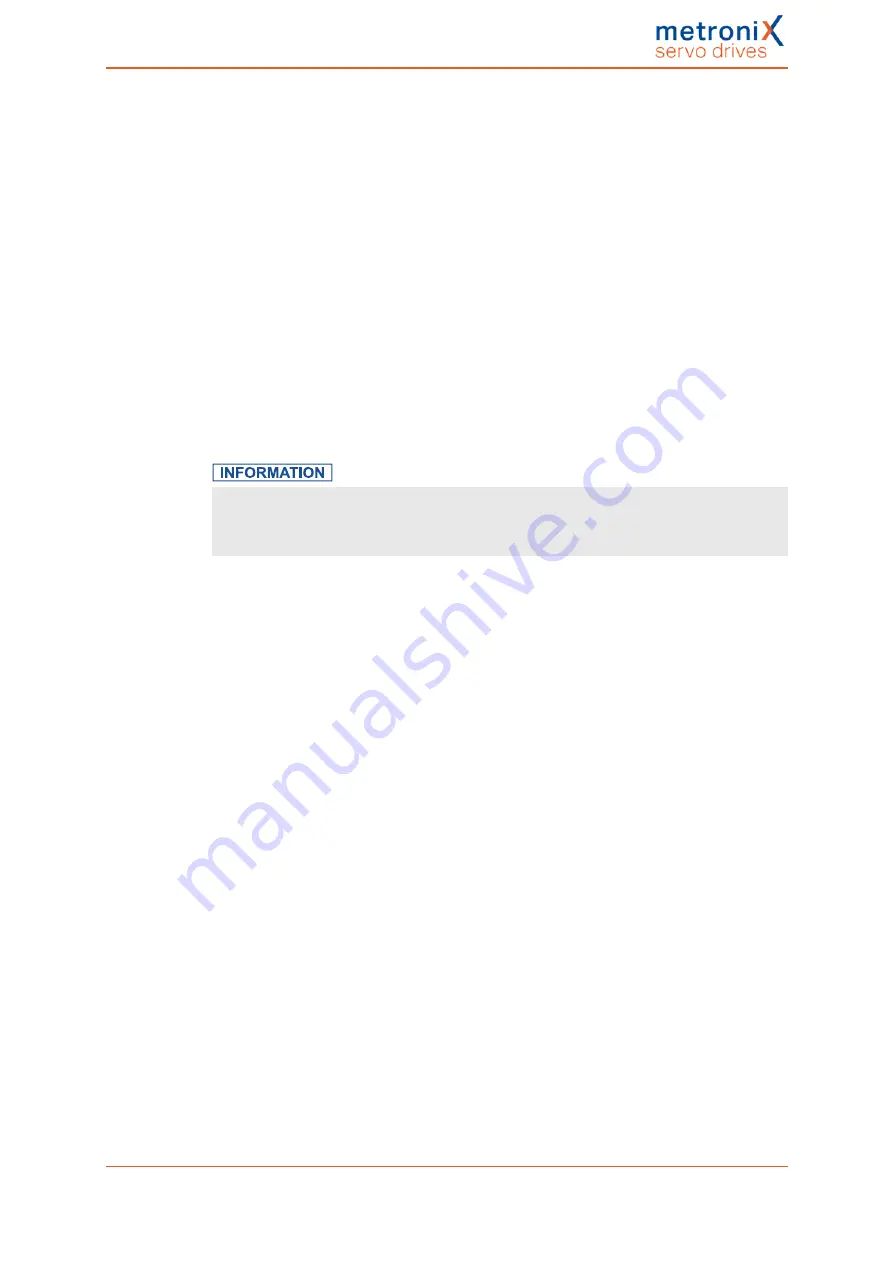
7 Additional settings
7.6.2
Configuration of the output stage
This menu (
Parameters/Device parameters/Power stage
) can be used to configure the
settings for the PWM generation by the output stage.
The option
Enhanced sine commutation
enables a better utilisation of the DC bus voltage
and, consequently, approx. 14% higher maximum speeds. In certain applications, the
control behaviour and the running characteristics of the motor may be impaired at very low
speeds.
Option
Half power stage frequency
: The clock frequency with regard to the current
controller cycle time t
i
can be halved.
With a lower clock frequency, higher limits for the maximum current are possible.
However, the motor may emit a singing noise. If you want the motor to run as quietly as
possible, select the full clock frequency. In addition, the losses in the motor are slightly
reduced if the full clock frequency is used (on the other hand, the losses in the servo drive
increase, which is why the adjustable maximum current limits are slightly lower). The
clock frequency has hardly any influence on the control behaviour.
Settings
The output stage must be switched off when the settings need to be changed.
In addition, the servo drive must be reset.
7.6.3
Use of linear motors
Numerous applications require a translatory motion to perform their task. Often, linear
axes are used for this purpose. They convert the rotatory motion of a standard servo drive
into the desired linear motion by way of toothed belt drives or ball-type linear drives.
However, these additional mechanical components lead to mechanical losses and are
subject the mechanical restrictions. This, in turn, has a negative effect on the process
cycle times.
Linear motors are part of the group of direct drives. They convert the supplied electrical
energy "directly" into a linear motion. If they are three-phase synchronous motors, they
can be used in combination with a BL 4100-C servo drive.
As it is always the case with synchronous servo drives, the commutation position must be
known before the drive is switched on for the first time. Due to its design, linear motors
use linear measuring systems. These are either absolute systems or purely incremental
systems. Purely incremental encoders do not supply the absolute position referred to one
electrical revolution so that a method for the automatic determination of the commutation
position must be applied when the servo drive is enabled.
Linear motors have a special design. As they are less compact compared to conventional
servo motors, their heat transfer capacity is reduced. This is why the usual i²t times for the
motor are shorter than in the case of conventional servo motors.
Linear motors can be divided into two groups: air-core and iron-core motors. Most motors
are air-core motors. This characteristic is relevant for selecting the method for determining
the commutation position.
Product manual BL 4000-C
Page 154 of 298