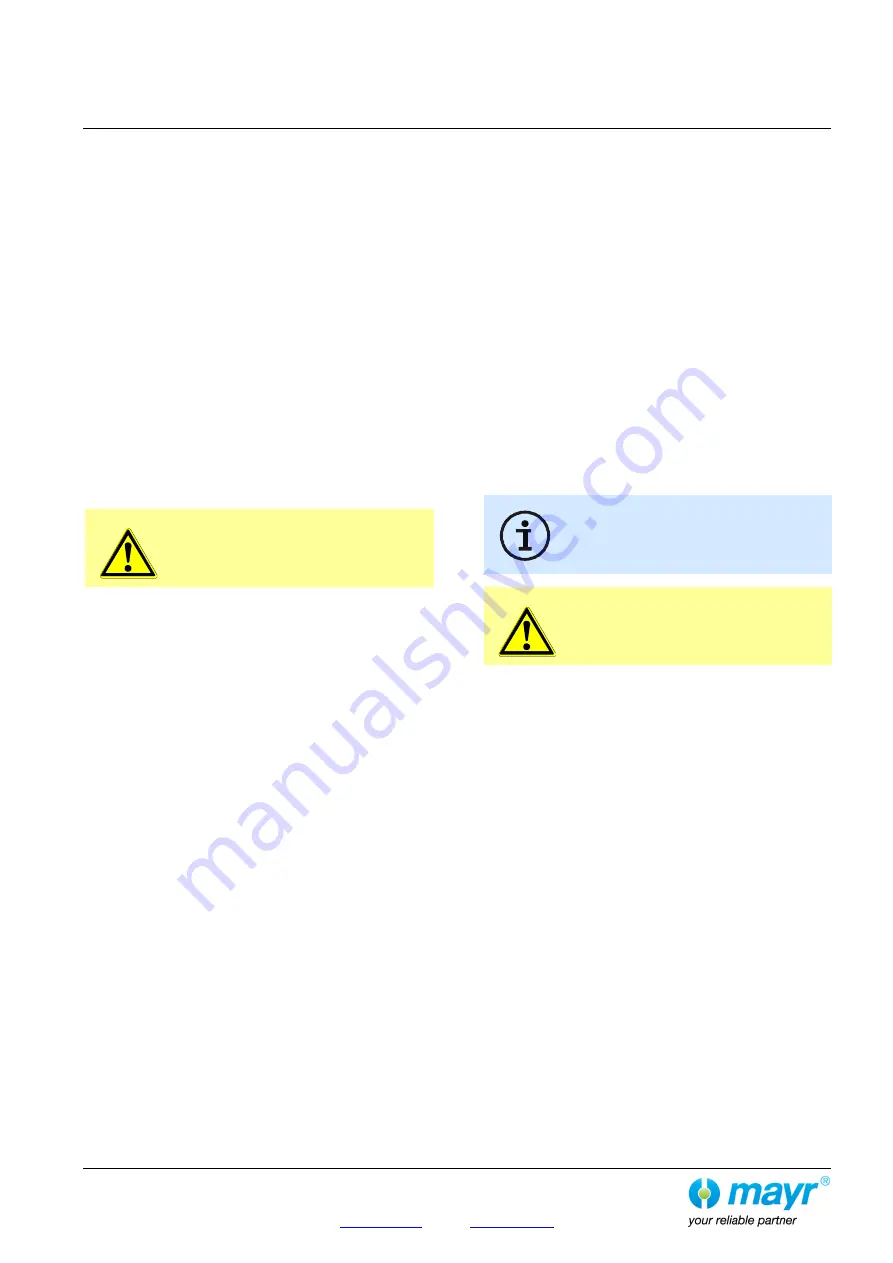
Installation and Operational Instructions for
EAS
®
-dutytorque Type 404_._ _400
Sizes 2
– 9
(B.4.3.1.ATEX.EN)
06/10/2016 TK/GH/SU
Chr. Mayr GmbH + Co. KG
Eichenstraße 1, D-87665 Mauerstetten, Germany
Tel.: +49 8341 804-0, Fax: +49 8341 804-421
Page 7 of 15
Design
EAS
®
-dutytorque clutches are mechanically disengaging
overload clutches (EAS
®
- element clutches) with a mounted,
plug-in elastomer compensating coupling (flexible coupling Nor-
Mex
®
FG).
The overload clutch separates the input and the output on
overload.
When disengaged, the clutch slows down freely without any
residual torque.
The elastomer compensating coupling is the connection to the
output-side shaft end of the system and compensates for
misalignments of the shaft ends (see Table 3, page 6) .
The elastomer compensating coupling consists of the following
components: Flange hub (26), claw ring (24), flexible
intermediate ring (23), cam ring (20) and the cap screws (21).
At the end of the flange hub (26) there is a centring ring (27),
which is intended for holding the claw ring (24) in de-installed
state.
De-installation of the claw ring (24) is necessary when:
the flexible intermediate ring (23) of the coupling must be
replaced (see page 9), or
the running characteristics of the motor in dry running must
be checked; the input and the output can be separated
without moving the motor (see page 9).
CAUTION
This operating state is not permitted under
ATEX conditions, and is in general only
permitted using suitable protective measures.
Scope of Delivery / State of Delivery
The clutch is manufacturer-assembled ready for installation.
The torque is set manufacturer-side according to the
customer's request (please compare the torque stipulated in
the order with the torque imprinted/engraved in the
identification).
Unless the customer requests a particular torque setting
when ordering, the clutch must be adjusted to the required
torque by using the Adjustment Diagram (attachment) (see
section Torque Adjustment).
The clutch is balanced
with a balance quality of G2.5 at 1500 rpm.
Please check the scope of delivery according to the Parts List as
well as the state of delivery immediately after receiving the
goods.
mayr
®
will take no responsibility for belated complaints.
Please report transport damage immediately to the deliverer.
Please report incomplete delivery and obvious defects
immediately to the manufacturer.
Function
The clutch protects the drive line from excessively high,
unpermitted torque impacts which can occur due to unintentional
blockages.
After overload has taken place, the transmitting mechanism is
completely disconnected. Only the bearing friction continues to
have an effect.
This means that no re-engagement impacts or metallic sliding
movements occur on the clutch torque transmission geometries
when using this clutch variant.
When in operation, the set torque is transmitted from the hub (1)
(input) via the pressure flange (5) or the flange hub (26) (flexible
coupling) onto the output.
If the set limit torque is exceeded (overload), the clutch
disengages.
On disengagement, the bolts (7) in the overload elements (6)
perform an axial movement (stroke) and remain disengaged.
Optionally, a switching disk (14) can be mounted onto Type
404_._1400, which is able to actuate a contactless
limit switch
with ATEX certification
(not included in scope of delivery) in
case of overload. The limit switch registers the disengagement
movement and switches off the drive.
The input and the output are separated residual torque-free.
After-acting masses can run free.
The run-out time after disengagement must be
max. 3 minutes.
CAUTION
After overload occurrence, the clutch has no
load-holding function.
The drive can be switched off electrically via:
a speed monitoring device; for this, there are 2 control flags
(Item 15, Fig. 2) in the pressure flange (5) or in the element
flange (3); or
a
limit switch with ATEX approval
(only for design with switching disk (14))
In order to make the clutch function again after overload
occurrence, it must be re-engaged using axial pressure on the
bolt end (7) of each overload element (6) (see Re-engagement,
page 10).
General Installation Guidelines
The bore tolerances in the hub (1) and in the
flange hub (26) are produced to H7. The surface roughness
depth in the bores is produced to Ra 1.6 µm.
Please secure screws with Loctite 243 (medium hard).