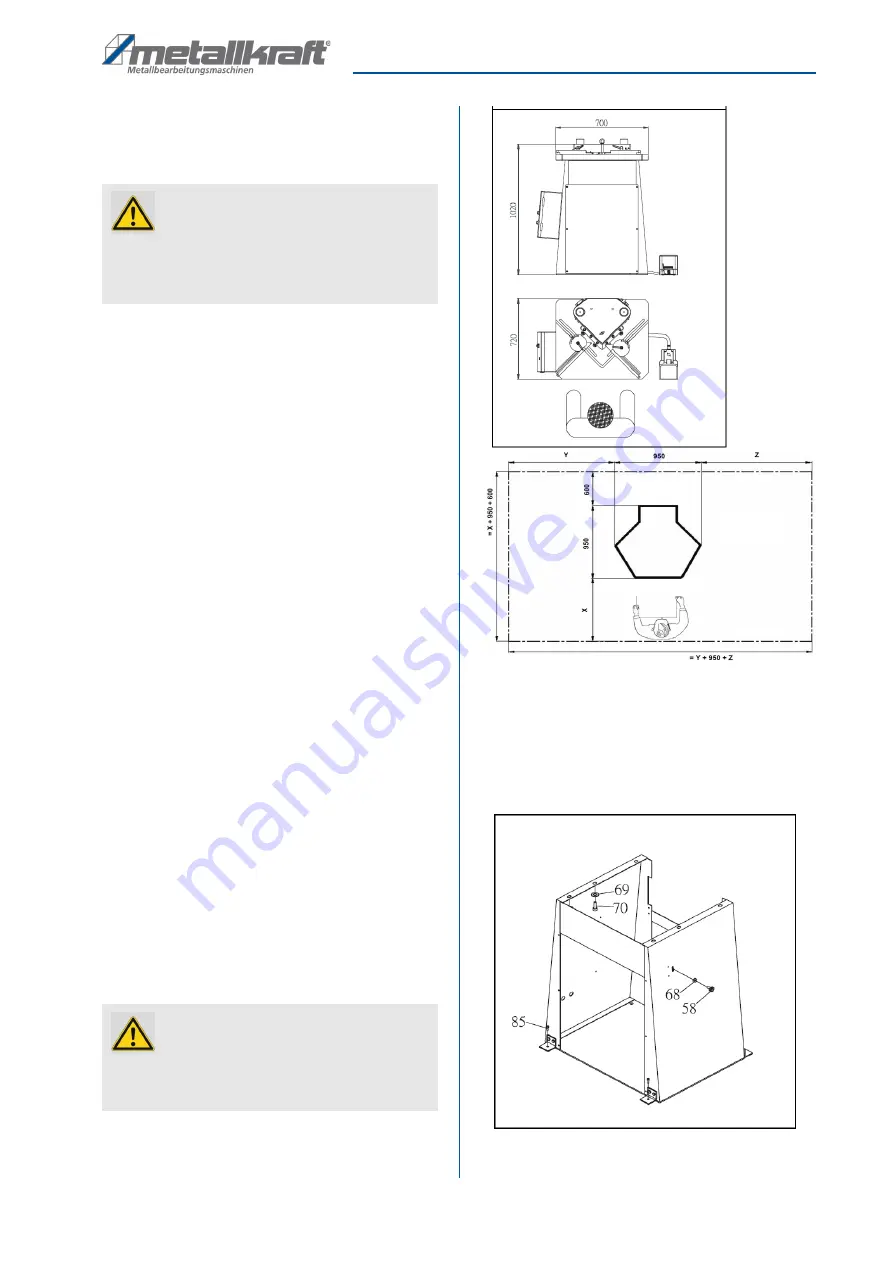
Setting up
AKM-Series 220 | Version 1.07
11
7 Setting up
7.1 Place of installation
In order to ensure good functioning of the notching ma-
chine and a long service life, the installation site should
meet the following criteria.
- The notching machine may only be installed and
operated in dry, frost-free, well-ventilated rooms.
- Avoid places near machines that cause chips or
dust.
- The place of installation must be vibration-free, i.e.
away from presses, planing machines, etc.
- The ground must be suitable for the work. Pay atten-
tion to the bearing capacity and evenness of the
ground.
- If necessary, protruding parts, such as support ta-
bles, etc., must be secured by on-site measures so
that persons are not endangered.
- Provide sufficient space for set-up and operating
personnel and material transport.
- Also consider accessibility for adjustment and
maintenance work.
- Provide adequate lighting (minimum value: 300 lux).
- The humidity should be in the range of 10% to 90%
and the measured room temperature should be bet-
ween max. 0°C - 50°C.
Setting up the machine:
Step 1: Make sure that the space around the machine is
sufficient for the application (Fig. 8). There must
be sufficient space for the operator and material
transport.
Step 2: Check each part of the machine for proper con-
dition before starting to set it up.
Step 3: Place the control foot pedal in the best position
for the application in front of the work area.
Fig. 8: Setup plan
Step 4: Remove the hexagonal head cap screws 85
(Fig.9).
Step 5: Use a crane to lift the machine from the pallet
and move it to the working position (Fig.10).
Fig. 9: Removing the fixing screws
ATTENTION!
Check the load-bearing capacity of the ground
before you install the machine. The installation place
must be capatable of bearing the weight of the
machine and the workpieces.
ATTENTION!
The machine is delivered unfilled. Before commis-
sioning, hydraulic oil must be filled into the tank.
Only use suitable hydraulic oil for refilling.
Stock area of
cutted material
Free clearance
space
Stock area of material
which will be cut
Free space for operation and
material feed/removal
Required minimum width
R
equi
re
d
mi
nim
um
depth
Summary of Contents for 3834200
Page 32: ...www metallkraft de ...