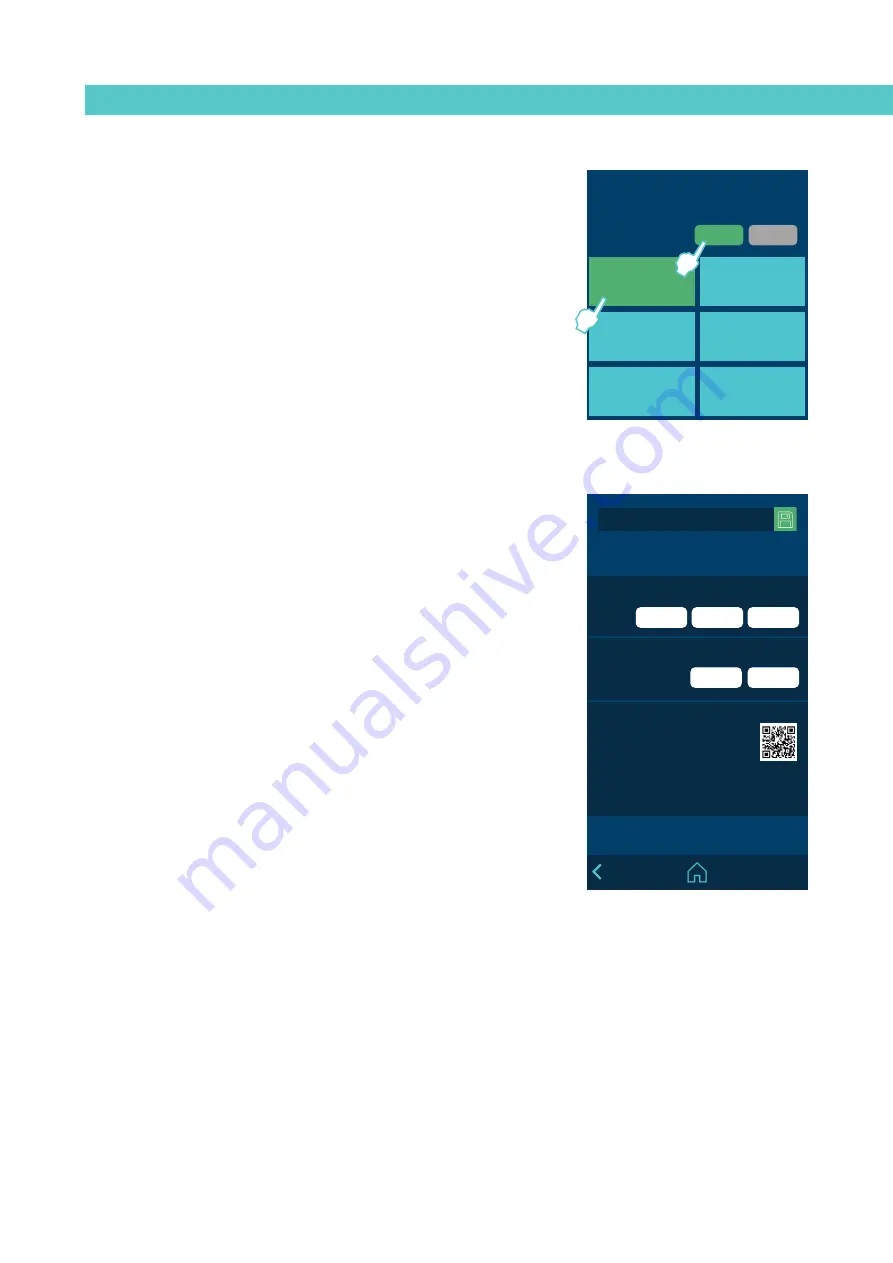
MA-5162-ENG
PISTON ADHESIVE MELTER
MELTER OPERATION
4-11
PISTÓN
HMI
: S02001101 v1.1.2
TC
: S02200100 v1.0.84
IO FM : XXXXXXXXX vx.x.x
English
Español
Français
Deutsch
Portugues
Italiano
Česky
Polski
Nederlandse
°F
°C
Units and Language
Unit:
English
Units and Lenguage Menu
• Units:
To select whether the temperatures are displayed in °C/°F.
•
Language configuration:
Press the desired language.
PISTÓN
HMI
: S02001101 v1.1.2
TC
: S02200100 v1.0.84
IO FM : XXXXXXXXX vx.x.x
01
19
2021
17
19
2021-01-19
17:19
HMI
: S02001101 v1.1.2
TC
: S02200100 v1.0.84
Date & Time
Date
Time
HH
MM
MM
DD
YYYY
Software version
Sensor technology: PT100
Scan the code to download the user manual
Date and time configuration
This screen allows you to view and modify the date and time data of the
system.
It also shows:
• The equipment software version.
• A QR code, to be able to download the user manual.
• The type of technology of the installed sensors.
Summary of Contents for Micron + 10
Page 10: ...FOCKE MELER GLUING SOLUTIONS TABLE OF CONTENTS This page is intentionally left blank ...
Page 38: ...FOCKE MELER GLUING SOLUTIONS INSTALLATION 3 16 This page is intentionally left blank ...
Page 74: ...FOCKE MELER GLUING SOLUTIONS 4 36 MELTER OPERATION This page is intentionally left blank ...
Page 84: ...FOCKE MELER GLUING SOLUTIONS 5 10 MAINTENANCE This page is intentionally left blank ...
Page 91: ...MA 5162 ENG MICRON PISTON ADHESIVE MELTER ELECTRICAL DRAWINGS 7 1 7 ELECTRICAL DRAWINGS ...
Page 92: ...FOCKE MELER GLUING SOLUTIONS 7 2 ELECTRICAL DRAWINGS This page is intentionally left blank ...
Page 102: ...FOCKE MELER GLUING SOLUTIONS 8 10 PNEUMATIC DIAGRAM This page is intentionally left blank ...
Page 104: ...FOCKE MELER GLUING SOLUTIONS 9 2 SPARE PARTS LIST This page is intentionally left blank ...