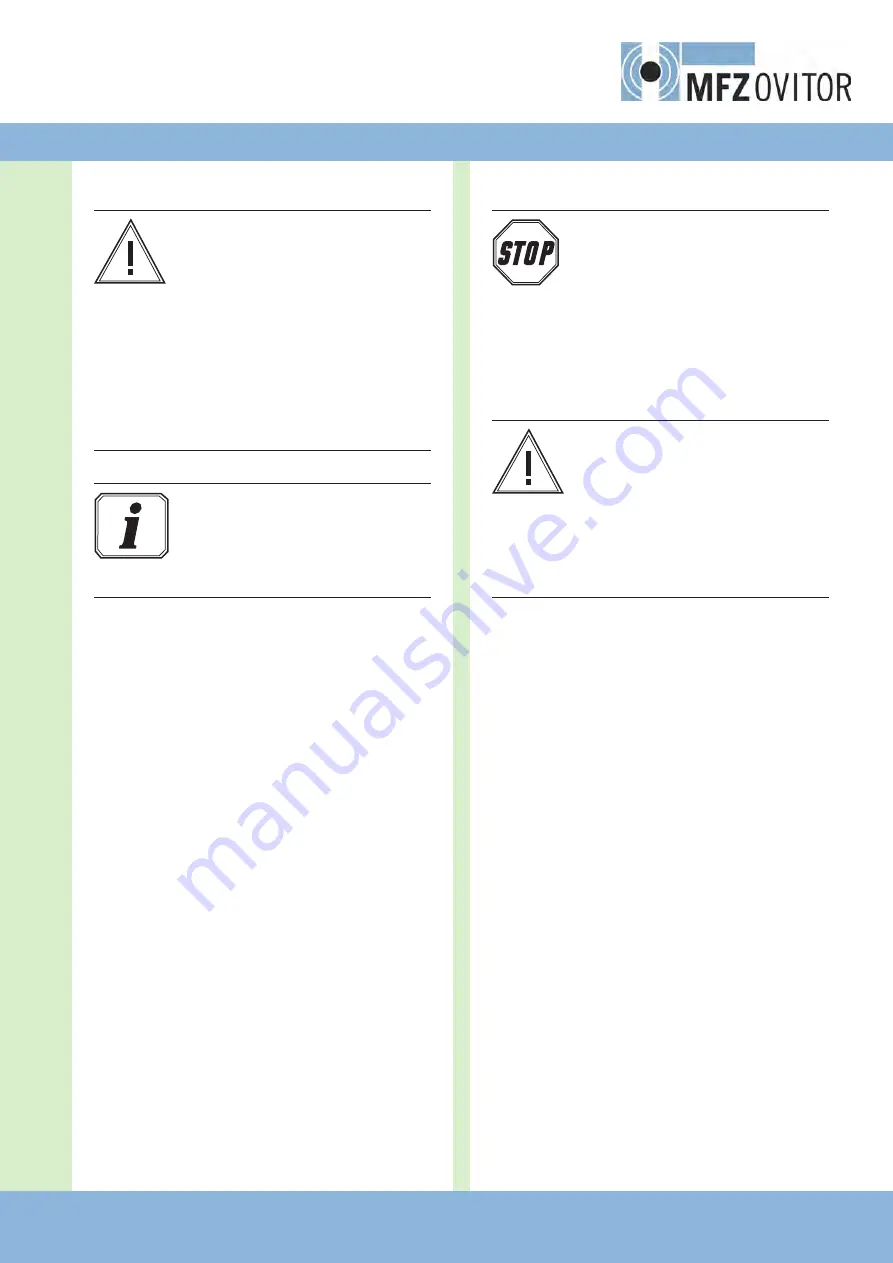
EN
CS 300 RM Gate Controls / Rev. B 1.0 – 5
5. Initial operation
5.1 General
Warning!
To guarantee that the equipment functions
properly, the following points must be
ensured:
The door is installed and operational.
- The MFZ tubular drive is installed and ready
for operation.
- The command and safety devices are instal-
led and ready for operation.
- The control housing with the CS 300 RM
control unit is installed.
Information:
For the installation of the gate/door, the MFZ
geared motor and the command and safety
devices, the relevant manufacturer’s instruc-
tions are to be adhered to.
5.2 Mains connection
Danger!
To ensure that the control unit functions pro-
perly, the following conditions must apply:
- The supply voltage must correspond to the
voltage shown on the type plate.
- The supply voltage must correspond to the
voltage of the door operator.
- If a permanent connection is to be made, an
all-pole mains switch must be installed.
Warning!
Before switching on the control unit for the
first time, check to ensure that the cabling
works are complete and that all the motor
connections are secure at both the motor and
the control unit. All control voltage inputs are
separated galvanically from the mains power
supply.