if necessary, by rotating the 10mm nut, screwing down to increase the pressure and up to decrease it.
8