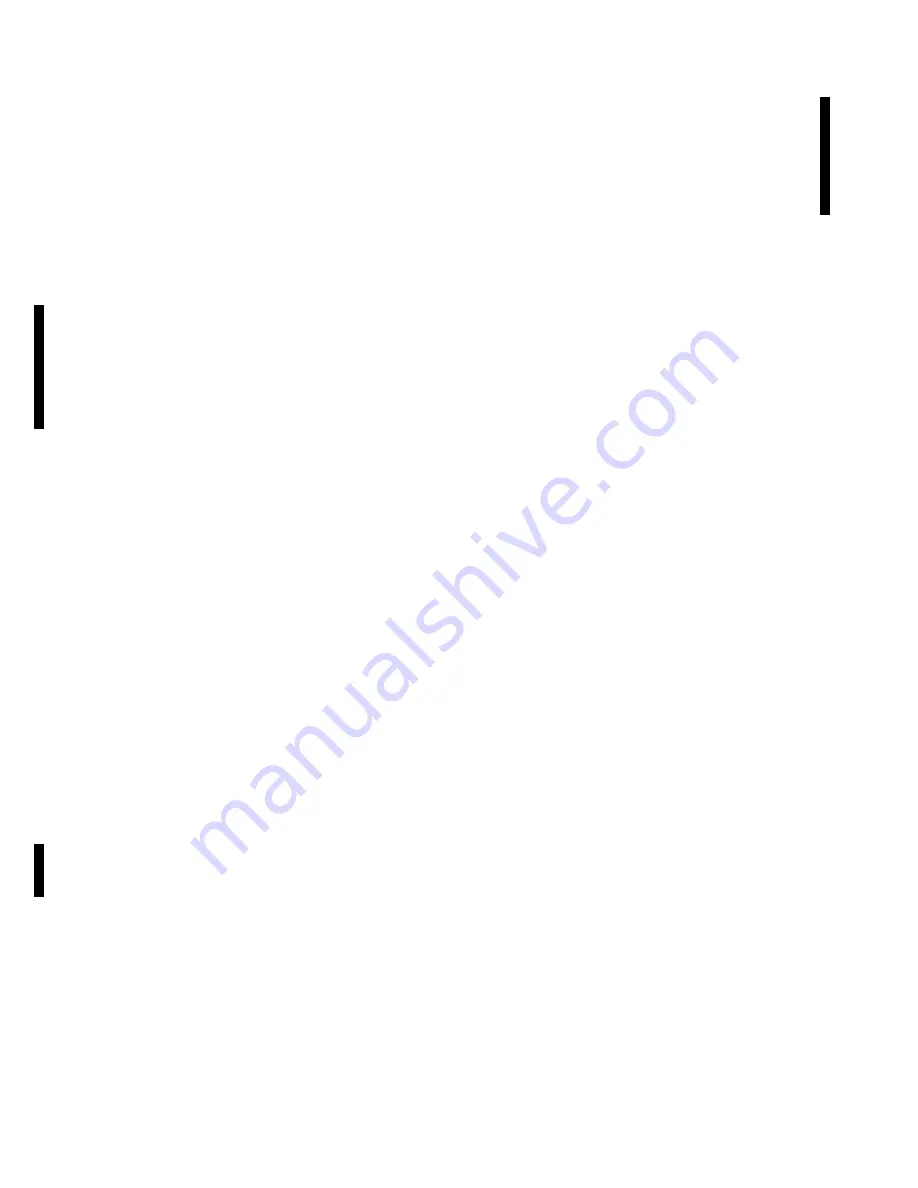
CSP
−
900RMM
−
2
MD Helicopters, Inc.
Rotorcraft Maintenance Manual
Page 202
Revision 22
29-00-00
(e). Operate flight controls through a
minimum of 25 full-stroke cycles
with the hydraulic system pressur
ized
.
(f). Leakage at the gland seals or at
weep holes shall not exceed 1 drop
per 25 cycles.
(g). Depressurize system and remove
(2). Operate pumps by ground running
helicopter on one engine at idle (65%)
RPM per current Rotorcraft Flight
Manual (Ref. Section 01-00-00,
Table 201) and inspect the pumps seal
drain for a maximum seepage of 5
drops in 3 minutes.
C. Hydraulic System Static Leak Test
NOTE:
Leakages are based on a static leakage
rate of 10 drops per dynamic seal.
(1). When main rotor control actuator
leakage is observed on aircraft standing
idle, the following procedure shall be
used to determine if leakage is unac
ceptable:
(2). Wipe actuator and clean up any fluid
spillage.
(3). Re-inspect in 24 hours. Accumulated
leakage from any of the three servoac
tuators shall not exceed the equivalent
of one teaspoon or roughly a fluid spot
not exceeding eight inches in diameter.
D. Hydraulic System Operational Test
(Aircraft Ground Run)
(1). Ground run helicopter per current
Rotorcraft Flight Manual (Ref. Section
01-00-00, Table 201).
(2). Perform hydraulic system check per
current Rotorcraft Flight Manual
(Ref. Section 01-00-00, Table 201).
(3). Shut down helicopter per current
Rotorcraft Flight Manual (Ref. Section
01-00-00, Table 201).
E. Hydraulic System Functional Test (with
GSE Pressure).
(1). Apply power to dc buses and close IIDS
circuit breaker (Ref. Section 96-00-00).
(2). Verify
1 HYD 2
caution segments
illuminate on IIDS panel.
(3). Select
HYD PRESS
on IIDS alphanu
meric display (Ref. Section 95-00-00).
(4). Apply 1000 psig external hydraulic
pressure to system 1 (Ref. Section
29-00-00).
(5). Slowly decrease pressure to 200 psig
and then slowly increase pressure to
1000 psig.
NOTE:
Hydraulic system 2 caution segment
should remain illuminated throughout this
portion of test.
(a). Verify pressure indication on IIDS
panel alphanumeric display.
(b). Verify that hydraulic system 1
caution segment illuminates before
250 psig and that segment goes out
at or before 510 psig.
(6). Remove external hydraulic pressure
and disconnect GSE cart from system 1
GSE ports (Ref. Section 29-00-00).
(7). Turn off dc power (Ref. Section
96-00-00).
(8). Repeat Steps E-1 through E-8 for
system 2.
Summary of Contents for CSP-900RMM-2
Page 19: ...CSP 900RMM 2 MD Helicopters Inc Rotorcraft Maintenance Manual INTRODUCTION Chapter ...
Page 20: ......
Page 23: ...CSP 900RMM 2 MD Helicopters Inc Rotorcraft Maintenance Manual Section 01 00 00 Introduction ...
Page 24: ......
Page 44: ......
Page 48: ......
Page 62: ......
Page 68: ......
Page 74: ......
Page 78: ......
Page 84: ......
Page 100: ......
Page 122: ......
Page 154: ......
Page 223: ...CSP 900RMM 2 MD Helicopters Inc Rotorcraft Maintenance Manual DIMENSIONS AND AREAS Chapter ...
Page 224: ......
Page 228: ......
Page 249: ...CSP 900RMM 2 MD Helicopters Inc Rotorcraft Maintenance Manual LIFTING AND JACKING Chapter ...
Page 250: ......
Page 254: ......
Page 260: ......
Page 264: ......
Page 273: ...CSP 900RMM 2 MD Helicopters Inc Rotorcraft Maintenance Manual Section 08 20 00 Leveling ...
Page 274: ......
Page 277: ...CSP 900RMM 2 MD Helicopters Inc Rotorcraft Maintenance Manual TOWING Chapter ...
Page 278: ......
Page 281: ...CSP 900RMM 2 MD Helicopters Inc Rotorcraft Maintenance Manual Section 09 00 00 Towing ...
Page 282: ......
Page 286: ......
Page 287: ...CSP 900RMM 2 MD Helicopters Inc Rotorcraft Maintenance Manual PARKING AND MOORING Chapter ...
Page 288: ......
Page 292: ......
Page 299: ...CSP 900RMM 2 MD Helicopters Inc Rotorcraft Maintenance Manual Section 10 20 00 Mooring ...
Page 300: ......
Page 306: ......
Page 308: ......
Page 311: ...CSP 900RMM 2 MD Helicopters Inc Rotorcraft Maintenance Manual PLACARDS AND MARKINGS Chapter ...
Page 312: ......
Page 316: ......
Page 333: ...CSP 900RMM 2 MD Helicopters Inc Rotorcraft Maintenance Manual SERVICING Chapter ...
Page 334: ......
Page 337: ...CSP 900RMM 2 MD Helicopters Inc Rotorcraft Maintenance Manual Section 12 00 00 Servicing ...
Page 338: ......
Page 368: ......
Page 372: ......
Page 390: ......
Page 401: ...CSP 900RMM 2 MD Helicopters Inc Rotorcraft Maintenance Manual Section 21 20 00 Vent System ...
Page 402: ......
Page 416: ......
Page 458: ......
Page 466: ......
Page 525: ...CSP 900RMM 2 MD Helicopters Inc Rotorcraft Maintenance Manual EQUIPMENT FURNISHINGS Chapter ...
Page 526: ......
Page 542: ......
Page 544: ......
Page 570: ......
Page 572: ......
Page 584: ......
Page 590: ......
Page 594: ......
Page 596: ......
Page 602: ......
Page 604: ......
Page 622: ......
Page 624: ......
Page 626: ......
Page 627: ...CSP 900RMM 2 MD Helicopters Inc Rotorcraft Maintenance Manual Section 25 60 10 Rescue Hoist ...
Page 628: ......
Page 632: ......
Page 644: ......
Page 646: ......
Page 648: ......
Page 654: ......
Page 655: ...CSP 900RMM 2 MD Helicopters Inc Rotorcraft Maintenance Manual FIRE PROTECTION Chapter ...
Page 656: ......
Page 662: ......
Page 672: ......
Page 678: ......
Page 686: ......
Page 692: ......
Page 698: ......
Page 711: ...CSP 900RMM 2 MD Helicopters Inc Rotorcraft Maintenance Manual FUEL SYSTEM Chapter ...
Page 712: ......
Page 721: ...CSP 900RMM 2 MD Helicopters Inc Rotorcraft Maintenance Manual Section 28 00 00 Fuel System ...
Page 722: ......
Page 846: ......
Page 878: ......
Page 887: ...CSP 900RMM 2 MD Helicopters Inc Rotorcraft Maintenance Manual HYDRAULIC SYSTEM Chapter ...
Page 888: ......
Page 892: ......
Page 925: ...CSP 900RMM 2 MD Helicopters Inc Rotorcraft Maintenance Manual LANDING GEAR Chapter ...
Page 926: ......
Page 932: ......
Page 980: ......
Page 983: ...CSP 900RMM 2 MD Helicopters Inc Rotorcraft Maintenance Manual DOORS AND WINDOWS Chapter ...
Page 984: ......
Page 992: ......
Page 1048: ......
Page 1049: ...CSP 900RMM 2 MD Helicopters Inc Rotorcraft Maintenance Manual FUSELAGE Chapter ...
Page 1050: ......
Page 1063: ...CSP 900RMM 2 MD Helicopters Inc Rotorcraft Maintenance Manual Section 53 00 00 Fuselage ...
Page 1064: ......
Page 1072: ......
Page 1078: ......
Page 1096: ......
Page 1134: ......
Page 1204: ......
Page 1205: ...CSP 900RMM 2 MD Helicopters Inc Rotorcraft Maintenance Manual Section 53 40 00 Tailboom ...
Page 1206: ......
Page 1235: ...CSP 900RMM 2 MD Helicopters Inc Rotorcraft Maintenance Manual Section 53 55 00 Empennage ...
Page 1236: ......
Page 1259: ...CSP 900RMM 2 MD Helicopters Inc Rotorcraft Maintenance Manual Chapter MAIN ROTOR ...
Page 1260: ......
Page 1272: ......
Page 1282: ......
Page 1330: ......
Page 1390: ......
Page 1440: ......
Page 1452: ......
Page 1462: ......
Page 1474: ......
Page 1503: ...CSP 900RMM 2 MD Helicopters Inc Rotorcraft Maintenance Manual Section 63 20 00 Gearboxes ...
Page 1504: ......
Page 1558: ......
Page 1579: ...CSP 900RMM 2 MD Helicopters Inc Rotorcraft Maintenance Manual Section 63 22 00 Rotor Brake ...
Page 1580: ......
Page 1598: ......
Page 1600: ......
Page 1612: ......
Page 1619: ...CSP 900RMM 2 MD Helicopters Inc Rotorcraft Maintenance Manual ANTI TORQUE ASSEMBLY Chapter ...
Page 1620: ......
Page 1626: ......
Page 1648: ......
Page 1672: ......
Page 1678: ......
Page 1685: ...CSP 900RMM 2 MD Helicopters Inc Rotorcraft Maintenance Manual FLIGHT CONTROLS Chapter ...
Page 1686: ......
Page 1706: ......
Page 1732: ......
Page 1828: ......
Page 1834: ......
Page 1842: ......
Page 1927: ...CSP 900RMM 2 MD Helicopters Inc Rotorcraft Maintenance Manual POWERPLANT Chapter ...
Page 1928: ......
Page 1935: ...CSP 900RMM 2 MD Helicopters Inc Rotorcraft Maintenance Manual Section 71 00 00 Powerplant ...
Page 1936: ......
Page 1958: ......
Page 1985: ...CSP 900RMM 2 MD Helicopters Inc Rotorcraft Maintenance Manual Section 71 20 00 Engine Mounts ...
Page 1986: ......
Page 1988: ......
Page 1994: ......
Page 2001: ...CSP 900RMM 2 MD Helicopters Inc Rotorcraft Maintenance Manual Section 71 60 00 Air Intake ...
Page 2002: ......
Page 2012: ......
Page 2033: ...CSP 900RMM 2 MD Helicopters Inc Rotorcraft Maintenance Manual Section 71 70 00 Engine Drains ...
Page 2034: ......
Page 2042: ......
Page 2043: ...CSP 900RMM 2 MD Helicopters Inc Rotorcraft Maintenance Manual ENGINE BLEED AIR Chapter ...
Page 2044: ......
Page 2048: ......
Page 2053: ...CSP 900RMM 2 MD Helicopters Inc Rotorcraft Maintenance Manual ENGINE CONTROLS Chapter ...
Page 2054: ......
Page 2058: ......
Page 2105: ...CSP 900RMM 2 MD Helicopters Inc Rotorcraft Maintenance Manual ENGINE EXHAUST Chapter ...
Page 2106: ......
Page 2109: ...CSP 900RMM 2 MD Helicopters Inc Rotorcraft Maintenance Manual Section 78 00 00 Engine Exhaust ...
Page 2110: ......
Page 2116: ......
Page 2120: ......
Page 2121: ...CSP 900RMM 2 MD Helicopters Inc Rotorcraft Maintenance Manual ENGINE OIL Chapter ...
Page 2122: ......
Page 2125: ...CSP 900RMM 2 MD Helicopters Inc Rotorcraft Maintenance Manual Section 79 00 00 Engine Oil ...
Page 2126: ......