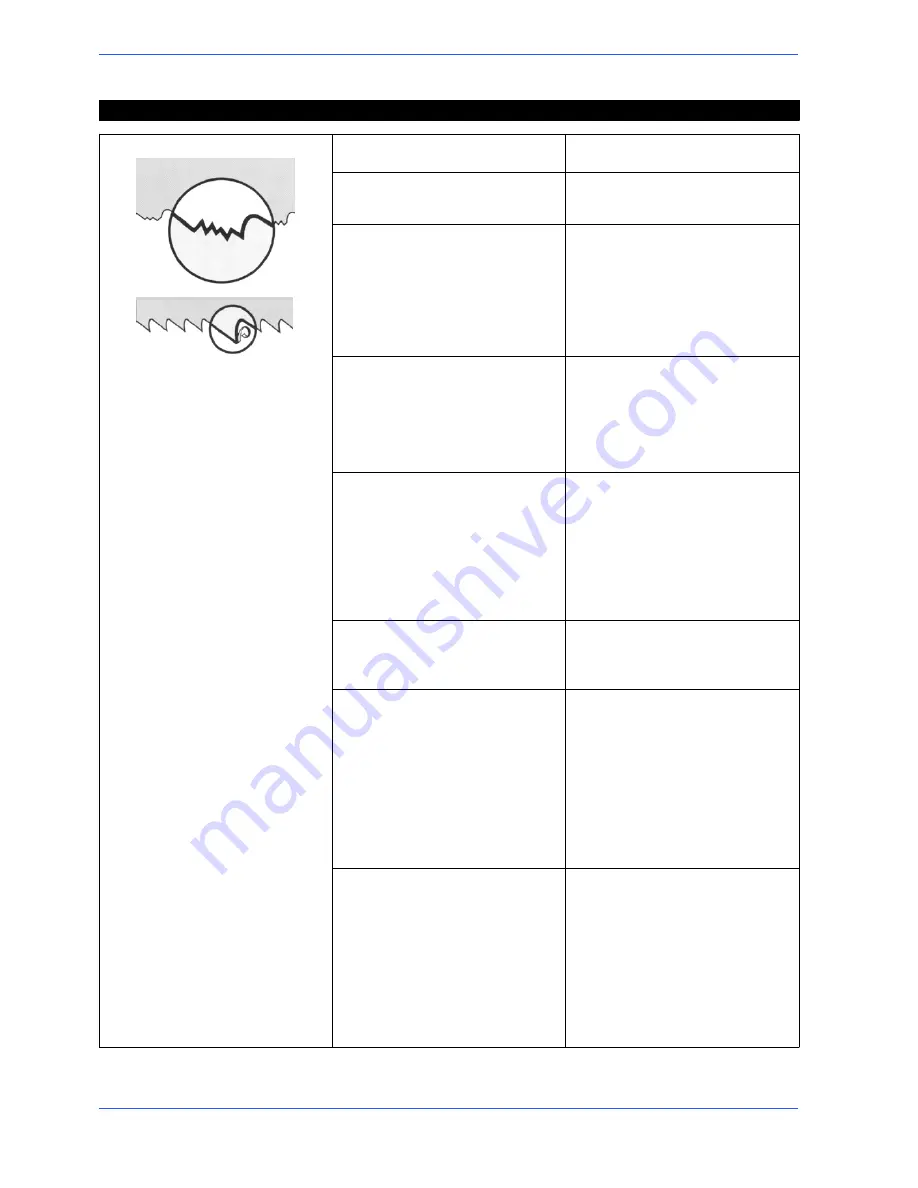
MEP S.p.A.
10--4
126
Use and maintenance manual
SHARK 282
SOLUTION
PROBABLE CAUSE
PROBLEM
Broken teeth
'
Cutting pressure too high
.
Check and set to correct
pressure
'
Tooth pitch unsuitable
.
Teeth too close together:
change blade for one with a
coarser tooth pitch
'
Swarf welded to teeth and
gullets
.
Check blade--cleaning
coolant jets. Check the
blade--cleaning brush. If the
swarf is not removed from
the blade it will be drawn
back into the cut and weld to
the teeth, causing tooth
breakage
'
Swarf welded to teeth and
gullets
.
Check blade--cleaning fluid
jets. Check blade--cleaning
brush. If the swarf is not
removed from the blade it will
be drawn back into the cut
and weld to the teeth,
causing the teeth to break.
'
Material defects
.
The material may have
altered surface areas, such
as oxides or sand, or
subcooled inclusions in the
section. These areas are
much harder than the blade
and will cause the teeth to
break: scrap or clean these
materials.
'
Workpiece not clamped
.
The blade may break if the
workpiece moves during
cutting: check the vice, jaws
and clamping pressure
'
The blade stops in the cut
.
Cutting pressure too high:
check and restore to rated
pressure. Downstroke speed
too fast: reduce speed.
Cutting speed too slow:
increase. The blade slips on
the flywheels: either the
wheels are worn and need to
be replaced or the blade
tension is incorrect (too low)
and must be re--adjusted.
'
New blade inserted in a
partially made cut
.
The cutting surface may
have been subjected to a
localised heat--induced
alteration, making it harder:
recommence cut using a
slower cutting and
downstroke speed. A tooth
from the old blade may be
left in the cut: check and
remove before restarting
work.
Summary of Contents for SHARK 282
Page 1: ...USE AND MAINTENANCE MANUAL YEAR OF MANUFACTURE ______________ SHARK 282 EN...
Page 2: ......
Page 4: ......
Page 8: ......
Page 59: ...6 7 51 Diagrams exploded views and replace Standardised Wiring Diagrams CENELEC Standard...
Page 60: ...MEP S p A 6 8 52 Use and maintenance manual SHARK 282...
Page 61: ...6 9 53 Diagrams exploded views and replace...
Page 62: ...MEP S p A 6 10 54 Use and maintenance manual SHARK 282...
Page 63: ...6 11 55 Diagrams exploded views and replace...
Page 64: ...MEP S p A 6 12 56 Use and maintenance manual SHARK 282...
Page 65: ...6 13 57 Diagrams exploded views and replace...
Page 66: ...MEP S p A 6 14 58 Use and maintenance manual SHARK 282...
Page 67: ...6 15 59 Diagrams exploded views and replace...
Page 68: ...MEP S p A 6 16 60 Use and maintenance manual SHARK 282...
Page 69: ...6 17 61 Diagrams exploded views and replace...
Page 70: ...MEP S p A 6 18 62 Use and maintenance manual SHARK 282...
Page 71: ...6 19 63 Diagrams exploded views and replace...
Page 72: ...MEP S p A 6 20 64 Use and maintenance manual SHARK 282...
Page 73: ......
Page 76: ...MEP S p A 6 24 67 Use and maintenance manual SHARK 282 Front flywheel assembly 282...
Page 78: ...MEP S p A 6 26 69 Use and maintenance manual SHARK 282 Motor flywheel assembly 282...
Page 80: ...MEP S p A 6 28 71 Use and maintenance manual SHARK 282 Cutting head cover 282...
Page 82: ...MEP S p A 6 30 73 Use and maintenance manual SHARK 282 Vice assembly 282...
Page 84: ...MEP S p A 6 32 75 Use and maintenance manual SHARK 282 Base assembly 282...
Page 86: ...MEP S p A 6 34 77 Use and maintenance manual SHARK 282 Control panel...
Page 88: ...MEP S p A 6 36 79 Use and maintenance manual SHARK 282 Handgrip 3OUT3 SHARK 282...
Page 90: ...MEP S p A 6 38 81 Use and maintenance manual SHARK 282 Fixed work table and turntable 282...
Page 92: ...MEP S p A 6 40 83 Use and maintenance manual SHARK 282 Optional Cut Control System...
Page 94: ...MEP S p A 6 42 85 Use and maintenance manual SHARK 282 Supplementary pneumatic vice 282...
Page 96: ......
Page 151: ......
Page 152: ......