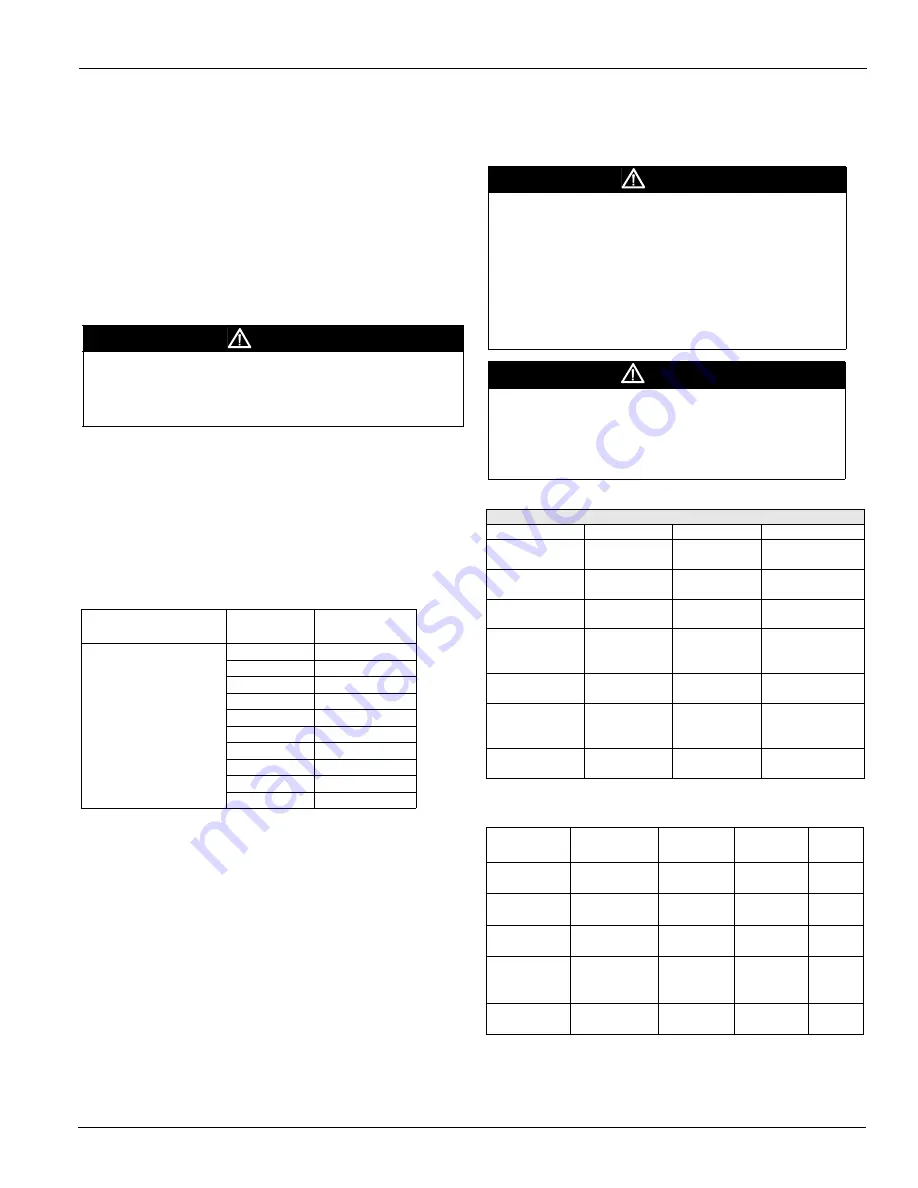
McQuay IM 777-6
23
Service and Maintenance
Service and Maintenance
Periodic Maintenance
1
Check all moving parts for wear every six months.
2
Check bearing collar, sheave, and wheel hub setscrews,
sheave capscrews, and bearing hold-down bolts for
tightness every six months.
3
Annually check and snug all electrical connections.
Inspect for signs of water damage such as corrosion and
repair if necessary. Check ground conductor and
connection integrity. Service if needed.
Ball Bearing Lubrication
Motor Bearings
Supply and return fans
—Supply and return fan motors
should have grease added after every 2000 hours of operation.
Using the following procedure, relubricate the bearings while
the motor is warm, but not running. Use one of the greases
shown in
Table 15
.
1
Remove and clean upper and lower grease plugs.
2
Insert a grease fitting into the upper hole and add clean
grease (
Table 15
) with a low pressure gun.
3
Run the motor for five minutes before replacing the
plugs.
Note:
Specific greasing instructions are located on a tag
attached to the motor. If special lubrication instructions
are on the motor, they supersede all other instructions.
Fan Shaft Bearings
Any good quality lithium or lithium complex base grease,
using mineral oil, conforming to NLGI grade 2 consistency,
and an oil viscosity of 455-1135 SUS at 100°F (100-200 cSt at
40°C) may be used for relubrication.
Compatibility of grease is critical. Relubricatable bearings are
supplied with grease fittings or zerks for ease of lubrication
with hand or automatic grease guns. Always wipe the fitting
and grease nozzle clean.
Note:
Temperature ranges over 225°F are shown for lubricants only. High
temperature applications are not suitable for standard air handler
components.
CAUTION
Bearing overheating potential. Can damage the equipment.
Do not overlubricate bearings. Use only a high grade mineral
grease with a 200°F safe operating temperature. See below for
specific recommended lubricants.
Table 15: Recommended Lubricants and Amounts for Fan
Motor Bearings
Mfr. Grease
NEMA Size
Amount to Add
(oz.)
Texaco, Polystar
or
Polyrex EM (Exxon Mobile)
or
Rykon Premium #2
or
Penzoil Pen 2 Lube
56 to 140
0.08
140
0.15
180
0.19
210
0.30
250
0.47
280
0.61
320
0.76
360
0.81
400
1.25
440
2.12
CAUTION
For safety, stop rotating equipment. Add one half of the
recommended amount shown in
Figure 18
. Start bearing,
and run for a few minutes. Stop bearing and add the second
half of the recommended amount. A temperature rise,
sometimes 30°F (1°C), after relubrication is normal. Bearing
should operate at temperature less than 200°F (94°C) and
should not exceed 225°F (107°C) for intermittent operation.
For a relubrication schedule, see
Table 16
. For applications
that are not in the ranges of the table, contact McQuay.
CAUTION
The tables below state general lubrication
recommendations based on our experience and are
intended as suggested or starting points only. For best
results, specific applications should be monitored regularly
and lubrication intervals and amounts adjusted accordingly.
Table 16: Relubrication Intervals
(Use NLGI #2 Lithium or Lithium Complex Grease)
Speed
Temperature
Cleanliness
Relub. intervals
100 rpm
Up to 120°F
(50°C)
Clean
6 to 12 months
500 rpm
Up to 150°F
(65°C)
Clean
2 to 6 months
1000 rpm
Up to 210°F
(100°C)
Clean
2 weeks to 2
months
1500 rpm
Over 210°F
(100°C) to
250°F (120°C)
Clean
Weekly
Above 1500 rpm
Up to 150°F
(65°C)
Dirty/wet
1 week to 1 month
Max catalog rating
Over 150°F
(65°C) to 250°F
(120°C)
Dirty/wet
Daily to 2 weeks
Above 250°F
(120°C)
Contact Browning
Table 17: Recommended Lubricants for Fan Shaft Ball
Bearings
Name
Temperature
Base
Thickener
NLGI
grade
Texaco,
Premium RB
30° to 350°F
(34° to 177°C)
Parafinic
mineral oil
Lithium
2
Mobile, AW2
40° to 437°F
(40° to 175°C)
Mineral oil
Lithium
2
Mobile, SHC
100
68° to 356°F
(50° to 180°C)
Synthetic
Lithium
2
Chevron,
Altiplex
Synthetic
60° to 450°F
(51° to 232°C)
Synthetic
Lithium
2
Exxon, ronex
MP
40° to 300°F
(40° to 149°C)
Mineral oil
Lithium
2
Summary of Contents for Skyline IM 777-6
Page 37: ......