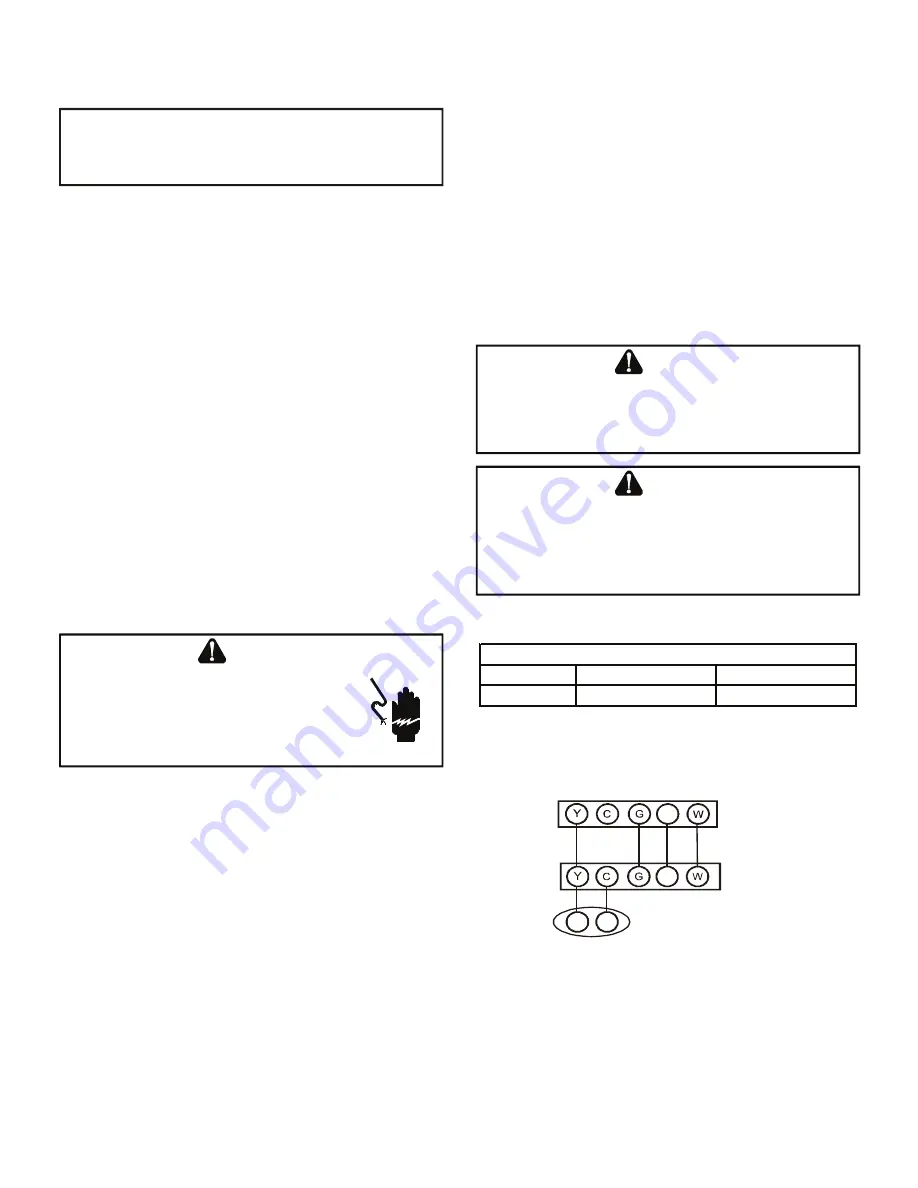
27
Twinning
Furnaces may be twinned without the use of a twinning
kit. Furnaces must be the same model and equipped with
PCBBF
145
control boards. Follow the diagram provided in
this manual. Connection of the “twin” terminals of each
control together will allow simultaneous operation of two
or more furnace indoor blowers to operate synchronously
on a common duct system. Field installed low voltage
thermostat wiring, 3/16” terminals are required to make
this connection. An isolating relay (24 VAC coil & N/O
SPST) contacts is also required if the furnaces are not fed
from the same line voltage phase. A pulsing DC signal is
used to share the call for fan operation between furnac-
es. The duration of the pulse width determines the speed
that the reading control will energize its blower motor.
T
O
PREVENT
UNRELIABLE
OPERATION
OR
EQUIPMENT
DAMAGE
,
THE
GAS
MANIFOLD
PRESSURE
MUST
BE
AS
SPECIFIED
ON
THE
UNIT
RATING
PLATE
. O
NLY
MINOR
ADJUSTMENTS
SHOULD
BE
MADE
BY
ADJUSTING
THE
GAS
VALVE
PRESSURE
REGULATOR
.
CAUTION
WARNING
P
OSSIBLE
PROPERTY
DAMAGE
,
PERSONAL
INJURY
OR
DEATH
MAY
OCCUR
IF
THE
CORRECT
CONVERSION
KITS
ARE
NOT
INSTALLED
. T
HE
APPROPRIATE
KITS
MUST
BE
APPLIED
TO
ENSURE
SAFE
AND
PROPER
FURNACE
OPERATION
. A
LL
CONVERSIONS
MUST
BE
PERFORMED
BY
A
QUALIFIED
INSTALLER
OR
SERVICE
AGENCY
.
Gas Supply and Piping
Natural Gas
Minimum: 4.5" w.c.
Maximum: 10.0" w.c.
Propane Gas Minimum: 11.0" w.c. Maximum: 13.0" w.c.
INLET GAS SUPPLY PRESSURE
The furnace rating plate includes the approved furnace gas input
rating and gas types. The furnace must be equipped to operate
on the type of gas applied. This includes any conversion kits
required for alternate fuels and/or high altitude.
R
Y
C
Furnace Integrated
Control Module
Remote Condensing Unit
(Single-Stage Cooling)
R
Room
Thermostat
Figure 31
Inlet gas supply pressures must be maintained within the ranges
specified in the following table. The supply pressure must be
constant and available with all other household gas fired ap
-
pliances operating. The minimum gas supply pressure must be
maintained to prevent unreliable ignition. The maximum must
3. Relocate junction box and associated plugs and
grommets to opposite side panel. Secure with screws
removed in step
W
IRE
ROUTING
MUST
NOT
INTERFERE
WITH
CIRCULATOR
BLOWER
OPERATION
,
FILTER
REMOVAL
OR
ROUTINE
MAINTENANCE
.
IMPORTANT NOTE
To ensure proper unit grounding, the ground wire should run
from the furnace ground screw located inside the furnace
junction box all the way back to the electrical panel.
NOTE:
Do not use gas piping as an electrical ground. To confirm
proper unit grounding, turn off the electrical power and
perform the following check.
1. Measure resistance between the neutral (white)
connection and one of the burners.
Resistance should measure 10 ohms or less.
This furnace is equipped with a blower door interlock
switch which interrupts unit voltage when the blower door
is opened for servicing. Do not defeat this switch.
24 Volt Thermostat Wiring
Low voltage connections can be made through either the right
or left side panel. Thermostat wiring entrance holes are located
in the blower compartment. The following figure shows con
-
nections for a “heat/cool system”.
This furnace is equipped with a 40 VA transformer to facilitate
use with most cooling equipment. Consult the wiring diagram,
located on the blower compartment door, for further details
of 115 Volt and 24 Volt wiring.
HIGH VOLTAGE !
T
O
AVOID
PERSONAL
INJURY
OR
DEATH
DUE
TO
ELECTRICAL
SHOCK
,
DISCONNECT
ELECTRICAL
POWER
BEFORE
SERVICING
OR
CHANGING
ANY
ELECTRICAL
WIRING
.
WARNING
Single-Stage Heating Thermostat Application
A single-stage thermostat with only one heating stage is
needed to control this furnace.
Fossil Fuel Applications
This furnace can be used in conjunction with a heat pump in
a fossil fuel application. A fossil fuel application refers to a
combined gas furnace and heat pump installation which uses
an outdoor temperature sensor to determine the most cost
efficient means of heating (heat pump or gas furnace).
Strictly follow the wiring guidelines in the fossil fuel kit in-
stallation instructions. All furnace connections must be made
to the furnace two-stage integrated control module and the
“FURNACE” terminal strip on the fossil fuel control board.