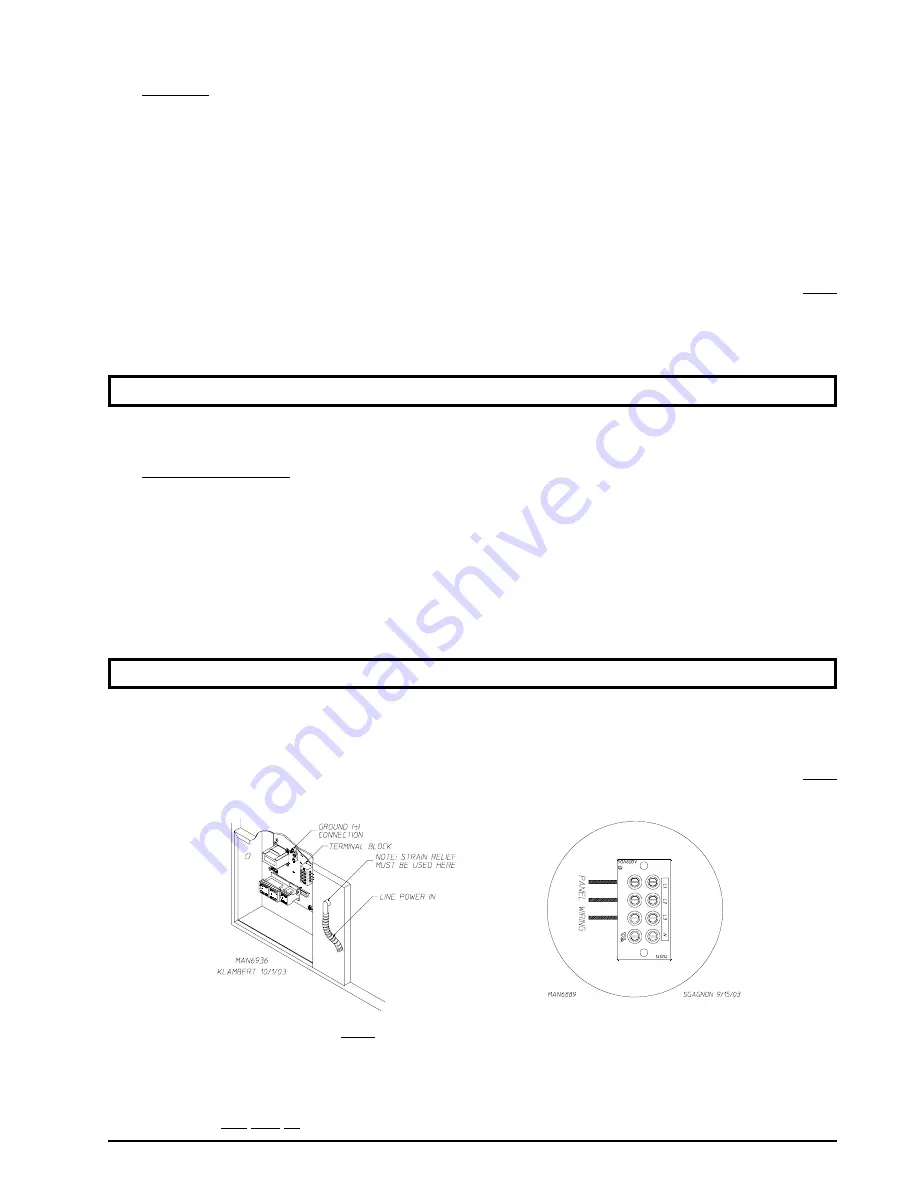
113395 - 6
Maytag Co.
21
3. Grounding
A ground (earth) connection
must be
provided and installed in accordance with state and local codes. In
the absence of these codes, grounding
must conform
to applicable requirements of the National Electrical
Code ANSI/NFPA NO. 70-LATEST EDITION, or in Canada, the installation
must conform
to applicable
Canada Standards: Canadian Electrical Codes Parts 1 & 2 CSA C22.1-1990 or LATEST EDITION. The
ground connection may be to a proven earth ground at the location service panel.
For added personal safety, when possible, it is suggested that a separate ground wire (size per local codes)
be connected from the ground connection of the dryer to a grounded cold water pipe.
DO NOT ground to
a gas pipe or hot water pipe
. The grounded cold water pipe must have
metal-to-metal connection
ALL
the way to the electrical ground. If there are any nonmetallic interruptions, such as, a meter, pump, plastic,
rubber, or other insulating connectors, they
must be
jumped out with a wire (size per local codes) and
securely clamped to bare metal at both ends.
IMPORTANT:
For personal safety and proper operation, the dryer
must be
grounded.
Provisions are made for ground connection in each dryer at the electrical service connection area.
4. Electrical Connections
A wiring diagram is located inside the control box for connection data.
If local codes permit, power to the dryer can be made by the use of a flexible U.L. listed power cord/pigtail
(wire size
must conform
to rating of dryer), or the dryer can be hard wired directly to the service breaker
panel. In both cases, a strain relief
must be
installed where the wiring enters the dryer.
3-Phase (3ø) Wiring Connections/Hookup
IMPORTANT:
A separate protected circuit
must be
provided to each dryer.
The only electrical input connections to the dryer are the 3-phase (3ø) power leads (L1, L2, and L3),
GROUND, and in the case of 4-wire service, the neutral. Providing local codes permit, power connections
to the dryer can be made by the use of a flexible underwriters laboratory listed cord/pigtail (wire size
must
conform
to rating of the dryer), or the dryer can be hard wired directly to the service breaker. In
ALL
cases, a strain relief
must be
used where the wire(s) enter the dryer electrical service (relay) box.
The electrical connections on
ALL
3-phase (3ø) gas and steam dryers are made into the rear service box
located at the upper left area of the dryer. The electrical connections are made at the power distribution
block located in the service box. The ground connection is made to the copper lug, also provided in this box.
To gain access, the service box cover
must be
removed.
The neutral will only be used on 4-wire service. This is typical for 380-416V, 50 Hz.
Summary of Contents for MD-170PTVW
Page 52: ...Part No 113395 6 05 01 07 0...