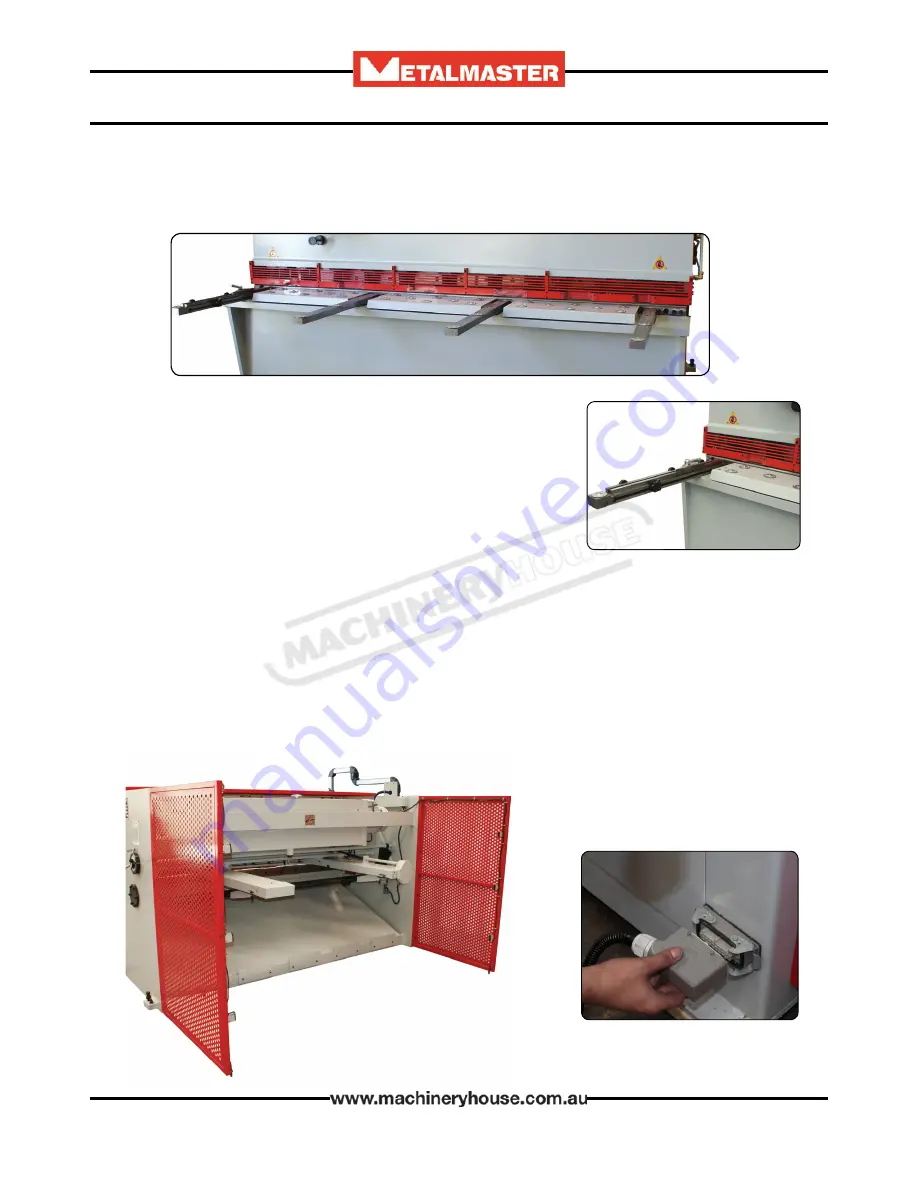
13
OPERATION MANUAL
Fig. 3.2
q
Place the squaring stops Fig 3.3 into position on the table top,
securing into place with the bolts supplied. Check that the square
stops are square to the blade. Adjust by loosening the bolts and
moving by the amount allowed by the clearance of the holes.
q
Re tighten the screws.
Fig. 3.3
3.4 ATTACHING THE ACCESSORIES.
q
Bolt the support arms onto the feed table. Ensure they are level and square to the table. (Fig 3.2)
q
Unpack and attach the rear fence to the back of the machine. Ensure that the sensors have been
connected and set up. (Fig.3.4)
q
Unpack the mobile foot control and plug the into the socket provided on the machine. (Fig.3.5)
Fig. 3.4
Fig. 3.5
Page 13
Instructions Manual for HG-4012 (S948)
12/02/2018