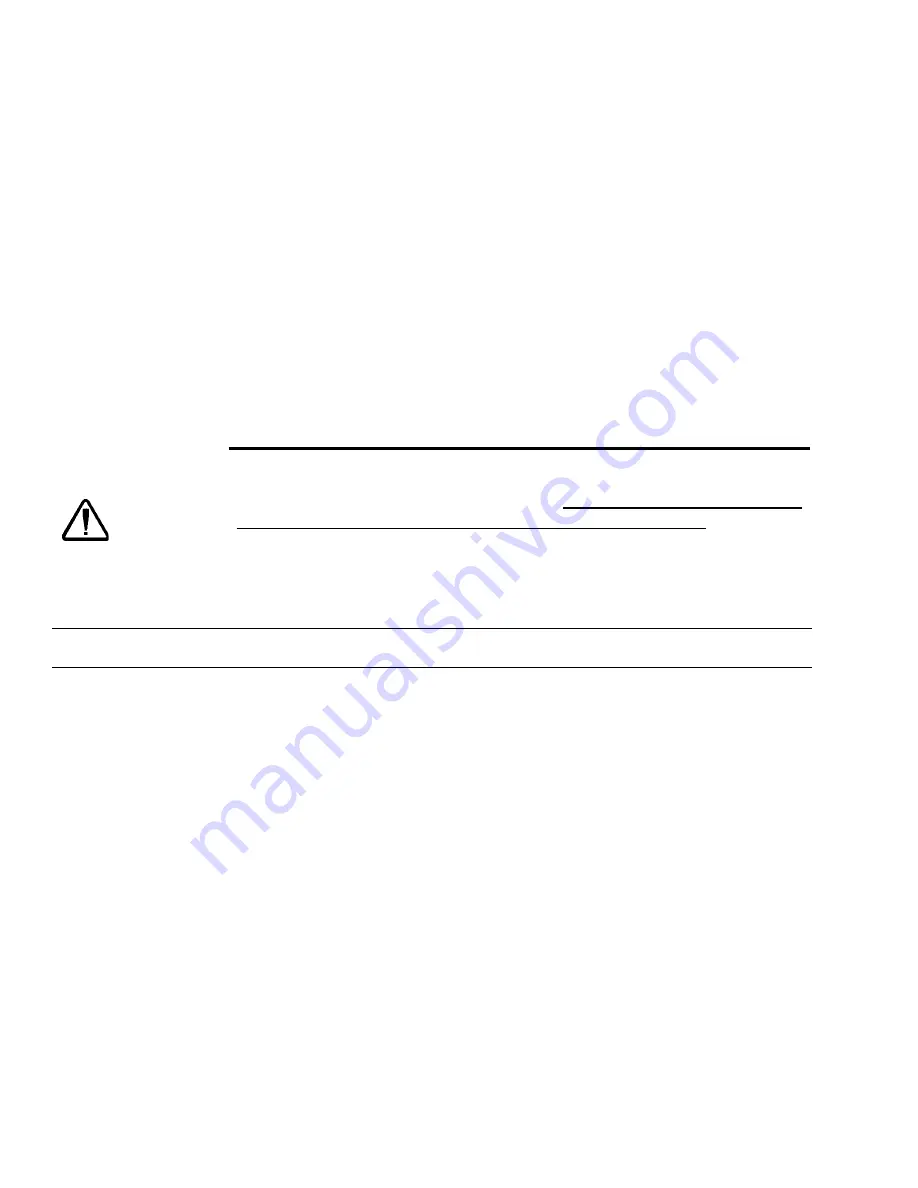
Section 4 – Operation/Configuration/Calibration
Rev. 2.0 04/16
22
H6630EM-LIT
Actuator Software Limit Setting (range of travel)
Software limits are set on the maintenance screen and limit the movement of the actuator to prevent
damage at the ends of travel. Care must be taken to not run the actuator into the ends of travel. The
positive and negative software limits must be set to eliminate this. After logging in with the password,
verify the positive software limit and the negative software limit are set to the amount of actuator travel.
If not, enter the correct values and press accept SW limit button. The range may be set less as desired
by the customer or dictated by the actual amount of stroke or limitation of the guide.
It is
recommended to set the limits less than the actuator stroke to ensure the ends of stroke are not
hit.
Also ranges may be offset as needed for the specific installation. Example: for a 12” stroke
actuator, positive limit could be set to 4.00” and negative limit set -5.50”.
At this time, the jog functions can be retested and software limits verified. Jog pushbuttons are located
on the Control screen and Maintenance screen of the local HMI. Utilize the jog pushbuttons to slowly
reach the end position and verify the actuator stops at the limit prior to reaching the end of travel.
The “Manual Direction” pushbutton on the maintenance screen will allow selection of the direction the
Jog pushbuttons move the actuator when pressed.
CAUTION
Repeated driving into the stops may cause actuator damage and/or controller trip
on overcurrent. Utilize the jog functions to test that the unit is stopping due to the
SW limits, otherwise re-perform this section. Ensure the Accept software limits
pushbutton is depressed after making any changes to the SW limits. The SW limit
may be reduced as needed to ensure the end of stroke is not reached. If the
controller trips during set up due to overcurrent etc., depress the reset button on
the maintenance screen to clear the trip
.
Note:
Motor Manual RPM can also be reduced from the maintenance screen to provide slower movement if
needed.
Roll Center or Park Position
The “Park” pushbutton provides a means to send the actuator to a preset position of the travel.
This is usually the position that the guide is centered. On the maintenance screen, enter the
desired “Park” position in inches. Jog the guide off center and test by using the “Park”
pushbutton on the Main screen. Speed for this function may be set on the maintenance
screen by using the Park RPM setting.
Detector Zero
By placing a sample of the process material in the detector, or with the line threaded through
the detector, the voltage output of the sensor can be read on the maintenance screen. If using
a flag or sample, ensure the material is grounded as required for capacitance style detectors.
Once the strip is placed at the desired position to be guided to, the “Detector Zero” button can
be pressed to capture the desired control point.
Summary of Contents for H6630EM
Page 2: ......
Page 8: ...Table of Contents Rev 2 0 04 16 iv H6630EM LIT ...
Page 16: ...Section 2 Installation Rev 2 0 04 16 8 H6630EM LIT ...
Page 28: ...Section 3 HMI Human Machine Interface Displays Rev 2 0 04 16 20 H6630EM LIT ...
Page 32: ...Section 4 Operation Configuration Calibration Rev 2 0 04 16 24 H6630EM LIT ...
Page 42: ...Section 6 Repair Replacement Rev 2 0 04 16 34 H6630EM LIT ...
Page 47: ...Appendix A H6630EM LIT 39 Rev 1 0 11 14 Downloading Programs Drive Program IS1293 ...
Page 48: ...Appendix A Rev 2 0 04 16 40 H6630EM LIT ...
Page 49: ...Appendix A H6630EM LIT 41 Rev 1 0 11 14 ...
Page 50: ...Appendix A Rev 2 0 04 16 42 H6630EM LIT ...
Page 51: ...Appendix A H6630EM LIT 43 Rev 1 0 11 14 ...
Page 52: ...Appendix A Rev 2 0 04 16 44 H6630EM LIT ...
Page 53: ...Appendix A H6630EM LIT 45 Rev 1 0 11 14 ...
Page 54: ...Appendix A Rev 2 0 04 16 46 H6630EM LIT ...
Page 55: ...Appendix A H6630EM LIT 47 Rev 1 0 11 14 HMI Program IS1287 ...
Page 56: ...Appendix A Rev 2 0 04 16 48 H6630EM LIT ...
Page 58: ...Appendix A Rev 2 0 04 16 50 H6630EM LIT ...
Page 60: ...Appendix B Rev 2 0 04 16 52 H6630EM LIT H25 4674 H6630 Advanced Parameters Trip Indications ...
Page 61: ...Appendix B H6630EM LIT 53 Rev 1 0 11 14 ...
Page 62: ...Appendix B Rev 2 0 04 16 54 H6630EM LIT ...
Page 63: ...Appendix B H6630EM LIT 55 Rev 1 0 11 14 ...
Page 64: ...Appendix B Rev 2 0 04 16 56 H6630EM LIT ...
Page 65: ...Appendix B H6630EM LIT 57 Rev 1 0 11 14 ...
Page 66: ...Appendix B Rev 2 0 04 16 58 H6630EM LIT ...
Page 67: ...Appendix B H6630EM LIT 59 Rev 1 0 11 14 ...
Page 68: ...Appendix B Rev 2 0 04 16 60 H6630EM LIT ...
Page 69: ...Appendix B H6630EM LIT 61 Rev 1 0 11 14 ...
Page 70: ...Appendix B Rev 2 0 04 16 62 H6630EM LIT ...
Page 72: ......
Page 73: ......