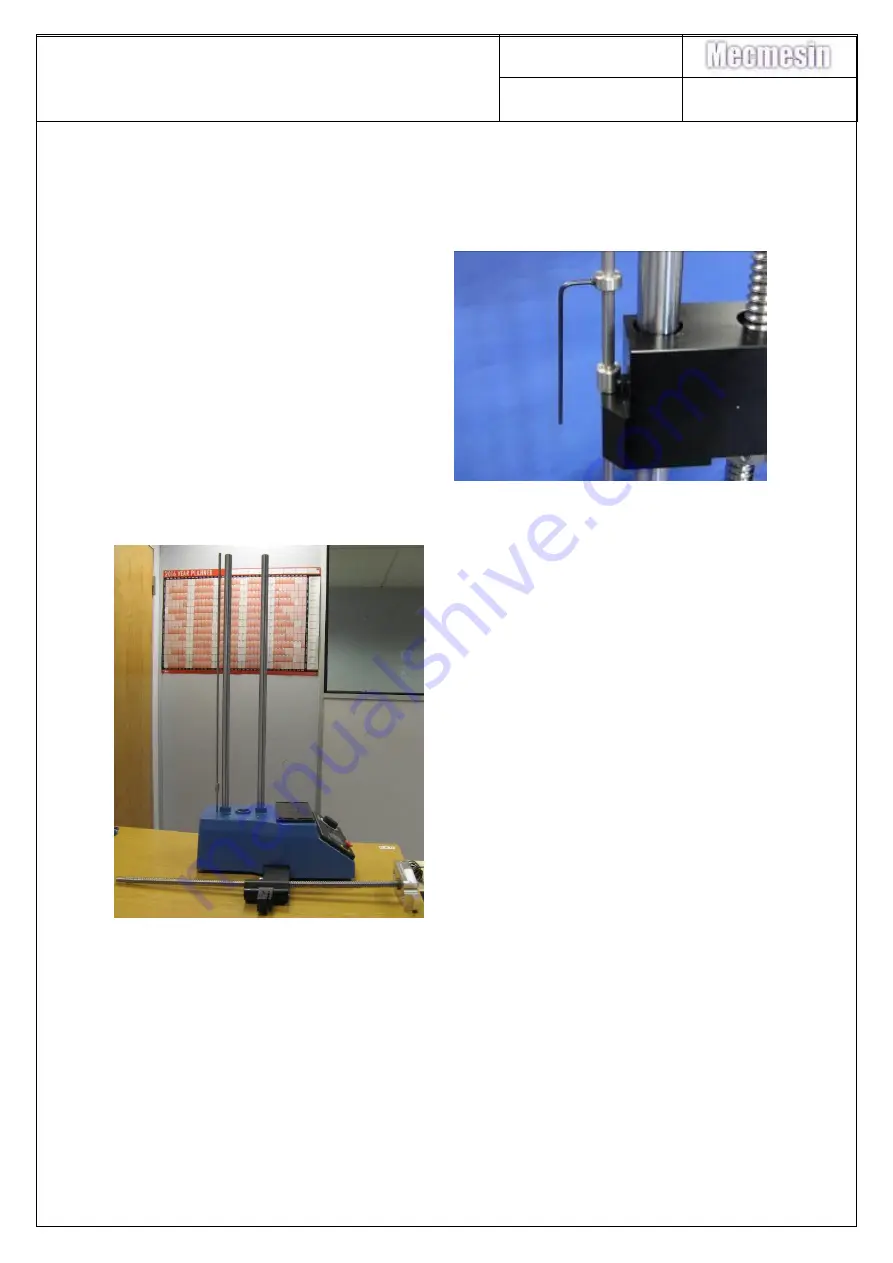
Multitest 0.5dV, 1dV & 2.5dV
Service and Repair Manual
Number 022-780
Issue Number: 02
Page 19 of 32
14. Ballscrew, Top and Moving Crosshead Assembly Replacement
67.
Remove the shroud as per Section 12.
68.
Slacken fixed top collet on
Microswitch rod (note the relative
positions of the fixed collet)
69.
Remove the top crosshead as per Section 13.
70.
Lift top crosshead/moving
5crosshead/ballscrew as a
complete assembly off the columns
taking care not to lose the limit
switch collets that will come off as
the crosshead is removed
Refitting of the Ballscrew assembly is the reverse of the above procedure