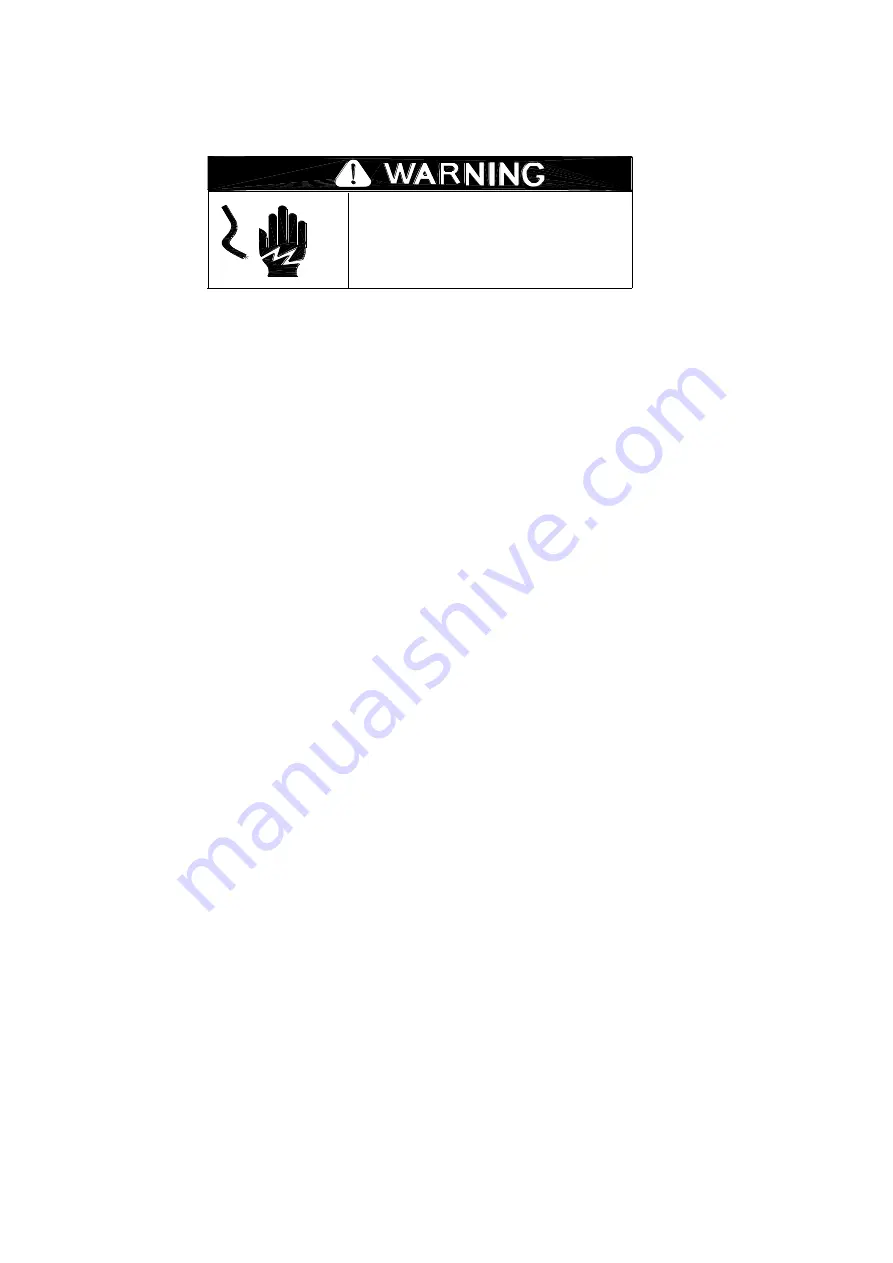
15
Troubleshooting
Before Maintenance
1.
Be sure the electrical supply is 115 VAC, 60Hz, 15A and is properly grounded to protect
maintenance personnel against electrical shock.
2.
Are any electrical leads loose? Danger of short circuit? If so, disconnect power.
Basic Troubleshooting
Some problems can be pinpointed through the service technician’s senses of hearing, sight and
touch. Examples are listed below.
Listen
Listen to the user’s description of how the ice maker was operating, especially the depiction of
unusual phenomena. Ask how the unit was operating before the user called for service and try to
deduce the defect from the comments.
Does the machine sound normal when it is running (like a window air conditioner)?
Look
Check the cooling system tubing, especially the welded joints. If some oil can be seen, the gas
may be leaking resulting in less than the normal amount of ice is being produced.
Is the cycle of the icemaking and ice harvesting normal (Does water run, is the fan running and
is the evaporator getting cold enough)?
Check the water system especially at the connections. Are there any water leaks?
Check the flow of water through the water filter and if not, replace the water filter.
Check if the ice maker was installed according to the user’s manual (level and air space).
Inspect the ice maker to see if it needs to be cleaned. Please note, cleaning a dirty ice maker is
not a warranty repair!
Feel
Touch the tubing at the evaporation weld, feeling the temperature. During the icemaking stage,
it should feel cold. During the ice harvest stage, it should feel hot.
If appropriate, touch the capillary tube or TXV tubing (near the drier). It should feel warm
during the ice making stage.
Troubleshooting Guide
This troubleshooting guide in the user manual should be read before this guide. Be sure only when
the trouble shooting in user manual can’t help you solve the problem, turn to this guide.
Troubleshooting Guide
ELECTRICAL SHOCK HAZARD
Disconnect Electrical Power Before
Beginning Removal of Parts
Summary of Contents for MIM1000
Page 1: ...1 Automatic Ice maker Service manual MIM452 MIM600 MIM1000...
Page 5: ...5 Cooling System...
Page 9: ...9 Wiring Connection...
Page 12: ...12 Exploding Drawing...
Page 16: ...16...
Page 17: ...17...
Page 18: ...18...
Page 19: ...19...
Page 20: ...20...