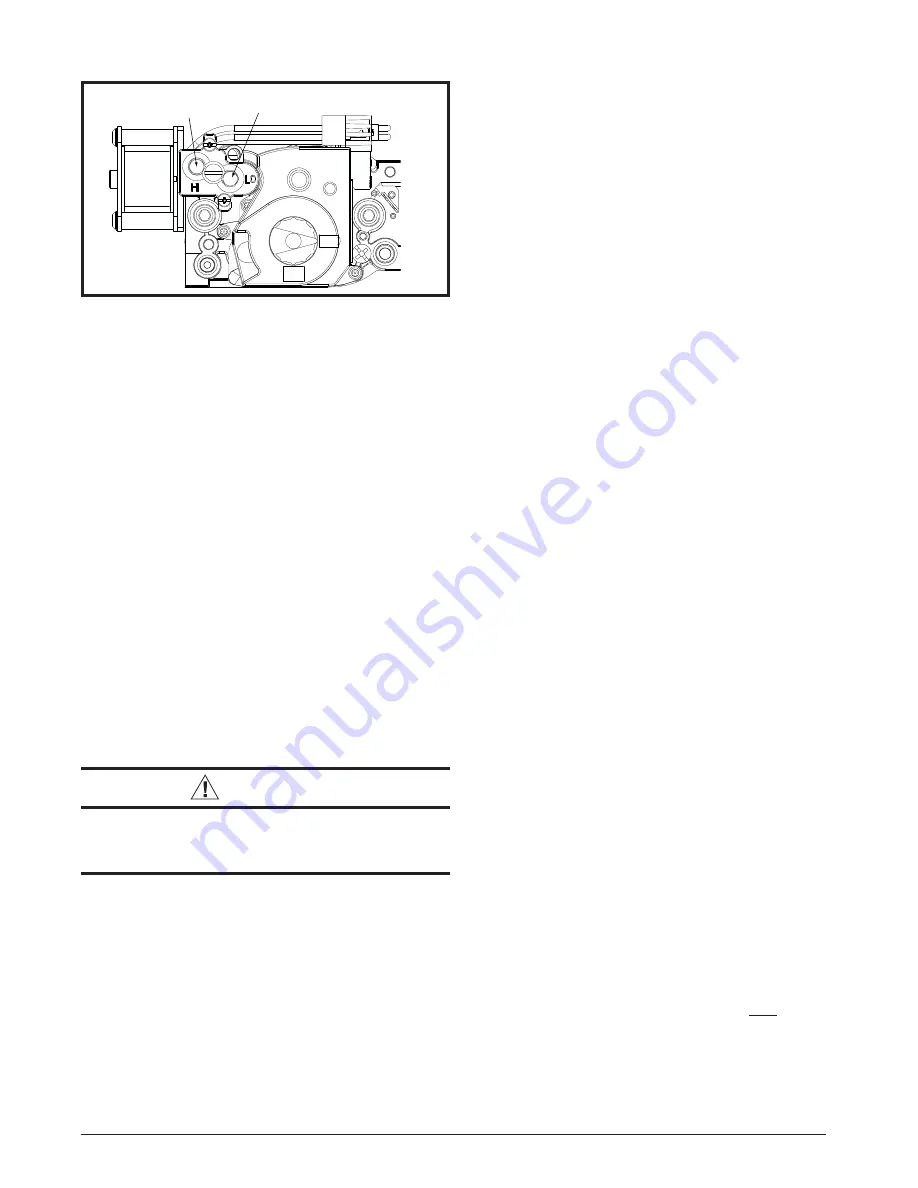
29
1. Place thermometers in the return and supply air
stream as close to the furnace as possible. To avoid
false readings, the thermometer on the supply air side
must be shielded from direct radiation from the heat
exchanger.
2. Adjust all registers and duct dampers to the desired
position and run the furnace for 10 to 15 minutes in
high fi re before taking any temperature readings. The
temperature rise is the difference between the supply
and return air temperatures.
For typical duct systems, the temperature rise will fall
within the limits specifi ed on the rating plate with the
blower speed at the factory recommended setting. If
the measured temperature rise is outside the specifi ed
limits, it may be necessary to change the speed of the
blower.
NOTE:
Lowering the blower speed increases the
temperature rise and a higher blower speed will decrease
the temperature rise.
The furnace is equipped with a multi-speed motor. Heating
and cooling speed selection is made by moving the
switches on the integrated control located in the furnace.
Verifying Burner Operation
CAUTION:
The door over the burners may only be open
for inspection purposes only. The door must be
installed during unattended operation.
1. Remove the burner compartment door.
2. Set the thermostat above room temperature and
observe the ignition sequence. The burner fl ame should
carry over immediately between all burners without
lifting off, curling, or fl oating. The fl ames should be
blue, without yellow tips.
3. After validating flame characteristics, change
thermostat setting to below room temperature.
4. Verify burner fl ame is completely extinguished.
5. Replace the burner compartment door.
HI Input
Adjusting Screw
Lo Input
Adjusting Screw
Figure 28. HI & LO Input Adjusting Screws
Verifying Operation of the Supply Air Limit
Switch
A properly functioning limit switch should turn off the
gas valve when the return is blocked (time depends on
how well the return air is blocked). The circulating air and
combustion blowers should continue to run when the limit
switch opens.
1. Check the blower door for secure mounting and that
there is power to the furnace.
2. Block the return airfl ow to the furnace by installing a
close-off plate in place of or upstream of the fi lter(s).
3. Set the thermostat above room temperature and
observe the Operating Sequence.
4. Remove the close-off immediately after the limit switch
opens. If the furnace continues to operate with no
return air, set the thermostat below room temperature,
shut off the power to the furnace, and replace the limit
switch.
OPERATING SEQUENCE
The operating sequences for the heating, cooling, and fan
modes are described below. Refer to the fi eld and furnace
wiring diagrams: (Figure 23, page 25), (Figures 24 - 26,
page 26), & (Figures 33 - 36, pages 41 - 44).
Heating Cycle
1. The thermostat calls for heat by energizing the
W1
terminal with 24VAC.
2. The control checks to see the pressure switch is open.
If the switch is closed, the furnace will shut down for
5 minutes before retrying
3. If the pressure switch is open, the control energizes
the inducer motor and waits for the pressure switch
to close. The pressure switch must close within 12
seconds.
4. The control runs the inducer for a 30 second pre-purge
time.
5. The control energizes the igniter output for the
appropriate adaptive warm-up time limit.
6. The furnace always ignites the burners in
high
fi re. If
the call for heat is for
low
rate, the furnace will move
down to
low
fi re after the fl ames stabilize.
7. If the fl ame is proved and ignites the gas, the control
de-energizes the igniter. The gas valve and inducer
remains energized. The control goes to blower on
delay.
8. The control energizes the blower on the selected
HEAT speed 30 seconds after the gas valve opened.
The gas valve and inducer remain energized.
9. If there is a call for
high
fi re, the gas valve moves
to the
high
fi re position and the blower speeds are
increased. The furnace will remain in high fi re until
the demand for heat is satisfi ed.
10. If autostaging is enabled (single stage thermostat) the
demand for heat has lasted more than the selected
time, the furnace automatically moves up to
high
fi re.
Autostage times are either
SHORT
(8 minutes),
LONG
Summary of Contents for *TC
Page 51: ...51...