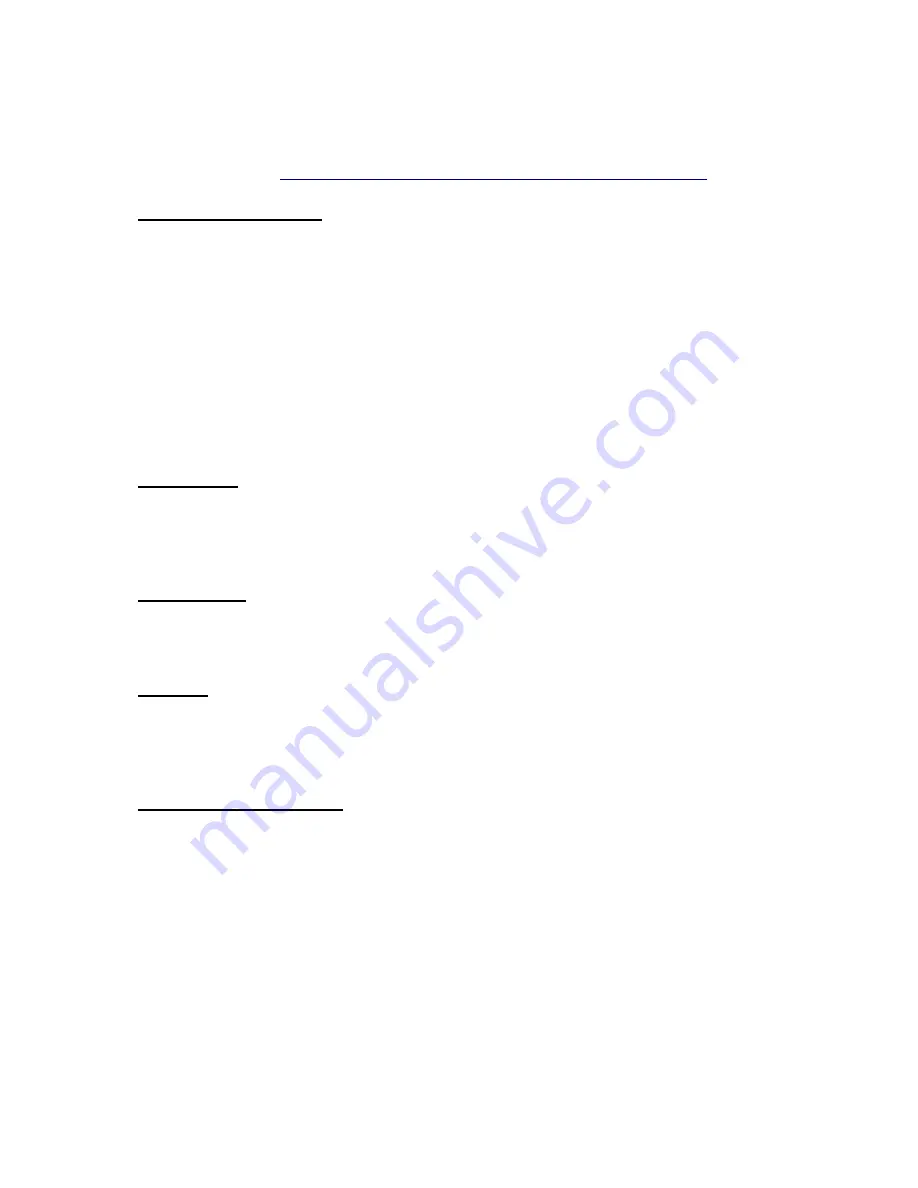
MAULE AEROSPACE TECHNOLOGY, INC.
MAINTENANCE MANUAL
FOR
MT-7-260
Rev. D
22/36
MOVABLE SURFACES AND CONTROL
AILERONS AND FLAPS
:
The ailerons and flaps are aluminum alloy structures covered with 2024-T3.
The aileron control system consists of a chain drive connecting the two control wheels and
is attached to the necessary cables which are routed over pulleys through the fuselage and into
the wing section to the aileron horns.
The flap control system consists of a control lever which has five active positions,
(-7
, 0
,
24
and 40
).
This is connected to the control cables (and spring cartridge located directly behind
cargo area) which are routed over pulleys through fuselage and connected to chain drive located
directly above the cabin area. This chain drive is connected to a torque tube which operates the
flap through a push-pull rod attached to the inboard hinge fittings.
ELEVATORS
:
The elevator has chrome molybdenum (4130) internal structure covered with Ceconite fab-
ric. Inspect for corrosion. Drain grommets should be kept open. The hinge attachments should
be lubricated with light engine oil. Accumulations of dust and dirt on hinges should be removed.
STABILIZERS
:
The stabilizers have chrome molybdenum steel (4130) internal structures covered with Ce-
conite fabric.
Inspect for corrosion including elevator hinges and struts.
RUDDER
:
The rudder structure is very similar to the elevators. No maintenance other than inspection
for corrosion is needed. The hinges should be cleaned and lubricated with light engine oil at fre-
quent intervals. The cable attachment points should be checked for wear and corrosion.
TRIM AND RUDDER TABS
:
These surfaces have low carbon steel frames with aluminum alloy skin (2024-T3).
These surfaces need no maintenance other than inspection for corrosion. The hinges
should be lubricated at frequent intervals using light engine oil.