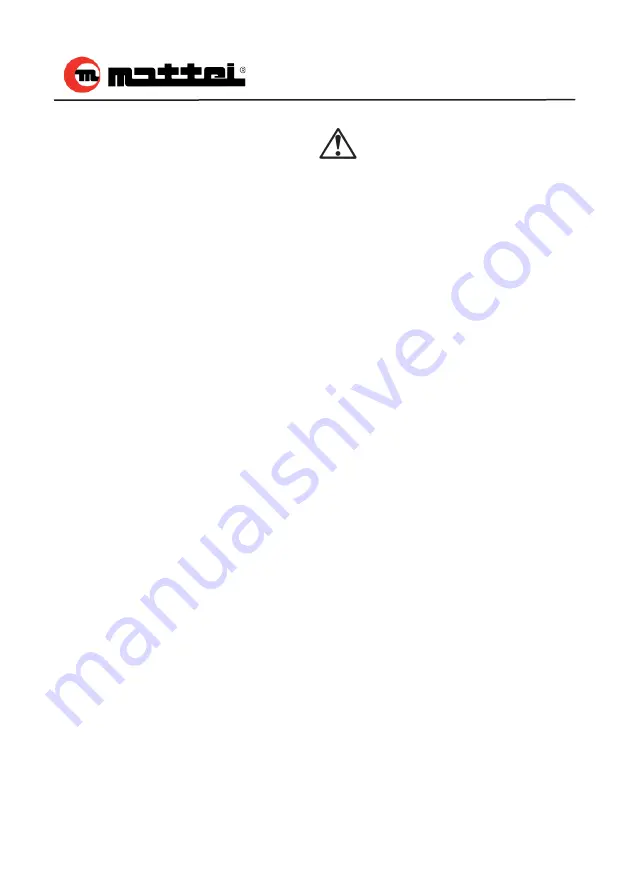
8.01
TI013G0008
Lubricants
Synthetic oils
Many synthetic oils with different bases are
available on the market (esters, glycols,
etc) that sometimes have proved to be sui-
table and provide a longer life than mineral
oils.
Normally they reduce carbon deposits, pro-
vide a high self-ignition temperature and
are remarkably resistant to oxidation.
As synthetic lubricants are good detergents,
to change the kind of lubricant in a machi-
ne and pass from a conventional mineral
based to a synthetic one, it is necessary to
carry out a thorough washing, following the
supplier’s instructions, to avoid damages to
the machine if dirt, residues and deposits
circulate.
It is also necessary to pay attention to con-
densate, as usually synthetic lubricants are
more sensitive to water washing and their
thin
fi
lm may not provide enough protection
against rust.
This problem can be worsened if the com-
pressor is not working continuously, but oc-
casionally.
In this case, even though not suggesting its
use, any responsibility for the choice is up
to the user and to the lubricant supplier.
WARNING!!!
It is diffi cult to determine life
of an oil, as there are different
parameters effecting the same, among
which the operating temperature and
quality of the intake air are very impor-
tant.
For this reason it is recommended to
obtain precise guarantees from the sup-
plier, validated by the analysis of sam-
ples taken from the machine, to determi-
ne the suitability of lubricant and its life.
MATTEI LUBRICANTS
Considering the important role of lubricant
for operation of the compressor, Mattei of-
fers special lubricants to the users and re-
commends their use.
These are:
- Mattei Rotoroil F2 (synthetic),
- Mattei Rotoroil F4 (synthetic),
- Mattei Rotoroil FG (synthetic, non toxic)
- Mattei Rotoroil M1 (mineral oil)
available in available in 1, 5 and 55 gallon
containers.
Their life can reach the hours shown in the
table, depending on the operating tempera-
ture and conditions of the intake air.
MATTEI LUBRICANTS
Name
Ambient temperature
Operating hours (max.)
Rotoroil F2
from 5 to 113 °F
5000
Rotoroil F4
from -22 to 86 °F
5000
Rotoroil FG
from 23 to 104 °F
1000
Rotoroil M1
from 25 to 113 °F
2000