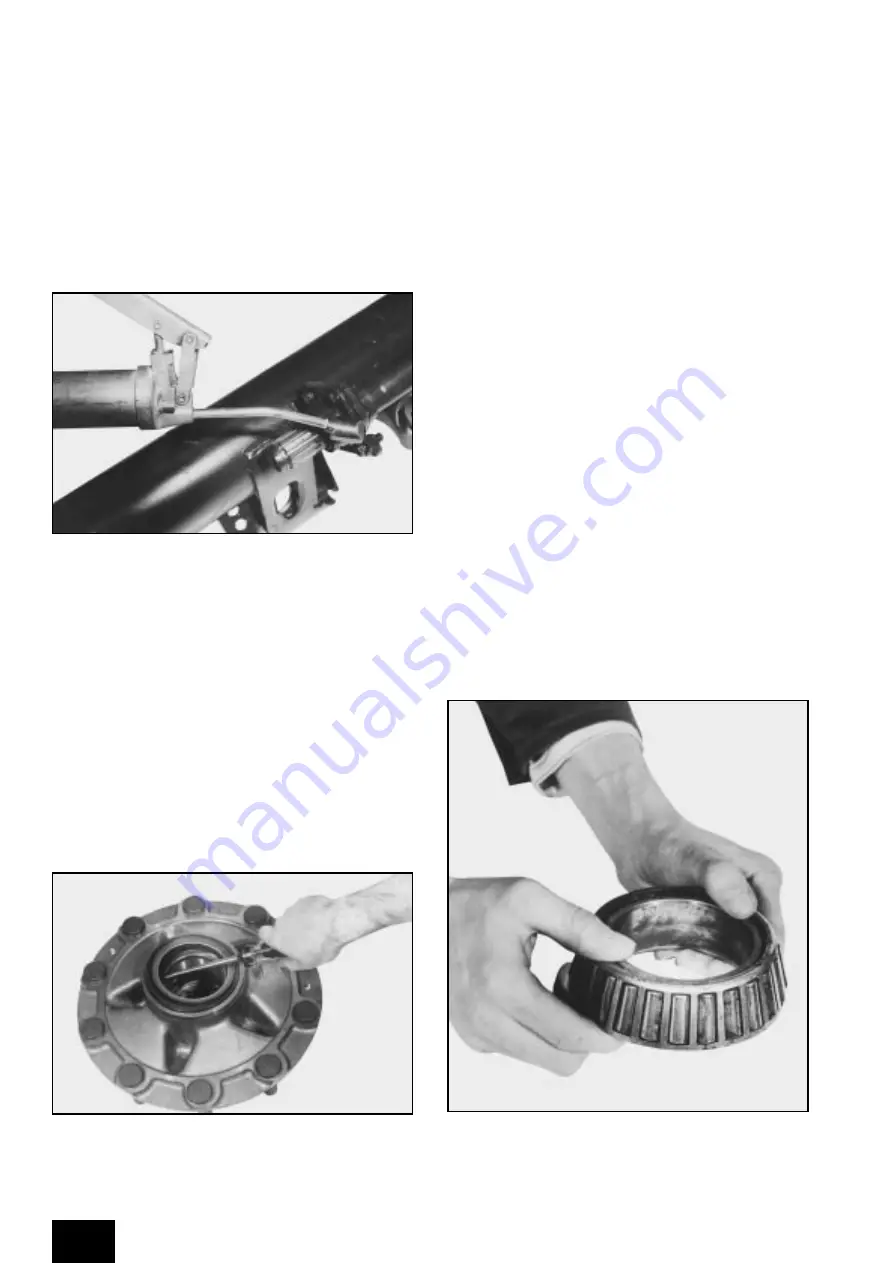
12
TE9000 / 93000 Service
17. GREASE CAMSHAFT BEARINGS
Grease camshaft bearings using grease gun (fig. 14), it is possible to see
the grease extrude from the side plates of the camshaft head bearings
with the hub and drum removed. Ensure the correct specification of
grease is used.
18. INSPECT BRAKE DRUMS
Clean excess brake dust from brake drum and inspect brake drum bore
for surface corrosion, damage and excessive wear.
Remove light corrosion by using coarse emery cloth at an angle of 45
degrees in one direction and then 45 degrees in the other direction to
produce a cross hatch effect, do not use any form of power tool.
If the drum bore shows signs of heat crazing it usually can be reused but
if the heat crazing is severe the drum should be replaced.
It is permissible to machine out the brake drum to a maximum of
Ø423mm. Oversize cam rollers must be fitted if this is done (21006610A).
19. REMOVE OIL SEAL
If the oil seal is still within the hub remove it with a work shop pri-bar and
discard it (fig. 15). Take care not to contaminate the inner bearing and hub
cavity.
If the oil seal has remained on the spindle journal lever it off taking great
care not to damage the spindle. Clean the area around the oil seal journal
as detailed in paragraph 6. Discard the oil seal.
Never reuse an oil seal after the hub has been dismounted from the
spindle.
20. WHEEL BEARING INSPECTION AND
GREASING
Step 20a describes the routine inspection and service.
Step 20b should be carried out every 300,000 km, or every 3 years or if
the grease appears dirty, contaminated or burnt, or if no cavity fill is
present.
Refer to grease type and fill volumes specified on page 6.
20a. ROUTINE ANNUAL HUB SERVICE
INNER BEARING:
If the grease within the hub is clean and does not appear or smell burnt
there should be no requirement to totally clean down the assembly and
re-grease the bearings.
Care must be taken not to contaminate the lubricant during the inspection.
Check the hub cavity and inner bearing for contamination caused when
the hub was dismounted from the spindle. Contamination must be
removed and if necessary a total clean down and re-lubrication as
described in step 20b must be performed.
Remove the inner bearing cone (fig. 16) and check the condition of the
grease.
FIG. 14
FIG. 15
FIG. 16