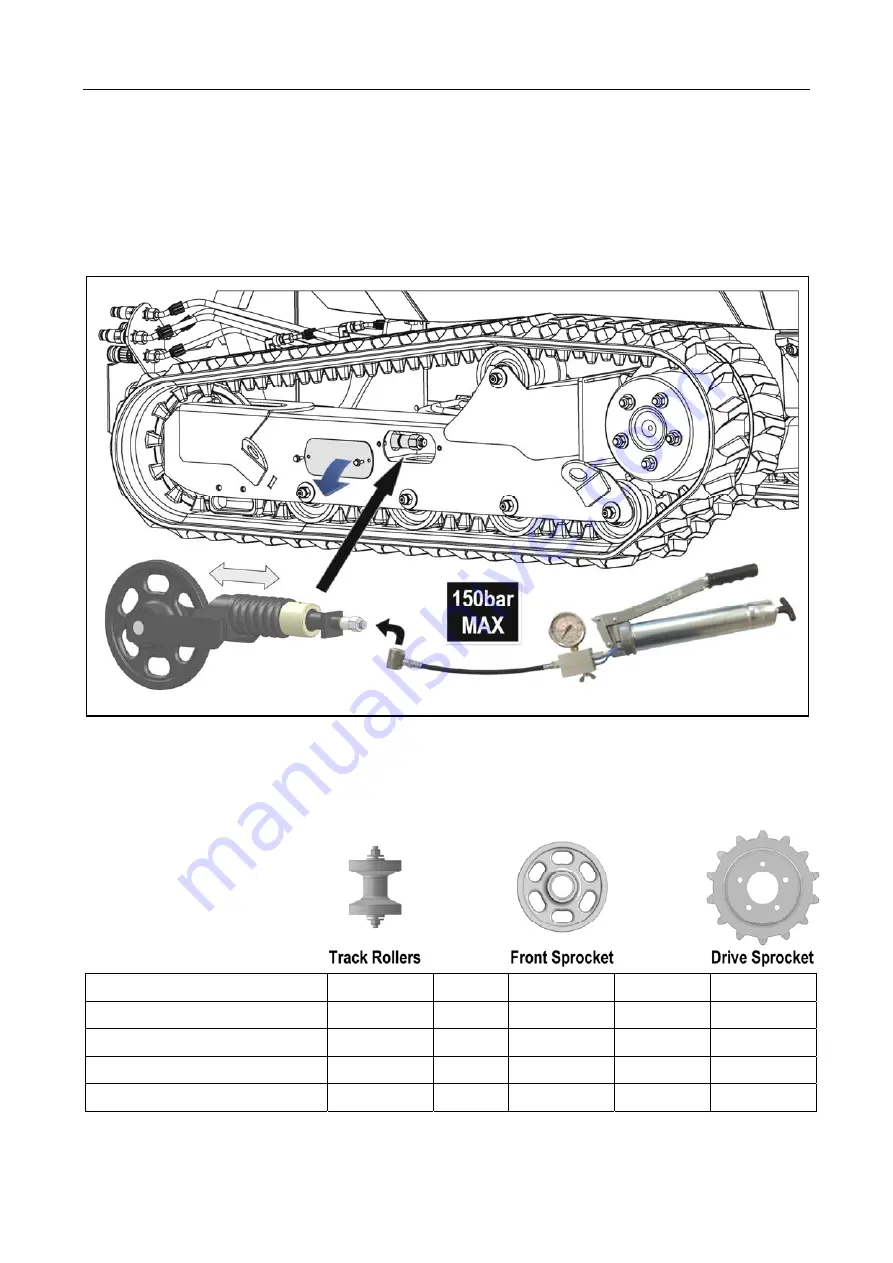
52
TRACK TENSIONING SYSTEM
The tracks on the machine are tensioned using a grease tensioning system.
Adjustment to track tension is made by pumping or draining grease through the adjusters
located behind cover plates on each side of the undercarriage.
When grease is pumped into the track adjuster it expands a cylinder, this moves the track
idler wheel forwards exerting tension on the track.
Grease is added to the tensioning system using a track tensioning grease gun equipped
with a pressure gauge and adaptor hose (P/N: 4008064).
Correct track tension is
130-150bar (Max)
.
The adjusters should be checked on a regular basis to ensure track tension is correctly
maintained; if track tension is too low there is a heightened risk of the track coming off
whilst operating the machine, if track tension is excessive it will increase the wear rate of
track and/or track components.
Wear Limits
Track components shown
opposite must be replaced
as soon as they reach their
maximum wear limit; this
corresponds to the 100%
worn figures stated below.
Lubrication of Undercarriage Components
Components of the tracked undercarriage (rollers, pins, bushings etc.), must be greased
every 20 working hours.
Ø
when new
►
130.0mm
264.0mm 290.0mm
Ø at 25% wear
►
128.0mm
263.0mm 289.0mm
Ø at 50% wear
►
126.0mm
261.5mm 287.5mm
Ø at 75% wear
►
124.0mm
259.5mm 285.5mm
Ø at 100% wear
►
121.0mm
257.0mm 283.0mm
Track Tensioner Track Tensioner Kit (4008064)