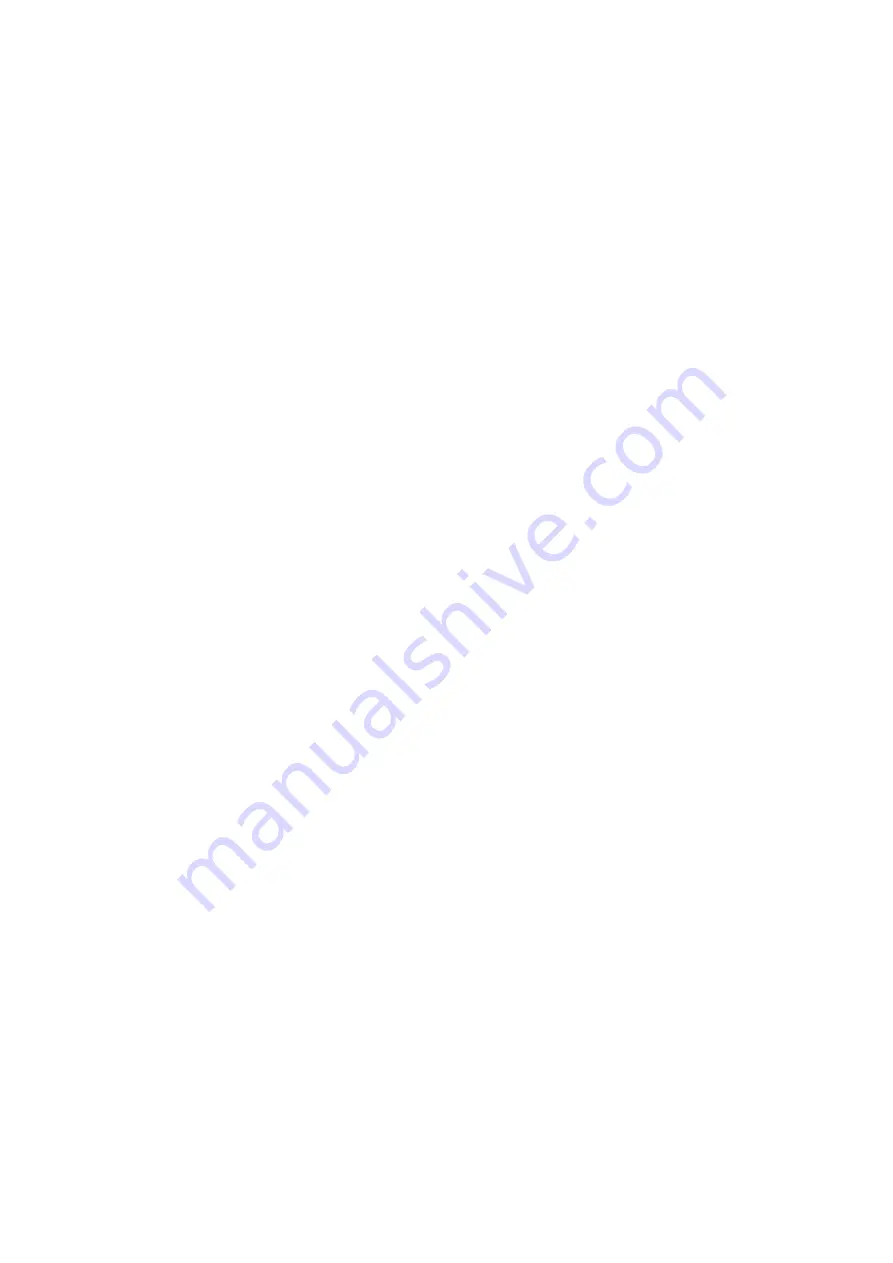
OMNIS sample rack – Housing
■■■■■■■■■■■■■■■■■■■■■■
92
■■■■■■■■
11.17 OMNIS sample rack – Housing
Materials
Lid
PBT
poly(butylene tereph-
thalate)
Enclosure
PBT
poly(butylene tereph-
thalate)
IP degree of protection
IP 40
11.18 Main modules – Connectors specifications
Energy supply
via power connection
Socket
IEC 60320, type C14,
10 A
Power cord
Length
max. 2 m
Number of conductors
3
with protective ground
Conductor cross-section
min. 0.75 mm
2
/ 18 AWG
Plug
Instrument side
IEC 60320, type C13,
10 A
Building side
country-specific
MDL
Metrohm Device Link
4 connectors
HID
Human Interactive Device
LAN
Local Area Network
Type
Ethernet CAT 6
Socket
RJ45
shielded
Cable type
(min. FFTP)
shielded
Cable length
max. 10 m
from Metrohm accesso-
ries