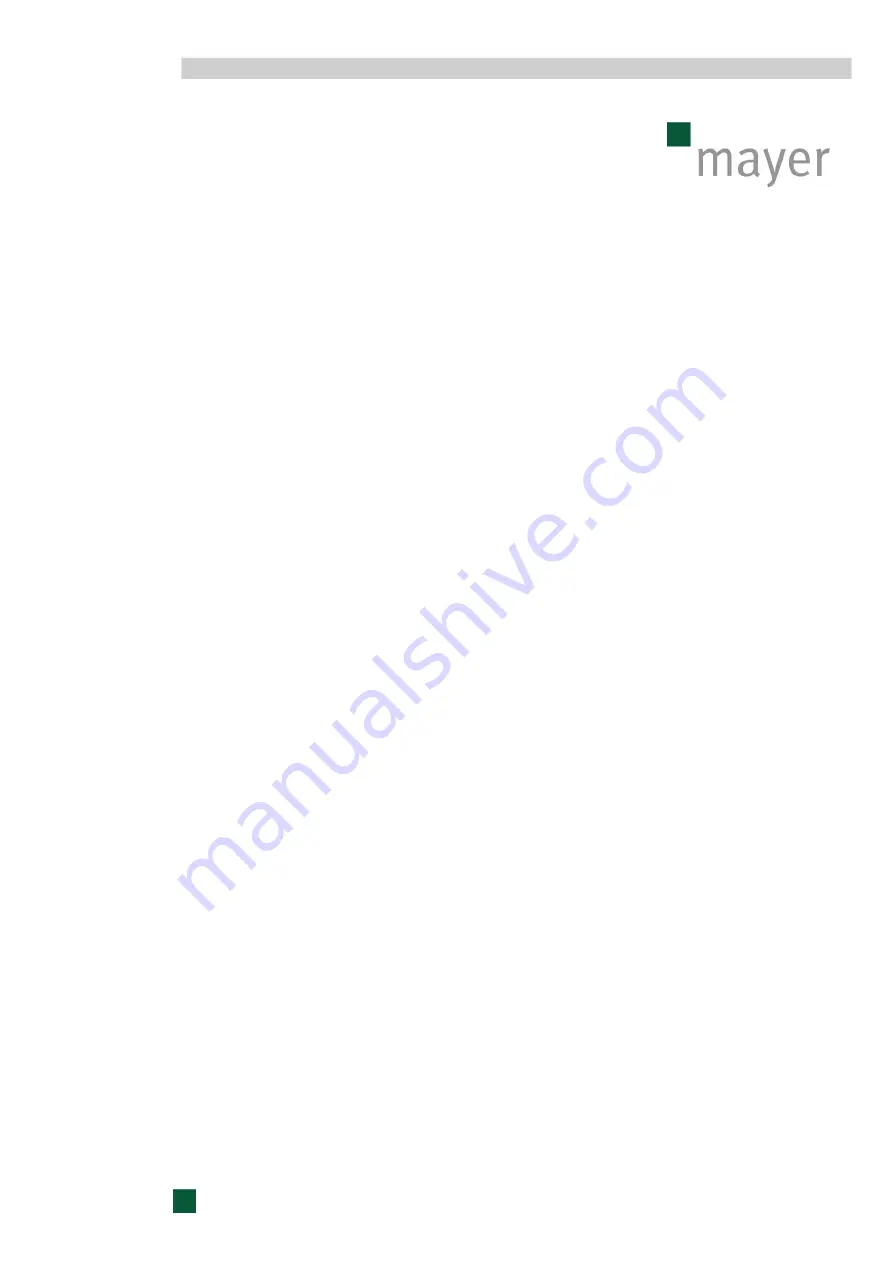
7
2. Starting the pot dispenser
When the machine is connected to compressed air supply, the
pot dispenser will start to operate automatically as soon as the
turntable of the potting machine begins to run.
3. Stopping the pot dispenser
The pot dispenser stops as soon as the potting machine's
turntable comes to a standstill (if the cylinder has already begun
to move, it will stop as has soon as it has reached its final
position).
Summary of Contents for TM 2400DR
Page 4: ...4 2 Structure Plan view of potting machine 2400DR back right left front ...
Page 39: ...39 9 Part list ...
Page 45: ...4 2 Functional description ...
Page 58: ...17 6 Part list ...
Page 60: ...19 ...