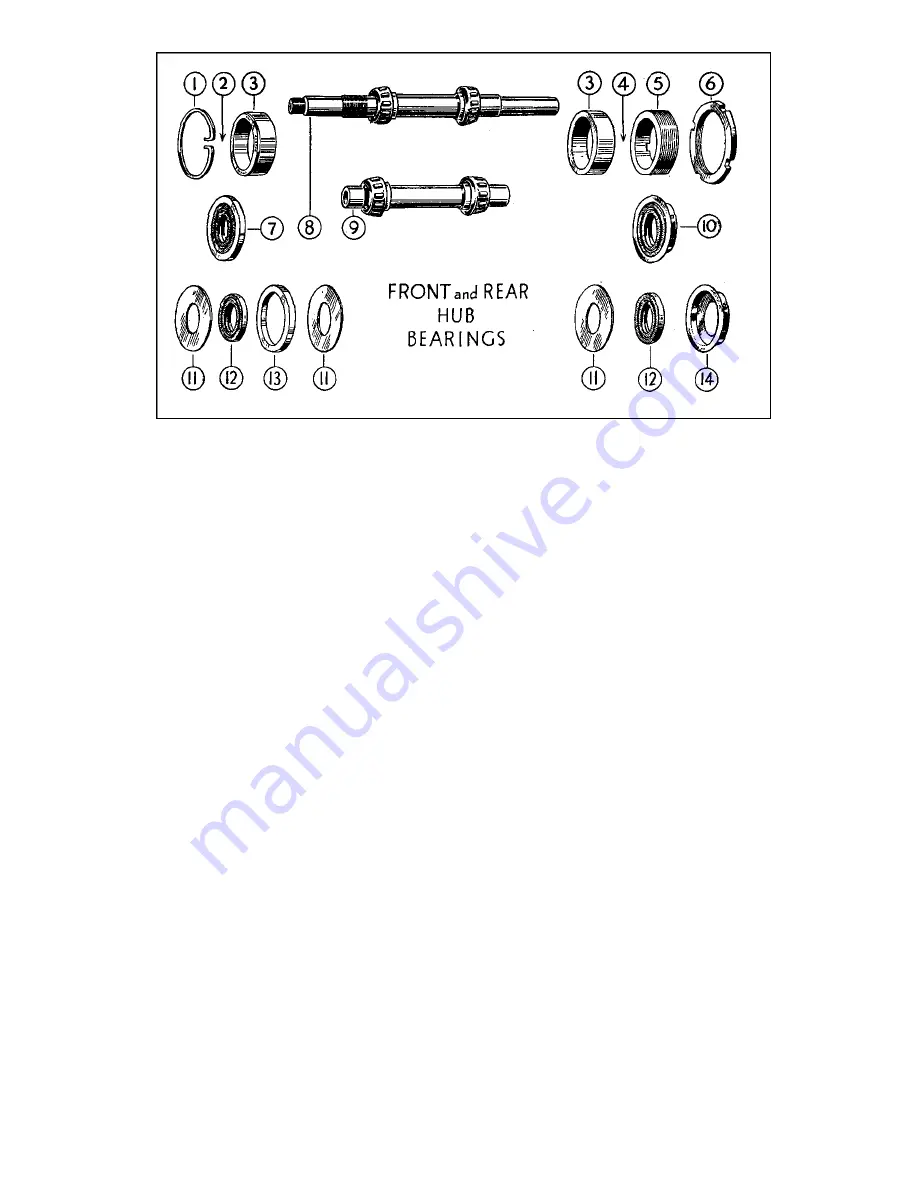
Illustration
22
Showing exploded view of hub bearing components.
1
2
3
4
5
6
7
SPRING CIRCLIP, (FITS IN GROOVE CUT
IN UNTHREADED END OF HUB.
OIL SEAL ASSEMBLY, CONSISTING OF :
1 SPACING RING (11)
1 OIL SEAL
(12)
1 COLLAR
(13)
1 SPACING RING (11)
FITS HERE, BETWEEN THE BEARING CUP
(3) AND THE SPRING CIRCLIP (1).
OUTER CUP OF TAPER ROLLER BEARING.
(*).
OIL SEAL ASSEMBLY, CONSISTING OF :
1 SPACING RING (11)
1 OIL SEAL
(12)
1 DISHED CUP (14)
FITS HERE, BETWEEN THE BEARING CUP
(3) AND THE BEARING ADJUSTING
RING (5).
ADJUSTING RING, FOR BEARINGS.
LOCK NUT, FOR BEARING ADJUSTING
RING.
AN OIL SEAL (12) ENCIRCLED WITH ITS
SPACING COLLAR (13).
8
9
10
11
12
13
14
*
FRONT WHEEL SPINDLE, WITH SET OF
TAPER ROLLERS MOUNTED IN TWO
CAGES.
REAR WHEEL HOLLOW SPINDLE WITH
SET OF TAPER ROLLERS MOUNTED IN
TWO CAGES.
AN OIL SEAL (12) SHOWN PRESSED INTO
A DISHED CUP (14).
RETAINING SPACING RING, OR WASHER,
FOR OIL SEAL.
OIL SEAL.
SPACING COLLAR, (THIS ENCIRCLES
THE OIL SEAL FITTED TO THE UN-
THREADED END OF A HUB.)
DISHED CUP, (THIS CONTAINS THE OIL
SEAL FITTED TO THE THREADED END OF
A HUB.
These are not supplied separately. A
front, or rear wheel spindle complete
with taper roller bearings includes two
of these bearing cups.
Also rollers are not supplied separately.
61
Summary of Contents for 46/G3L 1946
Page 2: ......
Page 54: ...Illustration 19 52 ...
Page 89: ...Illustration 36 Wiring Diagram Pictorial 87 ...
Page 91: ......
Page 92: ......