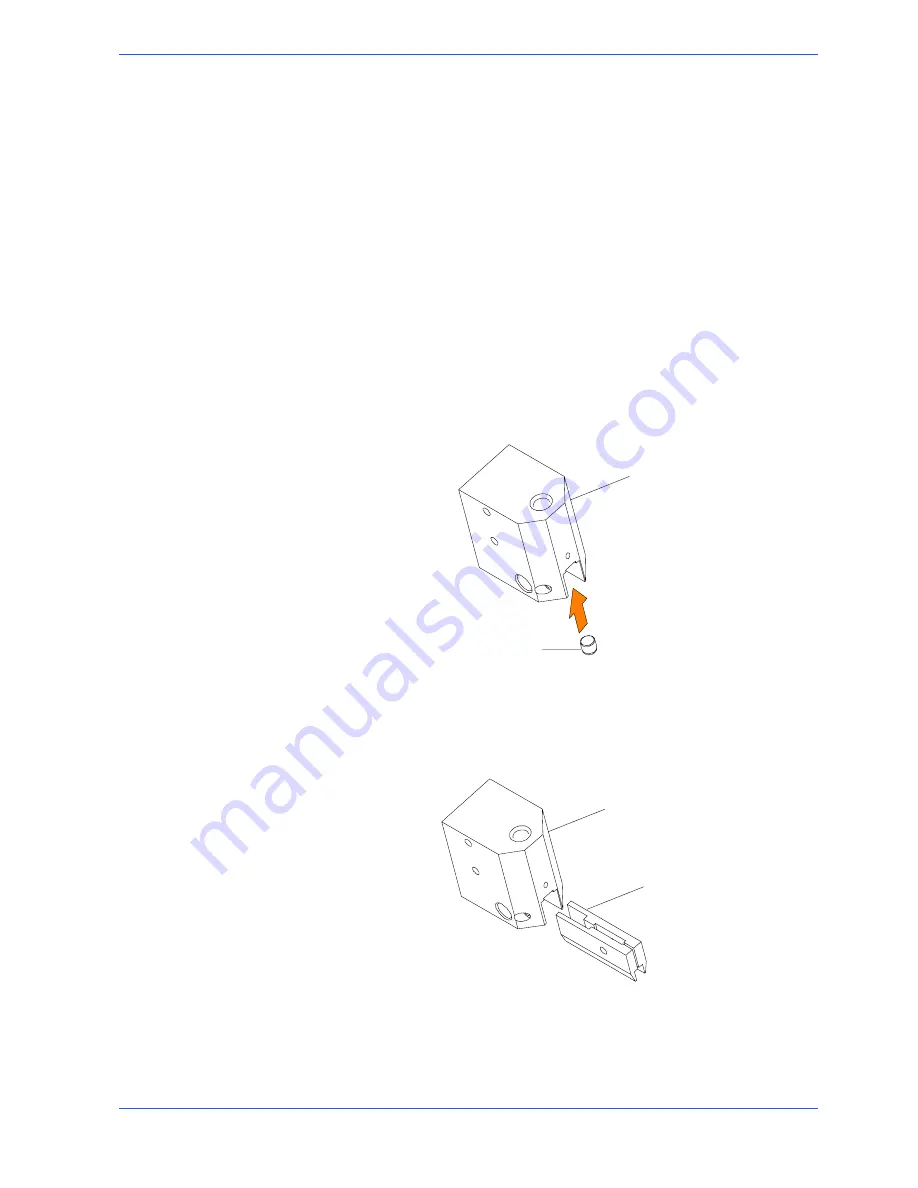
7--9
95
Adjustments
Blade guide parts
Band saw blades offer enormous advantages to cutting applications, without
requiring any special skills by the operator. A description follows of the blade
guide adjustments required to ensure correct operation of the saw.
Blade guide heads
The first blade adjustment involves adjustment of the heads. The blade guide
heads comprise the blade guide plates which ensure correct longitudinal align-
ment, the blade steady buttons which control vertical blade flexure, and the
coolant supply cocks.
Blade steady buttons
The blade steady buttons prevent upward blade flexure caused by the vertical
action of the cutting force. These buttons are fitted on both the front and rear
heads, and need no adjustment.
Blade steady button
Blade guide head
Blade guide plates
The plate contact points feature widia inserts which guide the blade longitudin-
ally. A small amount of play must exist between the plates and blade to ensure
that the blade runs smoothly and perpendicular to the work table.
Blade guide head
Blade guide plates
Thanks to the widia inserts, the working life of the guide plates is practically the
same as that of the machine itself. However, if due to wear or the assembly of a
new blade with a different thickness, the amount of play between the plates and
blade changes, the plates must be adjusted as follows:
"
disconnect the machine from the power supply;
Summary of Contents for SHARK 282
Page 1: ...USE AND MAINTENANCE MANUAL YEAR OF MANUFACTURE ______________ SHARK 282 EN...
Page 2: ......
Page 4: ......
Page 8: ......
Page 59: ...6 7 51 Diagrams exploded views and replace Standardised Wiring Diagrams CENELEC Standard...
Page 60: ...MEP S p A 6 8 52 Use and maintenance manual SHARK 282...
Page 61: ...6 9 53 Diagrams exploded views and replace...
Page 62: ...MEP S p A 6 10 54 Use and maintenance manual SHARK 282...
Page 63: ...6 11 55 Diagrams exploded views and replace...
Page 64: ...MEP S p A 6 12 56 Use and maintenance manual SHARK 282...
Page 65: ...6 13 57 Diagrams exploded views and replace...
Page 66: ...MEP S p A 6 14 58 Use and maintenance manual SHARK 282...
Page 67: ...6 15 59 Diagrams exploded views and replace...
Page 68: ...MEP S p A 6 16 60 Use and maintenance manual SHARK 282...
Page 69: ...6 17 61 Diagrams exploded views and replace...
Page 70: ...MEP S p A 6 18 62 Use and maintenance manual SHARK 282...
Page 71: ...6 19 63 Diagrams exploded views and replace...
Page 72: ...MEP S p A 6 20 64 Use and maintenance manual SHARK 282...
Page 73: ......
Page 76: ...MEP S p A 6 24 67 Use and maintenance manual SHARK 282 Front flywheel assembly 282...
Page 78: ...MEP S p A 6 26 69 Use and maintenance manual SHARK 282 Motor flywheel assembly 282...
Page 80: ...MEP S p A 6 28 71 Use and maintenance manual SHARK 282 Cutting head cover 282...
Page 82: ...MEP S p A 6 30 73 Use and maintenance manual SHARK 282 Vice assembly 282...
Page 84: ...MEP S p A 6 32 75 Use and maintenance manual SHARK 282 Base assembly 282...
Page 86: ...MEP S p A 6 34 77 Use and maintenance manual SHARK 282 Control panel...
Page 88: ...MEP S p A 6 36 79 Use and maintenance manual SHARK 282 Handgrip 3OUT3 SHARK 282...
Page 90: ...MEP S p A 6 38 81 Use and maintenance manual SHARK 282 Fixed work table and turntable 282...
Page 92: ...MEP S p A 6 40 83 Use and maintenance manual SHARK 282 Optional Cut Control System...
Page 94: ...MEP S p A 6 42 85 Use and maintenance manual SHARK 282 Supplementary pneumatic vice 282...
Page 96: ......
Page 151: ......
Page 152: ......