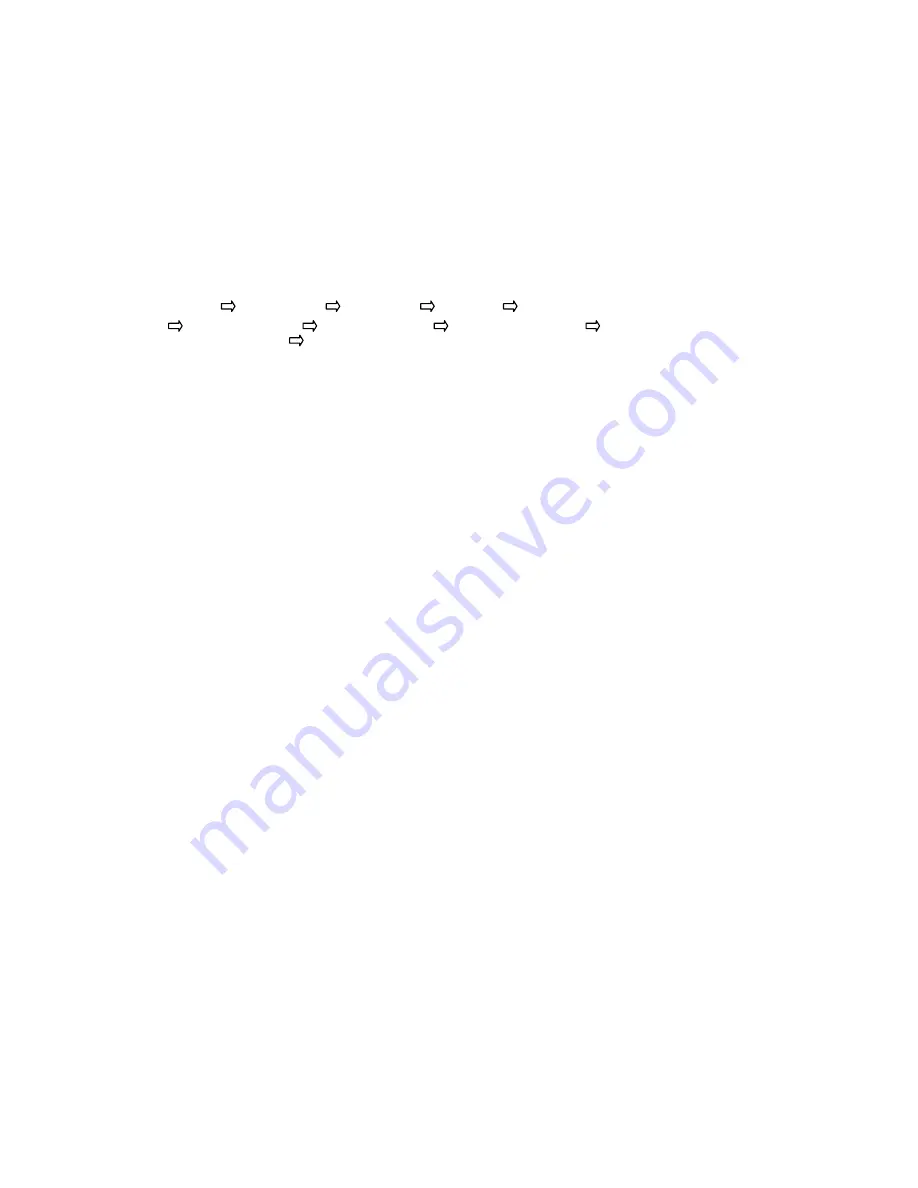
Page 3 of 34
File Name:
Doc#586p.docx
PART I: GENERAL INFORMATION
The basic function of the model FD4 Fire Pump Controller for diesel engine driven fire pumps is to automatically start the engine
upon a drop in pressure in the water main, or from a number of other demand signals. This controller provides automatic cycled
cranking, alarm and/or alarm shutdown protection for various engine failures. Stopping of the engine after the demand period is over
may be either manual or automatic. This controller also includes an automatic weekly test starting feature.
QUICK START FEATURE
The quick start feature prompts the user to set up quickly the essential screens for correct use of this fire pump controller. This
feature is initiated by pressing and holding the ‘3 PILOT push button for 2s. Then the following screens will be required to be
completed in the following order:
Start pressure Stop pressure
Delay start
Time
Date
Weekly start time Weekly start day
Commissioned date
Double skinned fuel tank Electronic Engine.
PART II: FUNCTIONS
Equipment is provided in the Controller to provide the following functions:
A.
Automatic Starting From:
a.
Drop in water line pressure
b.
Loss of battery charger output (if enabled)
c.
Operation of optional remote start switches, such as remote start switch, deluge valve switch, fire alarm switch, etc.
d.
Weekly test timer
B.
OID – Operator Interface Device - Provided for display of alarm functions, system pressure, battery volts, battery charger amps,
alarm conditions, etc. Includes a 4 line by 20 character LCD for display of system messages and programming.
C.
Auto-Off-Manual selector switch.
D.
Automatic Cranking - A microprocessor controlled crank cycle timer provides six (6) fixed crank periods separated by five (5)
rest periods each of approximately 15 seconds duration.
E.
Alarms and Signal Lights – Twenty Two (22) Standard lights are provided to give visual signals for;
"System Fault”, "Battery
#1 Healthy”
,
Battery #2 Healthy", "Charger #1 Failure"
,
Charger #2 Failure”, “AC Power Loss”, “Engine Running”,
"Engine Failed to Start"
,
"Engine Low Oil Pressure"
,
"Engine High Water Temp", "Engine Overspeed"
,
“Low Fuel”,
”ECM Failure”,”ECM Warning”,ECM Sw.in Alt.”, ”ECM Injection Fault”, “Fuel Tank Leak”,”Clogged Water
Strainer”,“High Cooling Water Temp”, “Low Engine Temp”, ”Contactor Coil Failure”,
and
“Pump On Demand”.
In
addition the mode buttons have LED’s on the button indicating
“Auto”, Manual”, “Test”,
or
“Off”
mode
.
2 additional lights,
configurable by the factory, can be provided for
"Pump Room Alarms"
. An audible alarm horn is mounted on the front of the
cubicle for sounding in the event of failure. Terminals are provided for remote failure indication of the following:
"Automatic Mode"
"System Fault"
"Engine Running (2 sets)"
"Common Battery Fault"
First Out Annunciation
This feature can be turned on via screen 313. The STND is no first out alarm sequence.
F3A:
This feature when turned on, will make the first alarm to occur fast flash, then all subsequent alarms slow flash. A first out
reset input is required, to clear the first alarm (Pilot pushbutton currently). Pressing the mute pb will turn all slow flashing alarms
to steady, First out alarm will slow flash.
F1A This feature when turned on, will make the first alarm to occur flash, then all subsequent alarms will show steady. A first
out reset input is required (Pilot pushbutton currently), to clear the first alarm. Pressing the mute pushbutton will silence the
mutable alarms, First out alarm will be on steady.