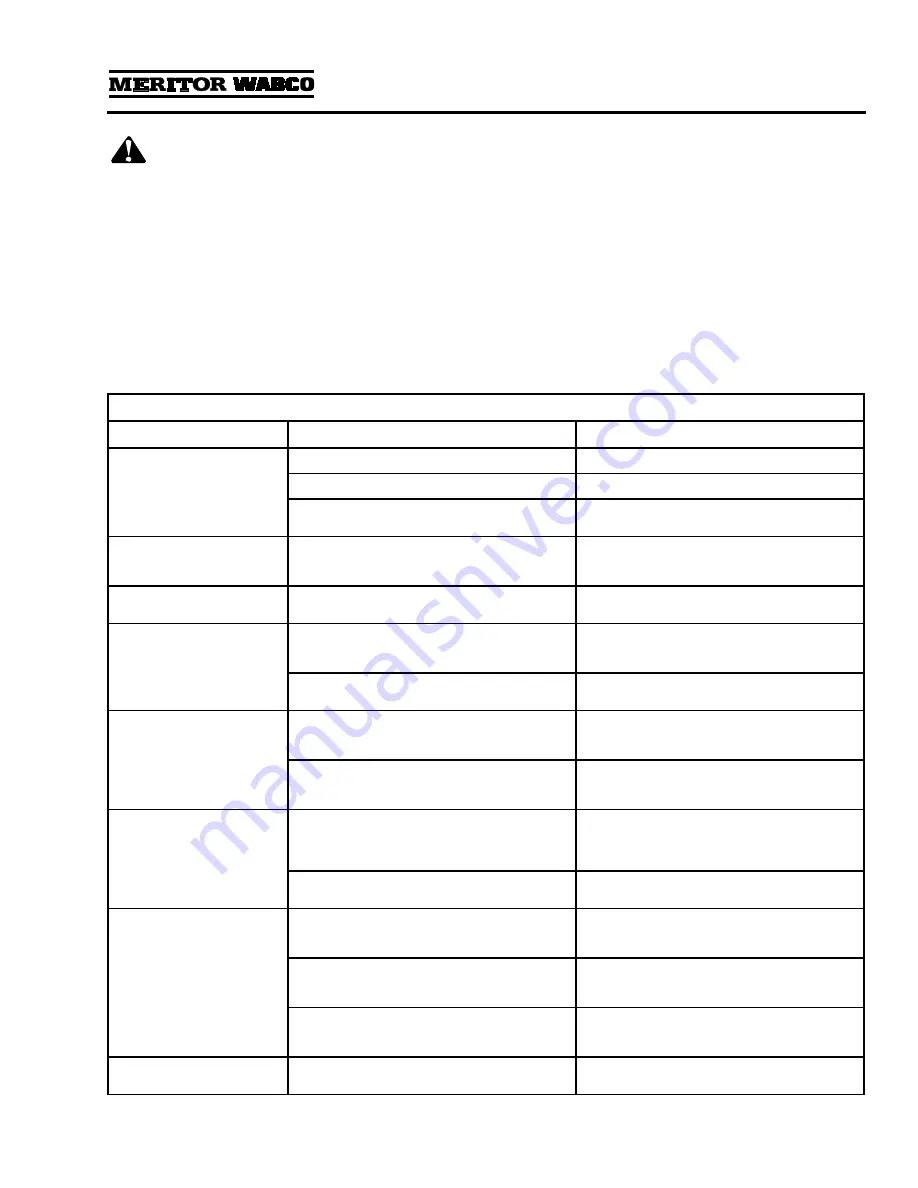
MM-34
Revised 11-02
Page 15
Section 3
Installing Replacement Parts
WARNING
To prevent serious eye injury, always wear safe
eye protection when you perform vehicle
maintenance or service.
Remove all pressure from the air system before
you disconnect any component, including the
desiccant cartridge. Pressurized air can cause
serious personal injury.
Park the vehicle on a level surface. Block the
wheels to prevent the vehicle from moving.
Serious personal injury can result.
Replacement Requirements
Before replacing any air dryer component, make
sure the air compressor and air governor are
working properly. Repair or replace these parts, if
necessary. Check the entire air system for leaks,
and repair as necessary. When draining air tanks
before servicing the air dryer, check for water
and/or oil that may have accumulated in the tanks.
Water and/or oil in the air tanks could indicate a
problem with the dryer or compressor.
Replacement Requirements
Component
When to Replace
Why
Desiccant Cartridge
Every two to three years.
Preventative maintenance.
When compressor is replaced.
Contaminated cartridge.
Water in supply tank.
Saturated or contaminated cartridge, high duty
cycle (wrong application of air dryer).
Bypass Valve (dryers with
date codes earlier than
0894)
Valve leaking, inlet to outlet.
Cut O-ring, bad seat.
Heater Assembly
Water collecting in air dryer is freezing —
electrical power to dryer is O.K.
Heater assembly not working (internal short or
open circuit).
Outlet Check Valve
Air continues to flow from purge valve after
purge cycle, but stops flowing when the
compressor load cycle begins.
Valve is stuck in the open position, or not
functioning properly.
No pressure build-up in system, everything
else is O.K.
Valve is stuck in closed position.
Purge Valve
No purge cycle when compressor unloads —
normal pressure at dryer control port 4
(governor port).
Valve is stuck in the closed position, or not
functioning properly.
Air flows from purge valve during
compressor’s load cycle — no pressure at dryer
control port.
Valve is stuck in the open position, or not
functioning properly.
Turbo Cut-Off Valve
Air flows from purge valve during compressor
unload cycle after purge cycle, and flow is
noticeably stronger at high engine RPM,
especially under load.
Turbo cut-off valve leaking.
No pressure build-up in system — high
compressor discharge line pressure.
Valve stuck in closed position.
Regeneration Valve
Regeneration cycle continues after compressor
begins, and secondary tank pressure drops
15 psi or more.
Regeneration valve allowing too much air to
come back into cartridge.
Purge cycle is too short (5 seconds or less) —
pressure-controlled check valve is O.K., no leak
in governor control line.
Regeneration valve not allowing enough air to
come back into cartridge.
Air dryer purges — but no regeneration, no
check valve between air dryer and supply tank,
and purge valve has not closed.
Regeneration valve not allowing any air to
come back into cartridge.
Pressure-Controlled
Check Valve
Regeneration cycle too short; may result in
water in tank.
Valve checks (stops airflow) too high.