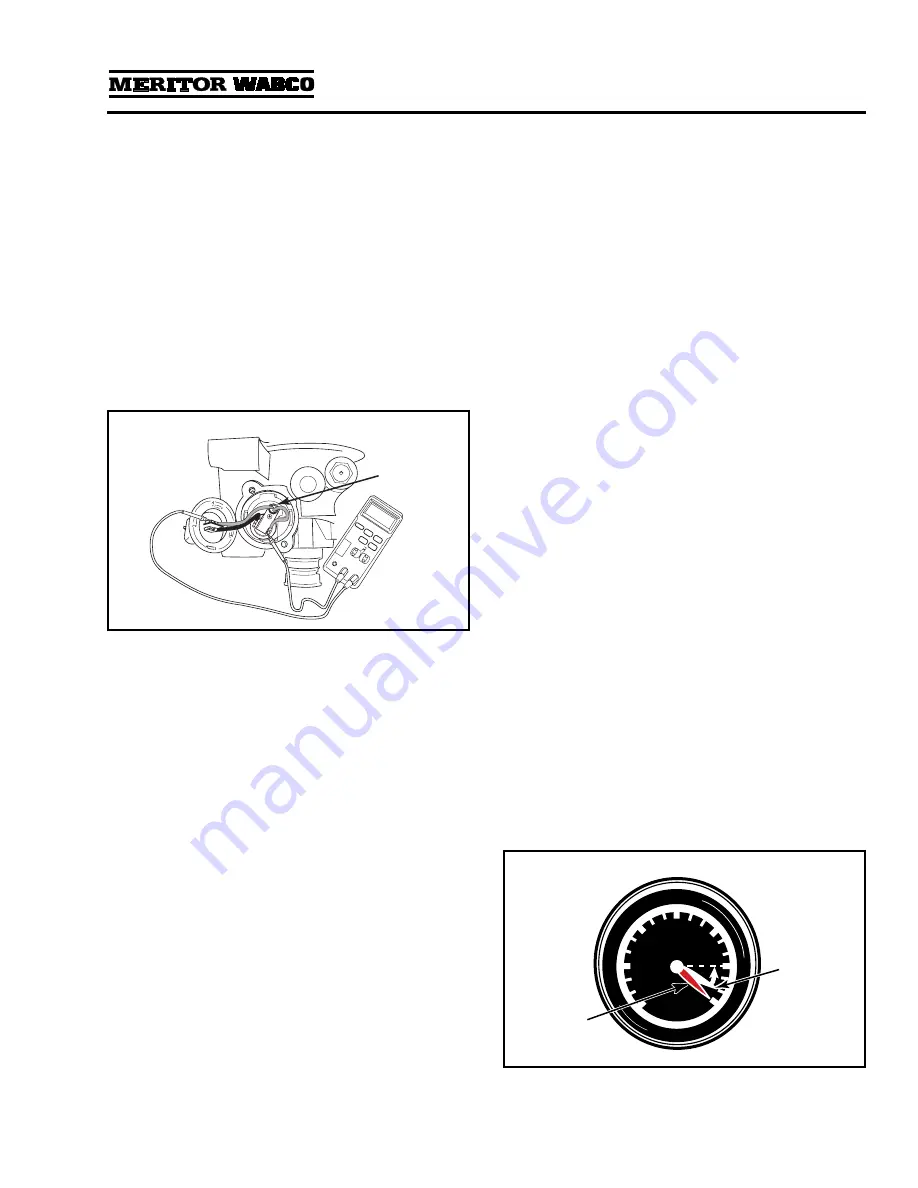
MM-34
Revised 11-02
Page 13
System Tests
Heater Resistance
To avoid damaging components, Meritor WABCO
recommends performing this resistance check
with the heater in place.
1.
Set volt-ohmmeter to ohms.
2.
Disconnect vehicle harness at the heater.
3.
Remove the two screws holding the external
components in place.
4.
With wires connected and properly secured,
touch one probe to each heater element lead.
5.
Measure the resistance. Acceptable resistance
is:
O
12 Volt: 1.0-2.0 ohms
O
24 Volt: 5.0-7.0 ohms
If resistance is less than 1.0 ohm for a 12-volt
or 5.0 ohms for a 24-volt system, replace the
heater.
6.
Reinstall components and vehicle harness.
Leak Test
1.
Drain air from all system tanks.
2.
Close reservoir draincocks.
3.
Start the vehicle. Allow air system pressure to
build while engine idles.
4.
When the system reaches cut-out pressure
there will be a purge, or strong blast of air,
followed by a mild flow which will last
10-25 seconds.
5.
Shut off the engine.
6.
Apply a soap solution to each connection that
contains pressurized air. Check the
connections to see if soap solution bubbles.
No Soap Bubbles:
Connections are sealed
properly.
Soap Bubbles Appear:
Connections are NOT
sealed properly.
To repair improperly sealed connections:
1.
Drain all reservoirs.
2.
Remove leaking connection.
3.
Inspect the connectors and ports for damaged
threads or cracks. Replace if necessary.
4.
Apply pipe sealant to the connection.
NOTE:
Repeat leak test until all connections are
sealed.
Air Pressure Checks
NOTE:
When checking air pressure during these
tests, do not rely on cab air gauges for accurate
readings. Install a calibrated air gauge (accurate to
within 1 psi) in the secondary air tank for making
determinations about the continued use or
replacement of equipment.
Operational Test for System Saver
Series Air Dryers — Regeneration
and Purge Style
1.
Check compressor loaded and unloaded cycle.
When the compressor is in the
loaded cycle
,
air pressure will build to approximately 120 psi
(cut-out pressure). When the compressor
reaches the
unloaded cycle
, the air dryer will
purge, initiating regeneration of the air dryer.
Figure 2.2
HEATER
Figure 2.3
PSI
20
40
60
80
100
110
120
1002161a
Primary
Air Supply
(Red)
Secondary
Air Supply
(White)