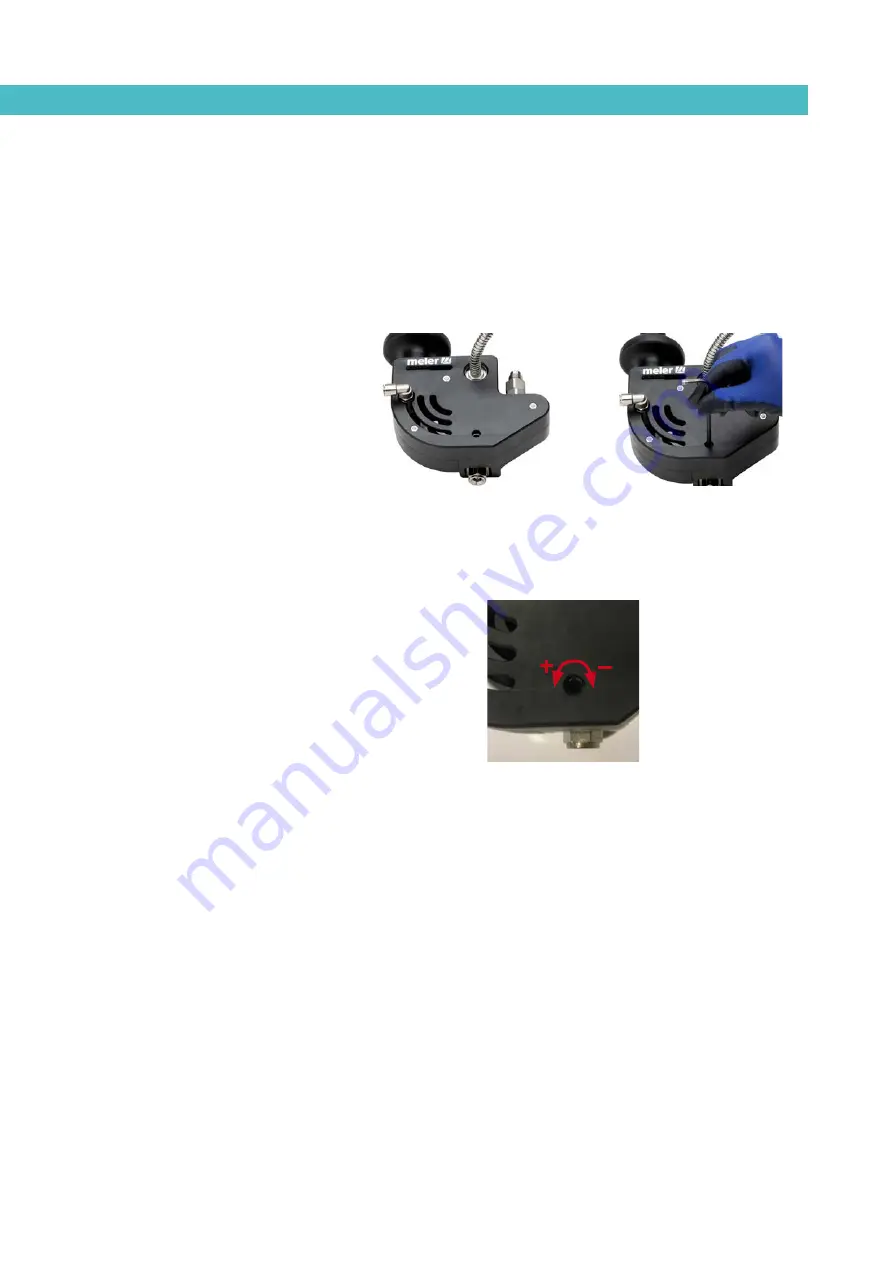
MELER GLUING SOLUTIONS
4-4
USING THE APPLICATOR
Adjusting the air flow (applicator for swirling)
The air flow is adjusted from the applicator itself. Make sure that the
applicator is receiving a pressure of 6 bar.
The applicator is equipped with a mechanical air choke on the applicator body.
None of the side plates have to be removed to handle the air cut-off; all that is
needed is a 4 mm Allen wrench to rotate the choke mechanism.
Turn the screw to the left to increase air flow and to the right to reduce it.
Summary of Contents for MV
Page 1: ...MV APPLICATOR INSTRUCCIONS MANUAL MA 5096 E 020915 GLUING SOLUTIONS ...
Page 8: ...MELER GLUING SOLUTIONS 1 4 SAFETY GUIDELINES This page is intentionally left blank ...
Page 12: ...MELER GLUING SOLUTIONS 2 4 INTRODUCTION This page does not contain any text ...
Page 28: ...MELER GLUING SOLUTIONS 6 6 MAINTENANCE This page does not contain any text ...
Page 32: ...MELER GLUING SOLUTIONS 7 4 SPARE PARTS LIST This page does not contain any text ...