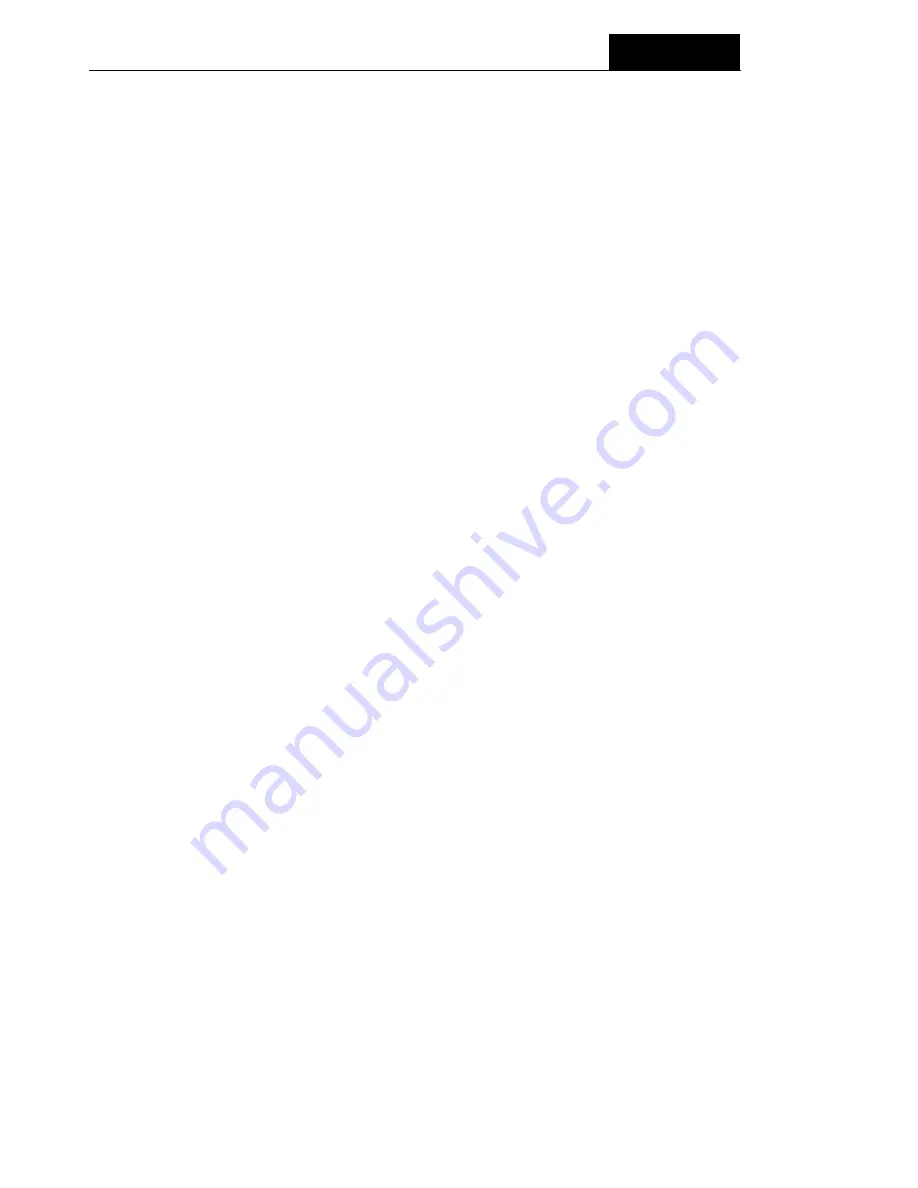
MP SERIES CONE CRUSHER TECHNICAL REFERENCE MANUAL
4-1
Countershaft, Ctrshaft Box & Sheave Assemblies
S
ECTION
4
4.1 Description
This section covers the countershaft box,
countershaft and crusher sheave assemblies. Power
is transmitted from the initial power source to the
countershaft through a V-belt or a direct drive. The
countershaft, which has a bevel pinion attached to
it, in turn drives the gear on the eccentric assembly.
The countershaft is supported within two sleeve
bearings or bushings. These bushings are pinned to
the countershaft box to prevent any possibility of
bearing rotation. The outer countershaft bearing
temperature is monitored by an RTD with a 4-
20mA signal. The spring-loaded probe on the RTD
makes direct contact with the bearing through a
compression fitting mounted in the countershaft
box. The flanges on the countershaft bushings
support the axial thrust loads from either the pinion
or the oil flinger. The oil flinger, keyed or pressed
to the drive end of the countershaft, removes the oil
from within the countershaft box by centrifugal
force. A housing covering the flinger is so designed
as to allow the oil to drain back to the Crusher for
reuse. The countershaft box has a force fit in the
main frame and is firmly held in place with large
diameter capscrews. An O-ring between the inner
mating surfaces of the box and frame, provides an
oil tight seal. A box guard protects that portion of
the countershaft box which is exposed to wear from
falling material.
4.2 Assembly Instructions
4.2.1 Countershaft Box Assembly
Installation
Procedures for assembling the various components
are given in the
Maintenance
portion of this
section. The countershaft box is to be installed in
the main frame as follows:
1. The countershaft box, countershaft, pinion,
bushings, oil flinger and flinger cover are
shipped fully assembled to make up the
countershaft box assembly. Also mounted on
the sheave end of the countershaft is either
the tapered sheave bushing or a safety set
collar for these Crushers that are direct drive
driven. Even though the end float was
factory set, sometimes during shipping the
end float is lost. Therefore the end float is to
be checked before the countershaft box
assembly is assembled to the Crusher. Refer
to Figure 4-17 for proper end float. It is
important for the proper operation of the
Crusher that the proper end float is
maintained. The countershaft must be free to
move in and out. To check the end float do
the following:
a. Pull the pinion end of the countershaft
until the oil flinger is tight against outer
countershaft bushing flange. Refer to
Figure 4-1.
b. Use a feeler gauge to measure the gap
(end float) between the pinion and
countershaft bushing. The end float
should be between 1.5 mm (0.060") and
0.8 mm (0.030"). If the end float is
correct proceed to step 2 if not proceed
to step c.
c. First loosen the sheave bushing clamp
screw, refer to Figure 4-1, and slide the
bushing off the countershaft. If necessary
insert a wedge (e.g. screwdriver) into the
bushing slit to aid in sliding the bushing.
If a safety set collar is mounted on the
countershaft just remove it.
d. On MP1000 Crushers remove the oil
flinger housing. Refer to Figure 4-3. For
the MP800 remove the countershaft box
cover. Refer to Figure 4-2.
e. If the gap is too small then heat the
flinger to a temperature of approximately
30°C (50°F) above ambient and bump
the sheave end of the countershaft until
the proper gap (end float) is obtained.
If the gap is too large then insert a feeler
gauge of proper thickness as specified in
step b between the pinion and
countershaft bushing. Next clamp the
pinion as shown in Figure 4-15. Then
heat the flinger as specified above and
push it until it is tight against the
countershaft bushing. Allow the flinger
to cool before removing the clamp and
feeler gauge.
Summary of Contents for MP1000
Page 1: ...Nordberg MP Series Cone Crusher ...
Page 2: ......
Page 4: ......
Page 6: ......
Page 8: ......
Page 64: ...SECTION 0 SAFETY 0 56 MP SERIES CONE CRUSHER TECHNICAL REFERENCE MANUAL ...
Page 66: ......
Page 74: ......
Page 154: ...Countershaft and Countershaft Box Callout Description 1 Countershaft 2 Countershaft box 1 2 ...