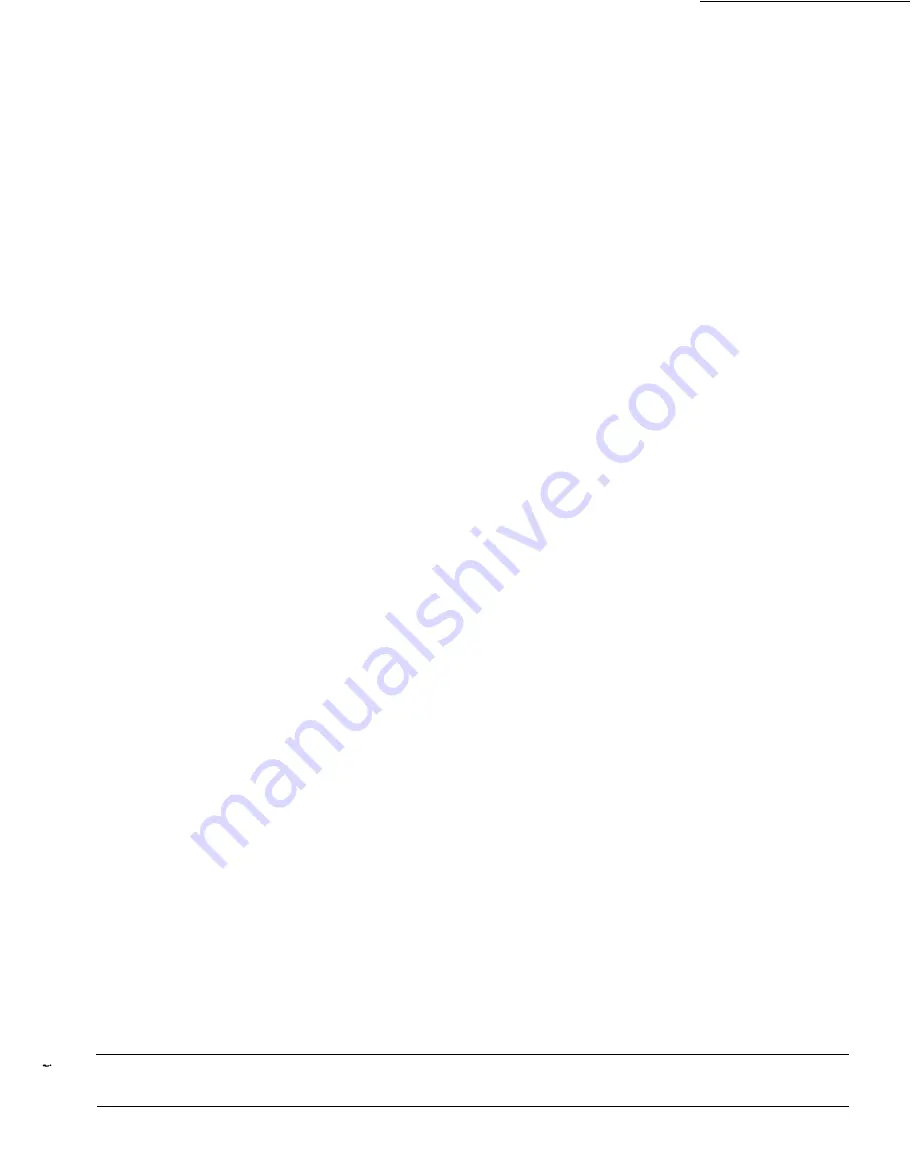
APPLICATION
The operation and maintenance procedures presented in this
manual apply to the standard model PEH chillers and the
In the application of cooling towers with McQuay model
model PHH heat recovery chillers. Reference to the installa-
PEH centrifugal chillers, the towers are normally selected for
tion manual for these units should be made for details per-
maximum condenser inlet water temperature on the order of
85°F.
taining to receiving and handling, installation, piping and wir-
ing, and preparation for initial startup.
Lower entering water temperature may be desirable from
All McQuay centrifugal chillers are factory tested prior to
the standpoint of energy performance but a minimum does
shipment and must be initially started by a factory trained
exist. For recommendations for optimum entering water
McQuay Service technician. Failure to follow this startup pro-
temperature and cooling tower fan control, consult McQuay
cedure may affect the equipment warranty.
Catalog 950, Applications Section.
The standard warranty on this equipment covers parts
The operating and maintenance procedures for the PEH
which prove defective in material or workmanship. Specific
and PHH chillers are identical in most respects; therefore,
details of this warranty can be found in the warranty state-
all references made in this manual for the PEH chillers will
ment furnished with the equipment.
equally apply to the PHH models unless specifically noted.
For simplicity, only the PEH designation will be used.
OPERATION
OPERATOR RESPONSIBILITIES
It is important that the operator become familiar with the
equipment and the system before attempting to operate the
chiller.
In addition to reading this manual the operator should study
the control diagram furnished with the unit so that he
understands the starting, operating and shutdown sequences
as well as the safety shutdown modes.
When the McQuay Service technician performs the initial
startup of the chiller he will be available to answer any ques-
tions and to instruct in proper operating procedures.
It is recommended that the operator maintain an operating
log for each individual chiller unit. A suggested log sheet is
shown on page 23 of this manual.
In addition, a separate maintenance log should be kept of
the periodic maintenance and servicing activities.
This McQuay centrifugal chiller represents a substantial
investment and deserves the attention and care normally
given to keep this equipment in good working order. If the
operator should encounter abnormal or unusual operating
conditions, it is recommended that a McQuay Service techni-
cian be consulted.
McQuay conducts training for centrifugal operators at its
factory Training Center several times a year. These sessions
are structured to provide basic classroom instruction and in-
clude hands-on operating and troubleshooting exercises. For
further information, contact your McQuay representative.
NOMENCLATURE
Each centrifugal chiller is assigned a set of identifying
numbers which are used to describe the unit features and
to identify each individual unit. These four-number groups
are stamped on each unit nameplate.
All inquiries pertaining to operating and servicing of this
unit should include all identification numbers.
Each of the individual components also have nameplates
to provide certain necessary information to the installer and
the operator.
The compressor nameplate identifies the compressor
model, style and serial numbers and includes the electrical
characteristics of the compressor motor. The CEO50 com-
pressor nameplate also shows the oil pump electrical
characteristics.
The condenser and evaporator vessels have nameplates
stamped with the maximum working pressure of the vessel.
It should be noted that the vessel relief valve maximum set-
tings coincide with the maximum refrigerant side vessel work-
ing pressure.
NOMENCLATURE CHANGE: The letter “H” has been added behind the first two digits of the model code to signify a hermetic
compressor motor. Models PE and PH are synonymous with PEH and PHH respectively.
IM 307 I Page 3