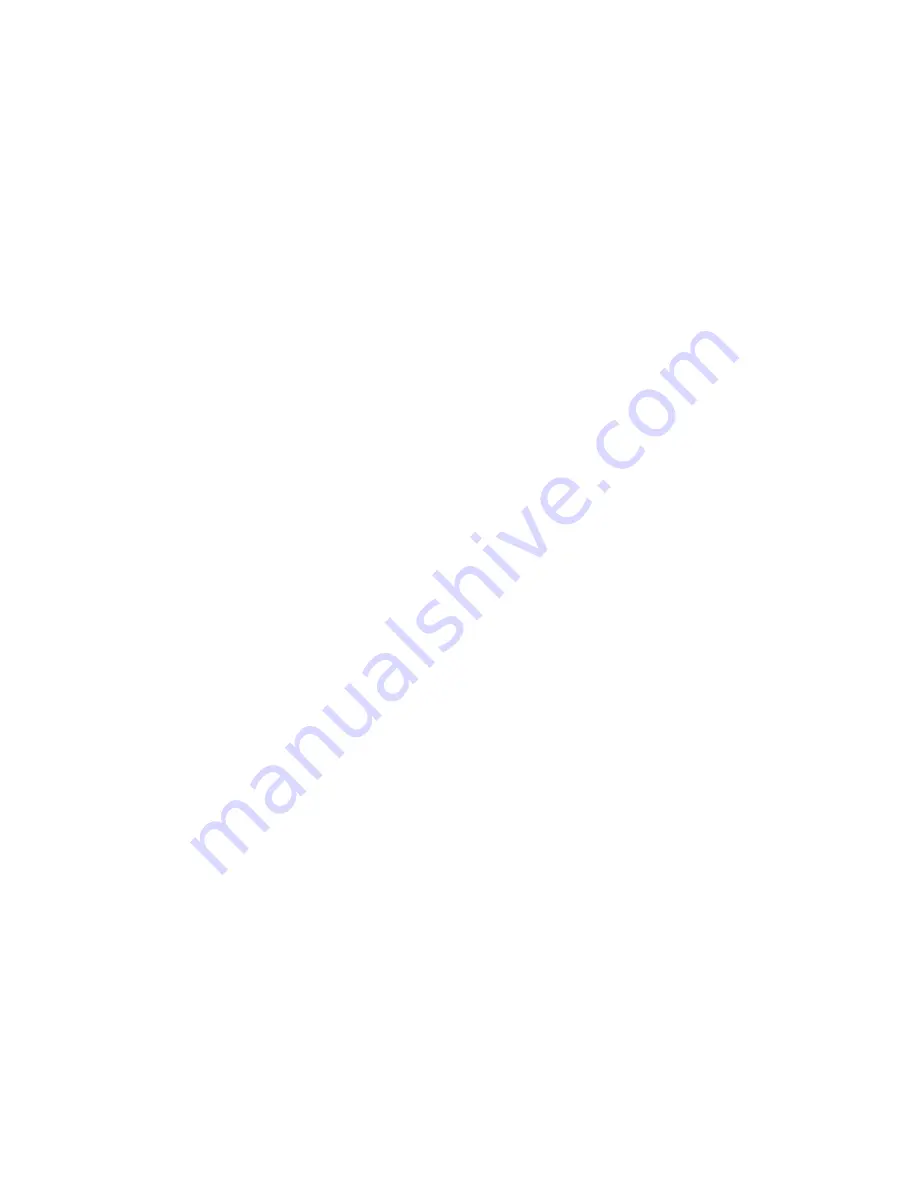
4
3 Safety instructions
MAXIMATOR compressors are manufactured to the latest state of the art and are
safe to operate. However, there are potential hazards in case of inadvertent wrong
operation or wrong use:
•
For the health and lives of persons.
•
For the compressor and its accessory parts as well as other assets.
•
For the life cycle and the performance capacity of the compressors and its
accessory parts.
Operation, maintenance and assembly of the compressor may only be carried by
personnel who are familiar with working on pneumatic systems and are familiar with
the hazards entailed by such systems. In addition, the operating instructions shall be
thoroughly studied and adhered to.
3.1 Usage to the intended purpose
The compressors may be exclusively used with those media for which they are
suitable according to our media endurance schedule. Any other media have to be
tested by us for compatibility with the compressor materials prior to being used. The
compressor drives are designed for compressed air up to 10 bar, other gases have to
be tested by us for compatibility with the compressor materials prior to being used.
Changes and modifications of the compressors are prohibited for safety reasons.
All maintenance, assembly and operating instructions specified in these operating
instructions must be adhered to in order to guarantee full functioning and safety.
3.2 Emission
Expanding compressed air is, depending on the specific application, prone to
generate a certain level of noise. Moreover, exhausting air from the silencer may be
fouled with water and oil (grease). It is also possible that small ice crystals form at the
silencer, become loose and fly around. This is why persons have to wear goggles
and, if need be, ear protection while in the vicinity of running compressors.
3.3 Safety hazards
During operation of the unit, both the drive part and the high-pressure part are under
pressure. Hence, it should be borne in mind that any gas that may leak due to a
defect or also during normal operation are highly pressurised and must not be
contained or deviated by objects or body parts. It must be ensured that in case of a
defect a compressor is immediately depressurised and repaired.
Maintenance and repair work may only be carried out at depressurised units.
Summary of Contents for DLE 5
Page 6: ...6 ...