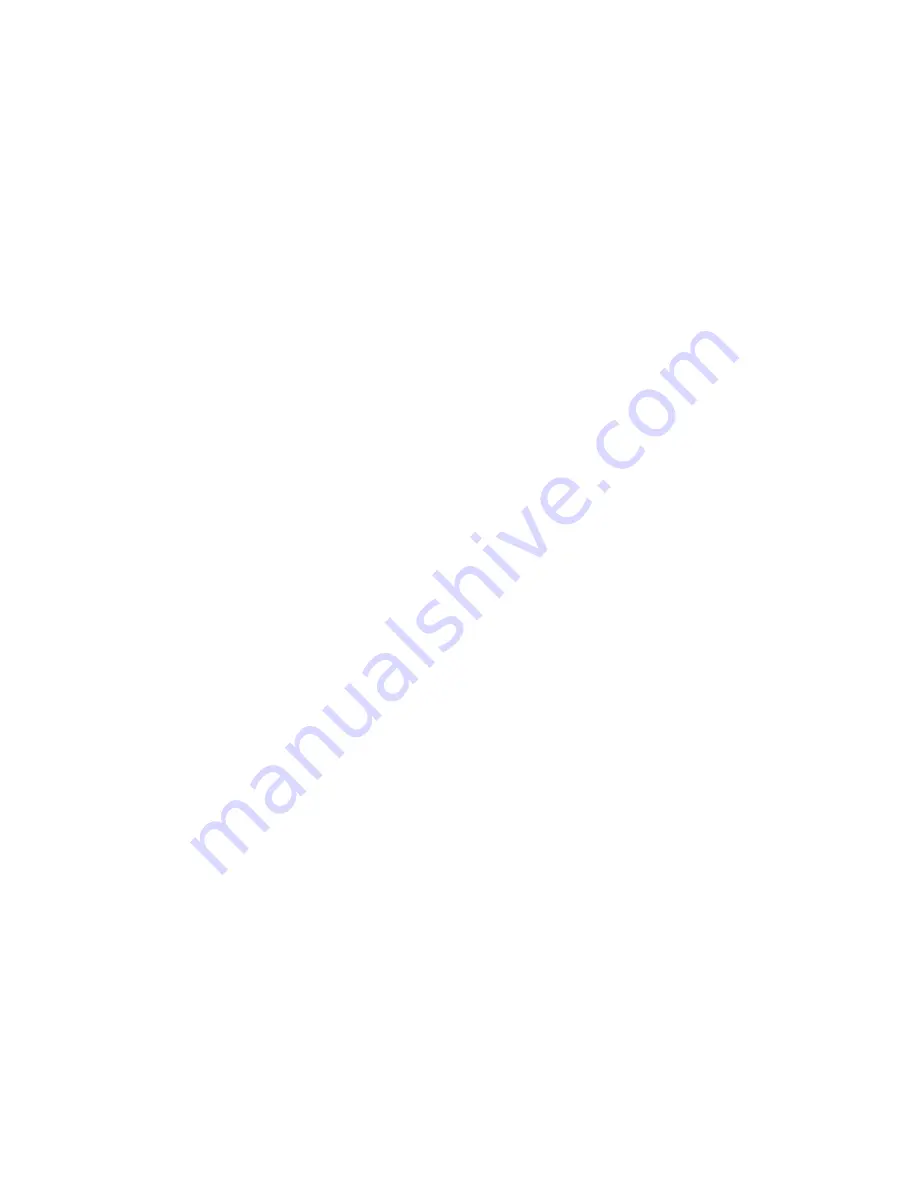
OPERATION OF OIL BURNER
Once the furnace flue pipe, electrical and oil line
connections have been made, use the following
instructions to set the burner:
Shut off the electrical power to the furnace.
Install an oil pressure gauge to the pressure port on
the oil pump. (Refer to the oil pump specification sheet
included with the burner instructions).
Restore electrical power to the furnace.
Start the furnace and bleed all air from the fuel oil
lines.
Close the purge valve and fire the unit.
Allow the furnace to warm up to normal operating
temperatures. During this time, set the pump pressure
in accordance with the data provided in Appendix A,
Table A-1.
When the furnace has reached "
steady state
" (after
approximately 10 minutes). Set combustion air damper
to get a TRACE of smoke.
Check the system temperature rise.
The temperature
rise is the difference between the return air temperature
measured at a point near the return air inlet, and the
supply air temperature measured near the furnace
outlet
. The system temperature rise is listed on the
furnace rating plate. If the temperature rise is too high,
the airflow must be increased. If the temperature rise is
too low, the fan should be slowed down.
Turn off the burner. Observing the duct thermometer in
the supply air stream, note the temperature at which
the blower fan stops. The fan adjustments can be
made by moving the dipswitch settings on the timer
control board for fan off delay.
To check the operation of the limit switch, shut off
power to the furnace. Temporarily remove the neutral
wire from the direct drive blower motor. Restore the
electrical power to the furnace and set the thermostat
above room temperature. After three or four minutes of
burner operation, the limit control should turn the
burner off. When the limit function test is complete,
shut off electrical power to the furnace, replace the
neutral wire to the blower fan motor, and then restore
power. The blower fan will start up immediately. Once
the temperature has dropped and the limit control has
reset, the fan will operate until the fan off time is
achieved. The oil burner will then resume operation
and continue until the thermostat is satisfied. Restore
the thermostat setting to a comfortable temperature.
Set the heat anticipator adjustment in the thermostat (if
so equipped), by removing the "R" or "W" wire to the
thermostat, then reading the amperage draw between
the two wires. Failure to remove one of the wires from
the thermostat while performing this test could burn out
the heat anticipator. Set the heat anticipator to the
amperage measured.
NOTE: THE FURNACE SHOULD BE RUN
THROUGH AT LEAST THREE FULL CYCLES
BEFORE LEAVING THE INSTALLATION, TO
ENSURE THAT ALL CONTROLS ARE
OPERATING PROPERLY AND AS EXPECTED.
NOTE: ALL JOINTS IN ANY POSITIVE
PRESSURE VENTING SYSTEM MUST BE
CHECKED FOR LEAKS BEFORE LEAVING
THE INSTALLATION SITE.
18
Summary of Contents for POF1HD091AVFA
Page 30: ...30...
Page 33: ...33...
Page 36: ...NOTES Nordyne Inc 8000 Phoenix Parkway O Fallon Missouri 63368 766B 0909...