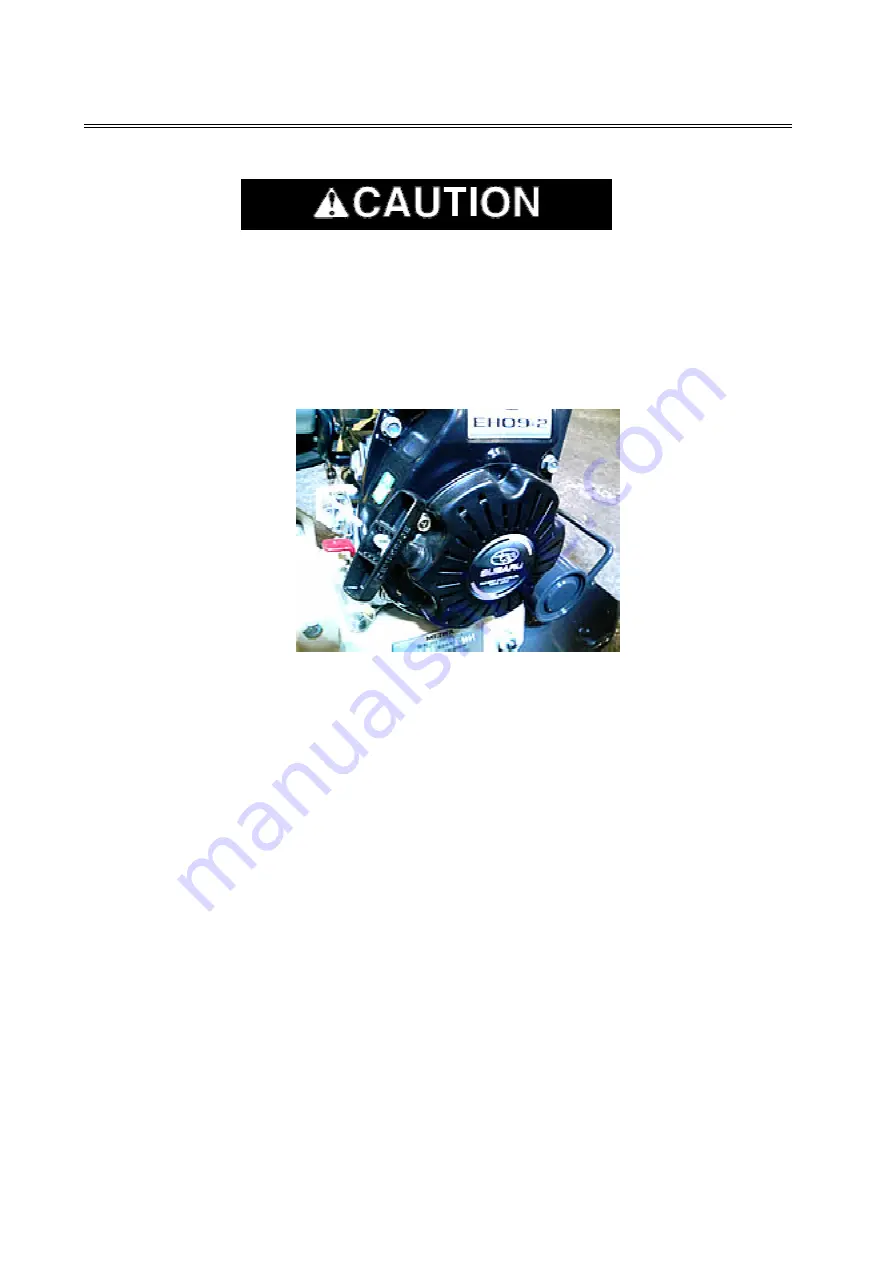
SECTION 4 - OPERATING INSTRUCTIONS
4. Position THROTTLE LEVER (Figure 4-5) to
“
LOW
”
speed position.
Avoid fully pulling out the rope. Return the Handle to its original position.
5.Pull the STARTER HANDLE (1, Figure 4-4) of RECOIL STARTER slowly until resistance is felt. This is the
“
COMPRESSION
”
point. Return the Handle to its original position and pull swiftly. After starting the engine, allow the Starter Handle to return
to its original position while still holding the Handle.
Figure 4-4
After the engine starts, set the Throttle Lever (Figure 4-5) at the low speed position
“
LOW
”
and warm it up without load for a few
minutes. Fully open CHOKE LEVER (1, Figure 4-3) gradually.
4-4