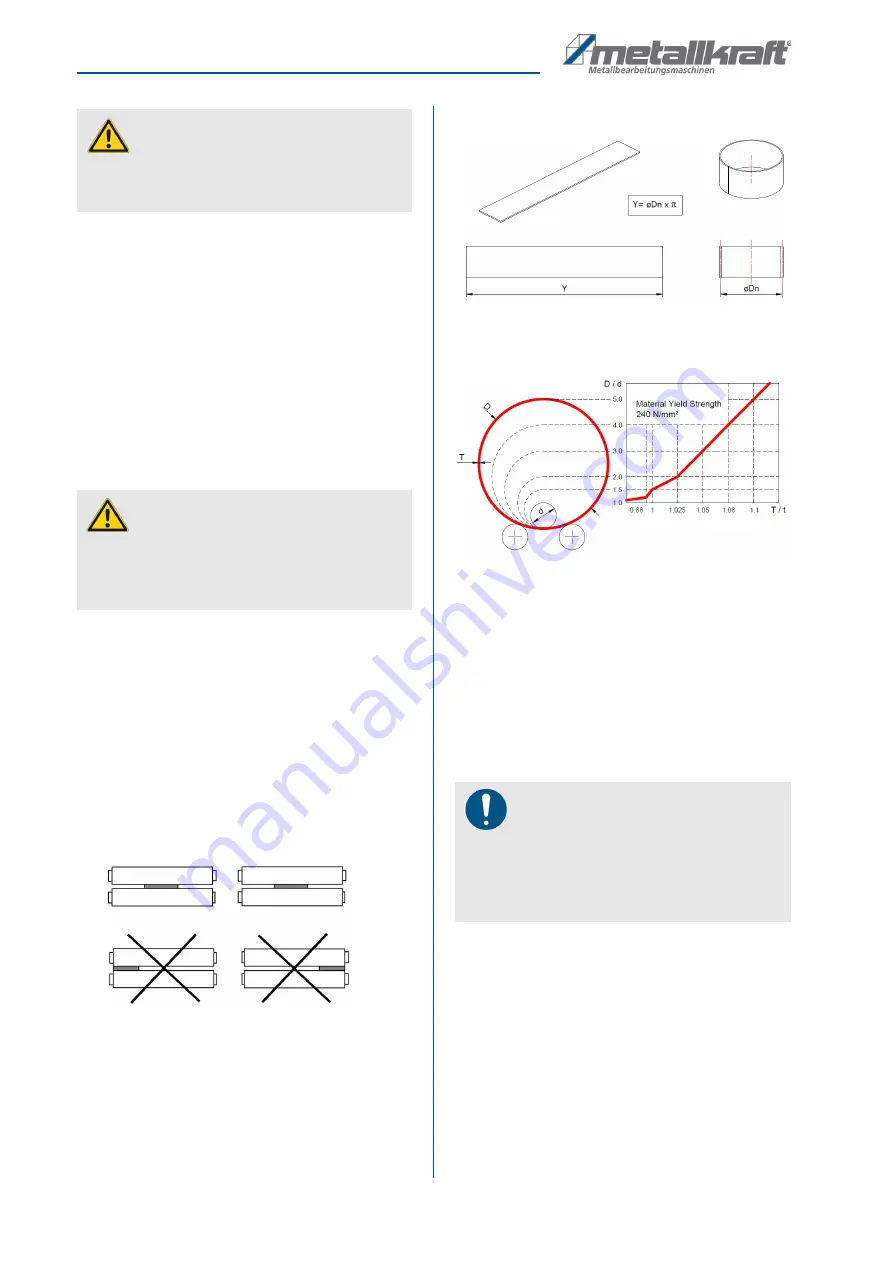
12
RBM 1305-15 E | Version 1.02
Operation
Step 10: Fold in the top roller and lock.
Step 11: Switch off the machine with the main switch.
8.2 Bending process
Bending may only be performed by qualified personnel
experienced in these machines. All steps of bending,
pre-bending and conical bending must be carried out
extremely carefully. It should be noted that a small ra-
dius is made by repeating the bending process several
times; Once too much bent, this step can not be un-
done.
Before processing
- Remove dirt and oil from the material.
- The material ends must be free of chips and burnt
residues.
- Burned material is harder at the points of separa-
tion than in the remaining area.
- The material has to be level.
- It is recommended to make a stencil made of card-
board or cardboard for the desired radius.
Always work the workpiece in the center of the rollers.
Fig. 8: Position the workpiece in the middle of the rollers
Calculation of the workpiece length
Fig. 9: Calculation of the workpiece length
Bending chart
Fig. 10: Bending chart
Pre bending
Pre-bending is the operation whereby the ends of the
material are bent to the same radius as the final radius.
As a result, the best results are achieved at full radii (eg
making tubes) or for operations where no flat ends are
desired.
Bending
ATTENTION!
The unfolded top roller must not be overloaded by
the workpiece. The workpiece must be supported by
a crane.
WARNING!
Do not use profiles that go beyond the strength
specification. Do not work on more than one piece at
a time. Use the machine only for the intended pur-
pose.
NOTE!
The material hardens a little bit more after each
pass.
When processing stainless steel, several passes
must be made because this material is work harden-
ing material.