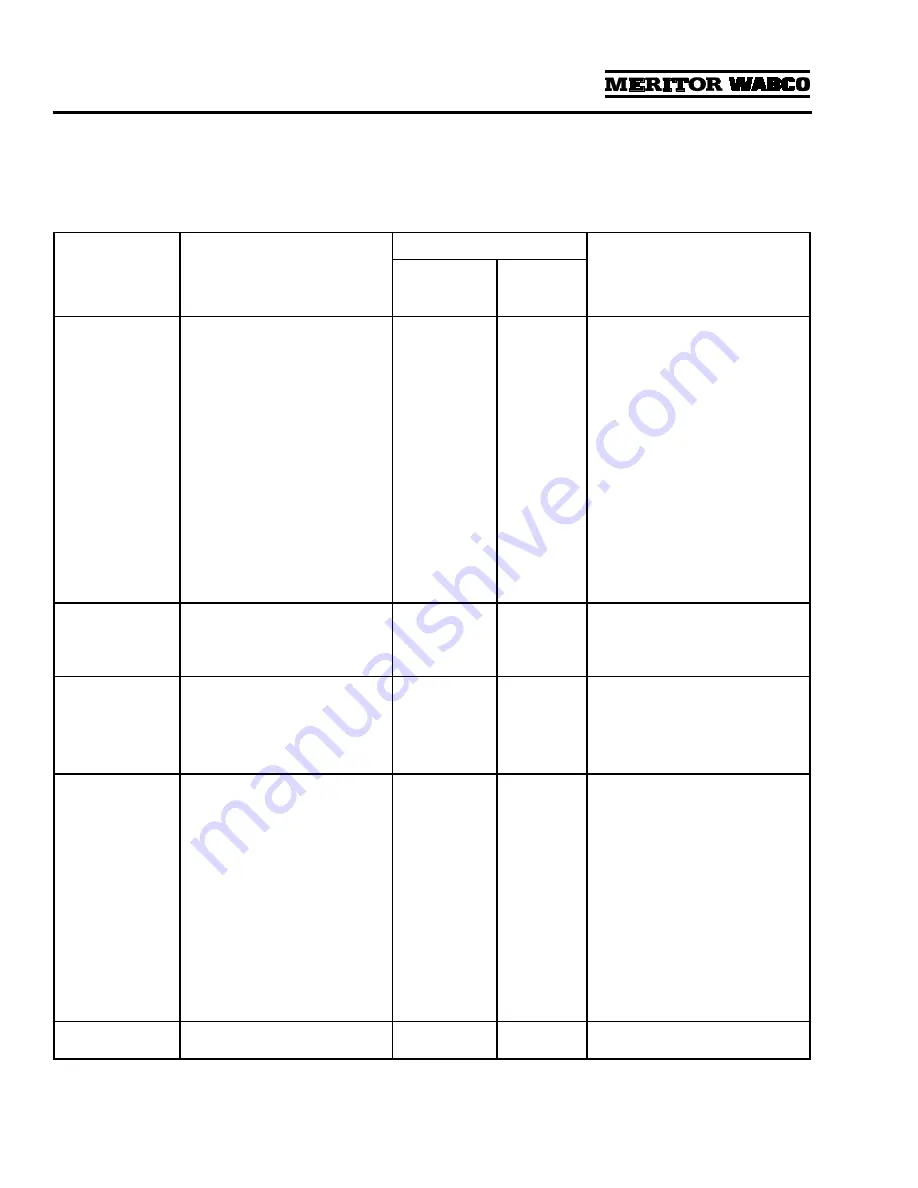
Section 2
Troubleshooting & Testing
MM-34
Page 10
Revised 11-02
Troubleshooting
Conditions you may experience, and suggested
solutions, appear in the following System Saver
Series Air Dryer Troubleshooting table.
NOTE:
The exploded view of the System Saver
single canister air dryer in Section 1 illustrates the
location of components in the dryer.
Condition
Possible Cause
Conditions May Occur In:
Solution
Regeneration
Style Air
Dryers
Dedicated
Purge Tank
Air Dryers
Dryer leaks from
purge valve during
compressor
loaded cycle. The
leak may cause
excessive
compressor
cycling or prevent
the system from
building air
pressure.
Purge valve frozen open (cold
weather operation).
Debris under purge valve seat,
such as particles from fittings or
air inlet line.
Purge valve washer installed
upside-down.
Wrong air line connected to dryer
port 4 (unloader port).
Purge valve snap ring not fully
seated in groove.
Yes
Yes
Check heater. Repair/replace if
necessary. Make sure governor to
dryer port 4 line is free of water/oil.
Remove and inspect purge valve
and clean water/oil from top of
piston.
Disassemble and clean purge valve.
Remove cartridge and clean dryer
sump area.
Ensure lip on aluminum washer
faces
DOWN
, away from dryer.
Verify correct air line installation
and correct as needed.
Seat snap ring fully into groove.
Slight leak from
purge valve. After
several hours, the
supply tank may
be empty.
Outlet check valve not seating or
regeneration valve not shutting
off regeneration airflow.
Yes
No
Remove, inspect, and clean outlet
check valve and regeneration valve
diaphragm. Replace if worn or
damaged.
Regeneration
cycle too long
(more than
30 seconds),
accompanied by
loss of pressure in
the supply tank.
Outlet check valve not seating.
Regeneration valve not shutting
off regeneration airflow.
Yes
Yes
Yes
No
Inspect and replace outlet check
valve as needed.
Replace regeneration valve.
Regeneration
cycle too short
(less than
10 seconds).
High air system demands during
compressor unloaded cycle.
Pressure-controlled check valve
not installed in system or not
working properly.
One-way check valve installed in
system reservoir instead of, or
with, pressure-controlled check
valve.
Regeneration valve not working.
Air governor not working
properly.
Yes
Yes
Yes
Yes
Yes
Yes
No
No
No
Yes
Increase air system capacity or
reduce air demands.
Check and replace pressure-
controlled check valve as needed.
Remove one-way check valve. Make
sure pressure-controlled check
valve is installed correctly.
Remove regeneration valve and
clean oil from diaphragm. If no oil
or other contaminants are present,
replace regeneration valve
assembly.
Inspect per manufacturer’s
instructions and repair/replace as
needed.
Water in purge
tank
Block in purge tank line.
N/A
Yes
Clear blockage. Replace desiccant
cartridge.