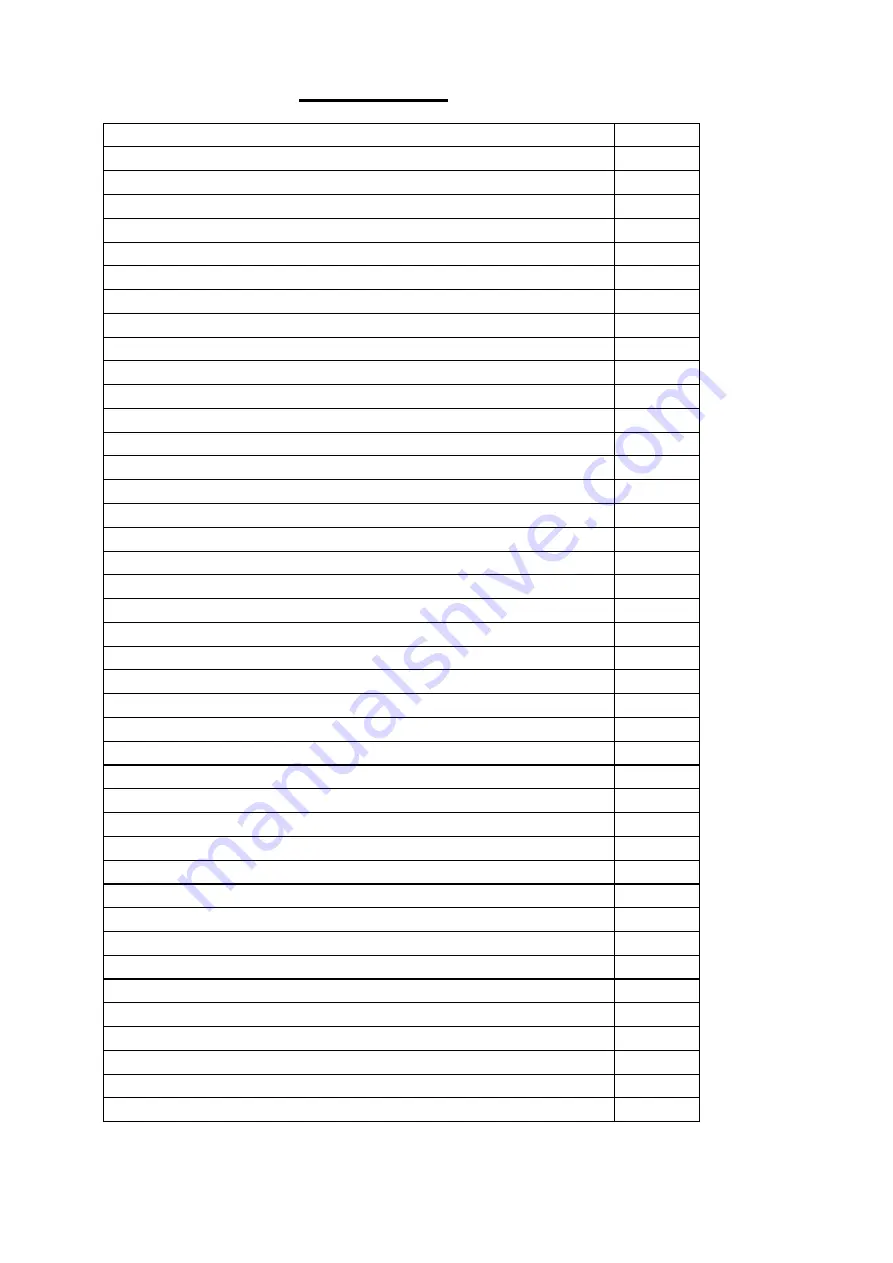
2
CONTENTS
PAGE
1.0 INTRODUCTION
3
1.1 ITEMS SUPPLIED WITH THE FIRE
3
1.2 HANDLING AND TRANSPORT
3
1.3 WARNINGS
4
1.4 CAUTIONS
4
2.0 TECHNICAL SPECIFICATIONS
5
3.0 INSTALLATION OF THE WAIMAKARIRI ULEB
6
3.1 UNPACKING
6
3.2 POSITIONING
6
3.3 FLUE REQUIREMENTS
6
3.4 FLOOR PROTECTOR REQUIREMENTS
7
3.5 REDUCING CLEARANCES
7
3.6 SEISMIC RESTRAINT
8
3.7 PREPARING THE BURNER FOR FIRST LIGHT-UP
9
4.0 PERMITTED FUELS
13
4.1 TESTING YOUR WOOD MOISTURE
13
4.2 RECOMMENDED FUEL LOG SIZES
13
5.0 OPERATIONAL SEQUENCE
14
5.1 BEFORE FIRST LIGHT-UP
14
5.2 COLD START-UP
14
5.2.1 KI INTERMEDIATE LOAD 1
14
5.2.2 INTERMEDIATE LOAD 2
14
5.2.3 MAIN LOAD
15
5.2.4 RE-FUELING & SHUT-DOWN
15
6.0 CATALYTIC COMBUSTOR & MAINTENANCE
16
6.1 HOW IT WORKS
16
6.2 BEST PRACTICES TO ENHANCE LIFE OF COMBUSTOR
16
6.3 INSPECTING CATALYTIC COMBUSTOR
17
6.4 REMOVAL OF CATALYTIC COMBUSTOR
17
6.5 CLEANING OF CATALYTIC COMBUSTOR
17
6.6 WHEN TO REPLACE CATALYTIC COMBUSTOR
18
6.7 DIFFERENT STATES OF CATALYTIC COMBUSTOR
19
6.8 MAINTENANCE OF OTHER WAIMAKARIRI PARTS
20
7.0 WAIMAKARIRI REPLACEMENT PARTS
21
8.0 TROUBLESHOOTING: CAUSES & REMEDY
22
WAIMAKARIRI WARRANTY REGISTRATION
25
WAIMAKARIRI WARRANTY TERMS & CONDITIONS
27